Exploring the Technical Intricacies of Casing Coupling Dimensions for Enhanced Drilling Efficiency
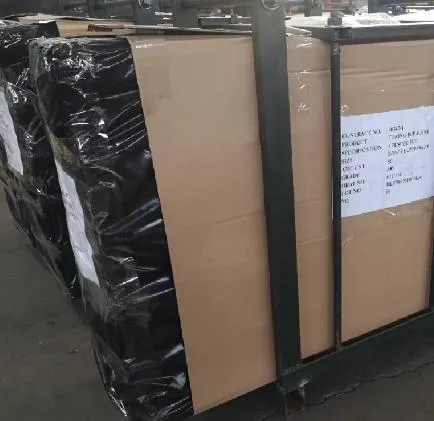
Understanding the precise dimensions of casing couplings is pivotal for those immersed in the oil and gas industry. These dimensions are more than just numbers; they are integral to the performance, safety, and longevity of drilling operations. This detailed discussion explores the complex nature of casing coupling dimensions, drawing from years of industry expertise and authoritative sources to provide a trustworthy guide for professionals in the field.
To begin with, casing couplings serve the essential purpose of connecting joints of casing pipe in drilling operations. Their role cannot be understated—they are the unsung heroes ensuring the secure transport of hydrocarbons from beneath the earth's surface. The dimensions of these couplings, including the outside diameter (OD), inside diameter (ID), length, and wall thickness, are crucial for delivering optimal performance under challenging conditions.
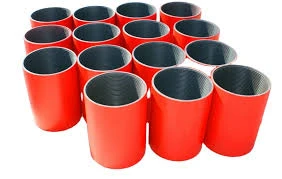
A critical factor influencing the choice of casing coupling is the drilling environment. Corrosive subterranean conditions necessitate materials with superior resistance, like stainless or specialty alloys, impacting dimension considerations due to material thickness and strength. The exterior and interior dimensions must accommodate these factors while maintaining structural integrity and meeting industry standards such as the American Petroleum Institute (API) specifications.
API standards, a key touchstone within the industry, establish rigorous guidelines ensuring uniformity and reliability in casing coupling dimensions. These standards are crafted from collective expertise and extensive research, offering a benchmark that aligns with the advanced needs of contemporary oil extraction environments. API 5CT, specifically, outlines the dimensions and tolerances for casings and couplings, ensuring compatibility and functionality across global operations.
Further expertise is demonstrated in the understanding of thread types used in casing couplings. Connection threads, like Buttress or API Round Thread, significantly influence coupling dimensions. For example, the Buttress thread provides a robust seal and efficient harvesting in high-pressure scenarios, demanding precise OD and ID dimensions to guarantee boltless integrity during stress.
casing coupling dimensions
Real-world deployment scenarios underscore the importance of precision in coupling dimensions. Field experts recount instances where deviations, even in minute millimeters, could lead to mismatches, causing stoppages and potential environmental hazards. These real-life insights inform the continuous improvement of not only casing design but also installation techniques, aligning with the exact specifications to avert costly production downtimes.
Experts agree that alongside dimensional accuracy, surface treatment of casing couplings is a critical consideration. Treatments like phosphating or copper coating, standard in many operations, offer enhanced protection against corrosion without altering the dimensions crucial for coupling performance.
The future of casing coupling dimensions is likely to see transformative enhancements driven by technology and materials science developments. With ongoing innovations such as automated dimension verification via advanced scanning technologies and AI-driven predictive maintenance systems, the industry is poised to achieve unprecedented levels of precision and reliability. Such advancements promise to refine coupling longevity and performance, setting new benchmarks for what can be achieved in energy extraction.
For industry professionals, understanding and leveraging this intricate knowledge about casing coupling dimensions is not merely beneficial—it is essential. It forms the cornerstone of ensuring that operations are conducted with engineering excellence, operational safety, and financial prudence. Recognizing the interplay between precise dimensions and overall system efficiency empowers decision-makers to optimize their drilling operations better, reducing downtime and maximizing resource extraction.
In summary, casing coupling dimensions encapsulate a universe of technical detail that impacts every facet of oil and gas drilling operations. By adhering to established standards, incorporating advanced materials and technologies, and maintaining stringent quality control, industry players can ensure their operations remain at the forefront of efficiency and safety. This refined understanding not only solidifies professional expertise but also inspires trust among stakeholders, paving the way for sustainable, successful energy production.