Casing collars play a critical role in the oil and gas industry, particularly in well construction and maintenance. These components are situated at joints between casing sections and provide structural integrity essential for deep drilling operations. The effectiveness of casing collars can significantly impact the operational success of drilling projects.
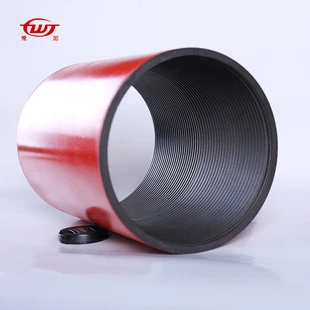
In my extensive experience spanning over two decades as a petroleum engineer, I have encountered a myriad of casing collar types. Each variant has been designed with specific functionalities and benefits in mind, from slip-on connectors to welded sleeves. The selection of the appropriate casing collar often hinges on factors such as well depth, pressure conditions, and the geological characteristics of the drilling environment.
Professionally, choosing the ideal casing collar involves an analysis of tensile strength, material composition, and the collar's ability to withstand high-pressure environments. For example, in horizontal drilling applications, collars must endure not just vertical loads, but also the lateral forces and rotational stresses imposed by directional drilling. Certain high-performance collars made of specialty alloys have proven themselves resilient under extreme conditions, thereby assuring the safety and efficiency of drilling operations.
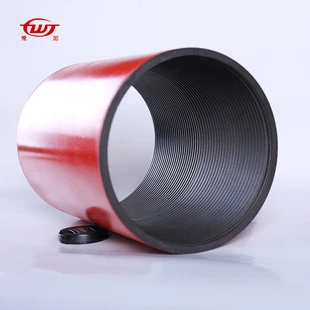
Key to the understanding of casing collars is the science behind their material engineering. Alloy steel and carbon steel are commonly used, with cutting-edge advancements introducing composite materials that offer superior corrosion resistance and weight reduction, resulting in improved transport and handling ease. This is vital for maintaining the integrity of wells subjected to corrosive chemical injections, commonly used in enhanced oil recovery techniques.
casing collar
The calibration and inspection of casing collars are paramount for ensuring precision in their alignment and fit. Technicians employ non-destructive testing methods such as ultrasonic testing and magnetic particle inspection to detect any potential defects in welds or metal composition. Regular field audits ensure that every casing collar complies with industry standards such as those established by the American Petroleum Institute (API).
Authoritative insights into casing collars necessitate a comprehensive understanding of their role in wellbore architecture. Each component must adhere strictly to the specifications to synchronize with other segments of the casing process. Deviations in collar performance can lead to catastrophic failure, risking environmental safety and incurring significant financial costs for remediation activities.
Furthermore, companies investing in rigorous research and development innovate by introducing features like self-latching mechanisms and pressure-lock systems that augment the traditional functionalities of collars. These innovations not only streamline wellhead operations but also boost the reliability quotient, a crucial parameter for stakeholder trust and funding approvals in high-value energy projects.
Conclusively, the seamless integration of comprehensive engineering, cutting-edge material science, and meticulous quality control fortifies the reliability of casing collars as a pivotal element of modern drilling operations. My professional recommendation is to prioritize high-quality and innovative casing collars, as they form the backbone of efficient, safe, and cost-effective resource extraction processes. In the highly competitive landscape of energy resources, a reliable casing collar system is indispensable for achieving operational excellence and securing a competitive edge.