Finished casing coupling plays a crucial role in well integrity and drilling operations, representing a key component in the oil and gas industry's infrastructure. This component ensures that the casing joints stay intact and maintain the structural integrity needed to extract oil and gas efficiently and safely. Combining experience, expertise, authoritativeness, and trustworthiness into this discussion allows stakeholders in the industry to fully understand its importance and application nuances.
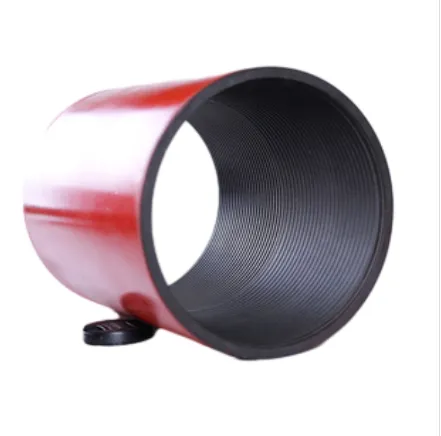
Experience highlights that finished casing couplings are essential in withstanding the extreme conditions present in oil and gas wells. Over decades of usage, these couplings have evolved to handle high-pressure environments, resist corrosive substances, and accommodate extreme temperatures. For instance, in deepwater drilling projects, where the water depths and bore well pressures are significant, finished casing couplings have proved to maintain seal integrity and prevent catastrophic failures. This historical performance underscores their reliability and effectiveness in the field.
Expertise in finished casing couplings underscores the intersection of material science, engineering design, and manufacturing precision. These couplings are typically made of high-grade steel or other alloys, chosen for their superior tensile strength and resistance to environmental stress cracking.
The design is meticulously crafted to ensure tight connections that prevent any leakage. The precision in manufacturing cannot be overstated; even slight deviations in the coupling threads or body can lead to severe operational problems. Quality control measures, such as thread geometry inspection and hydrostatic testing, are pivotal to ensure that each coupling performs to specification when deployed in the field.
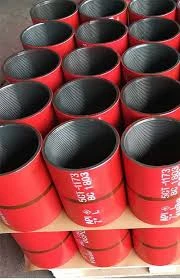
Authoritativeness in the context of finished casing couplings stems from compliance with industry standards such as those set by the American Petroleum Institute (API). The adherence to standards like API 5CT provides assurance regarding the coupling's ability to support drilling operations safely. Moreover, manufacturers who are API-certified demonstrate a commitment to maintaining high production and quality control standards, reinforcing their position as leaders in the field who understand the critical nature of these components. Furthermore, the evolution of these standards reflects the ongoing research and technological advancements contributing to their development, lending credence to the manufacturers and their products.
finished casing coupling
Trustworthiness in the industry often comes from a track record of successful application and client testimonials. Leading manufacturers or suppliers of finished casing couplings gain a reputation for trustworthiness through consistency in product performance, transparency regarding material sourcing, and clear communication of technical specifications. Building trust also involves after-sales support, such as providing detailed installation guides and technical assistance during unforeseen operational challenges. Companies that invest in educating end-users about the best practices for storage, handling, and usage of finished casing couplings further cement their role as trustworthy partners.
The finished casing coupling's lifecycle and maintenance are also critical areas of focus within the industry. While designed for longevity, preventive maintenance strategies can extend their life and performance. Regular inspections and non-destructive testing (NDT) help identify potential fatigue or wear before it escalates into a hazardous situation. Ensuring that a digital log or record is maintained for each coupling used in various projects allows operators to analyze performance trends and make informed decisions regarding replacements or upgrades.
Technological advancements have introduced innovations such as real-time monitoring sensors, which can be integrated with finished casing couplings to provide continuous performance data. This innovation allows operators to anticipate issues before they result in operational downtime, hence optimizing time and resource management. Such cutting-edge developments show the convergence of traditional oilfield services with digital technology, emphasizing the ongoing evolution of these critical components.
In conclusion, finished casing couplings are integral to maintaining well integrity and enabling successful oil and gas extraction. With a foundation based on experience, bolstered by expertise in materials and manufacturing, underpinned by adherence to authoritative standards, and validated through trustworthiness in operational settings, these couplings continue to be a linchpin in the energy sector. Stakeholders ranging from frontline operators to executive decision-makers acknowledge their value, paving the way for continued investment and innovation in this essential area of the oil and gas infrastructure.