The Role of Well Casing Coupling in Oil and Gas Drilling
In the intricate world of oil and gas drilling, every component plays a pivotal role in ensuring operational efficiency and safety. One such component is the well casing coupling, an often overlooked but crucial element that secures the sections of pipe used to line the borehole. This article delves into the significance of well casing coupling and its impact on drilling operations.
Well casing, also known as drilling pipe, serves as a protective barrier between the drilled formation and the drilling equipment. It prevents the walls of the borehole from collapsing and isolates different geological layers to avoid contamination. The casing is not a single, continuous piece but rather sections of pipe threaded together end-to-end. Here's where the casing coupling comes into play.
A coupling, also referred to as a collar or a connector, is essentially a short tube with internal threads on both ends that connects two lengths of casing. These are engineered to be robust and leak-proof, ensuring the integrity of the entire casing string. The quality of the coupling directly affects the strength and reliability of the well casing system.
There are various types of couplings, including weld-on, screw-on, and integral types, each serving specific applications based on the depth, pressure, and environment of the well. Weld-on couplings are joined to the casing by welding for increased strength, while screw-on couplings use threads for easier installation and removal. Integral couplings are formed as part of the casing itself during the manufacturing process, providing superior strength and corrosion resistance Integral couplings are formed as part of the casing itself during the manufacturing process, providing superior strength and corrosion resistance
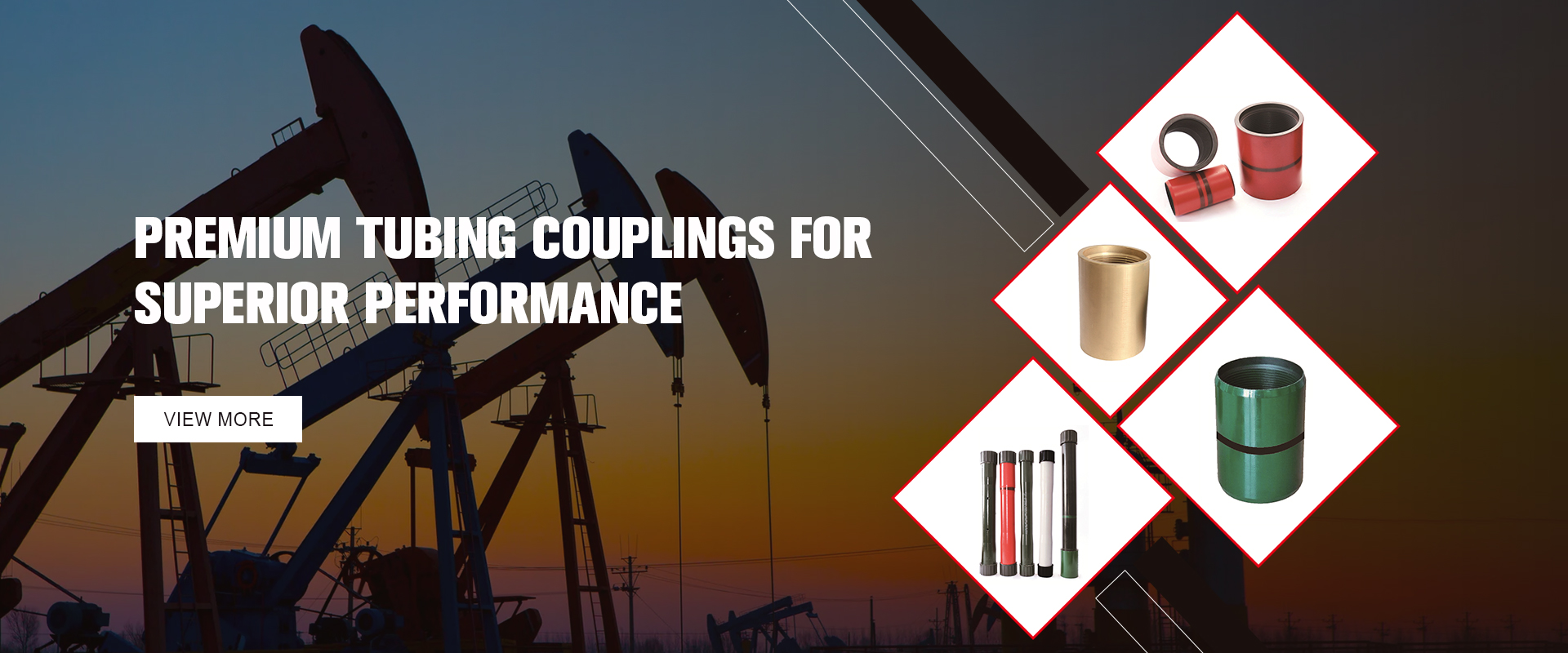
Integral couplings are formed as part of the casing itself during the manufacturing process, providing superior strength and corrosion resistance Integral couplings are formed as part of the casing itself during the manufacturing process, providing superior strength and corrosion resistance
well casing coupling.
The performance of a coupling is gauged by its ability to withstand the forces it encounters downhole. These include tensile loads from the weight of the casing, compression from the earth's movements, and the constant battle against corrosion from well fluids. A failure in the coupling can lead to costly workovers or even loss of the well, underlining the critical importance of their design and material selection.
In modern drilling practices, advancements in coupling technology have led to the development of premium connections. These offer improved sealing capabilities, torque control, and enhanced durability. Premium connections reduce the risk of thread damage and provide better pressure containment, which is essential in deepwater and high-pressure environments.
Furthermore, as drilling activities expand into more challenging terrains and deeper waters, the demand for sophisticated casing coupling systems grows. Innovations like metal-to-metal seals, advanced materials capable of withstanding harsh environments, and computer modeling to optimize thread designs are continually being developed to meet these challenges.
In conclusion, well casing couplings are unsung heroes of the oil and gas sector, silently safeguarding the integrity of drilling operations. Their reliable performance is paramount to the success of any drilling endeavor. As technology progresses, so too does the sophistication of coupling design, promising to enhance safety and efficiency in this vital industry.