Understanding the intricacies of casing coupling dimensions offers substantial benefits to those involved in the oil and gas industry, engineering, and construction. This component plays a pivotal role in ensuring the integrity and efficiency of piping systems across various applications. In this context, the focus is not merely on understanding the dimensional aspects, but also on ensuring compliance with industry standards, which directly influences operational success.
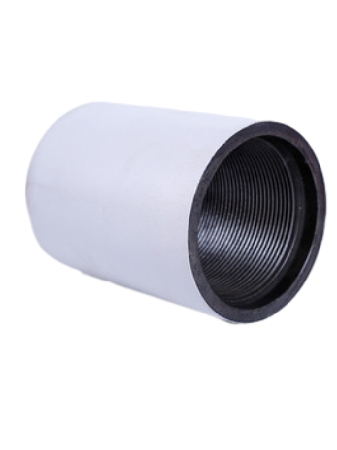
Casing couplings serve a critical function in the structural strength of any well system. These components are designed to connect casing joints in a seamless manner, and their dimensions can significantly impact the entire assembly's reliability. The dimensions you must consider include the outer diameter, the wall thickness, and the length of the coupling. Each of these parameters is governed by specific standards, such as those from the American Petroleum Institute (API) and International Organization for Standardization (ISO).
When considering outer diameter, what is crucial is the compatibility with casing tubes to ensure an effective seal and to minimize stress points along the string. Inadequately sized couplings might lead to leaks or mechanical failures, which can be both costly and dangerous. Typically, API standards classify casing sizes from 4.5 inches to beyond 20 inches, with couplings needing to align precisely with these measurements.
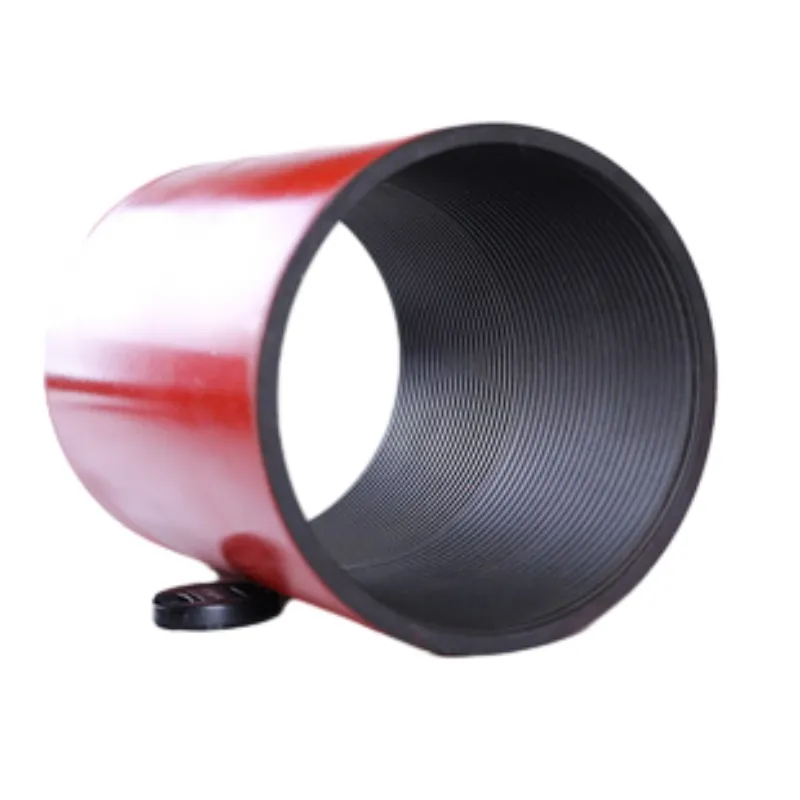
Wall thickness is another vital dimension that determines the coupling's ability to withstand external pressure and wear. This thickness is usually proportional to the diameter and is determined based on the environmental pressures and the weight of the casing. The weight per foot of the casing also influences coupling selection, as heavier casing requires more robust couplings to sustain the additional load.
Length of the coupling, surprisingly to some, is just as critical. A longer coupling may provide more stability, but its weight and potential impact on the flow dynamics within the casing need to be accounted for. Standard couplings range from short thread (STC) options to longer buttress thread designs, each tailored for specific operational conditions.
Expertise in selecting the right casing coupling dimensions is not solely about matching numbers but understanding the operational environment. Real-world experience shows that using incorrect dimensions can lead to operational inefficiencies. For example, in deepwater drilling scenarios, mismatched couplings could result in delayed project timelines due to unanticipated technical failures.
casing coupling dimensions
The authoritativeness of your selection process is strengthened by transparency and adherence to recognized standards. When procurement specialists or engineers choose certain coupling dimensions, documenting the decision-making process with reference to API and ISO specifications helps build a defensible position during audits or inspections.
Moreover, trustworthiness in the oil and gas industry is reinforced through rigorous testing and certification of casing couplings. Manufacturers should provide detailed datasheets and certificates indicating compliance to assure that each coupling meets specific standards for material quality and dimensional precision. This due diligence is crucial for maintaining operational integrity and safety.
Engaging with manufacturers who have a proven track record and offer comprehensive after-sales support can also enhance operational reliability. These partnerships ensure you have access to expert guidance on selecting the appropriate coupling dimensions for your particular application.
An experiential understanding of casing couplings comes from both field usage and historical data analysis. By reviewing reports from past projects and noting any issues that arose from coupling misalignments or failings, your team can develop a set of best practices. Such best practices might include periodic training sessions for engineers involved in the selection and installation of casing components, bridging the gap between theoretical knowledge and practical application.
In conclusion, the realm of casing coupling dimensions intersects with both engineering precision and operational pragmatism. True expertise is reflected in an ability to not only select the appropriate components but also anticipate and mitigate potential complications by thoroughly understanding both standard specifications and field conditions. This comprehensive approach not only assures safety and reliability but ultimately enhances the efficiency and profitability of your operations.