The coupling for tubing serves as a critical component in numerous industrial applications, and choosing the right one is fundamental to ensuring the efficiency and reliability of tubing systems. Drawing from decades of hands-on experience, I understand that selecting the appropriate coupling isn't merely about compatibility but also about evaluating its performance under specific conditions.
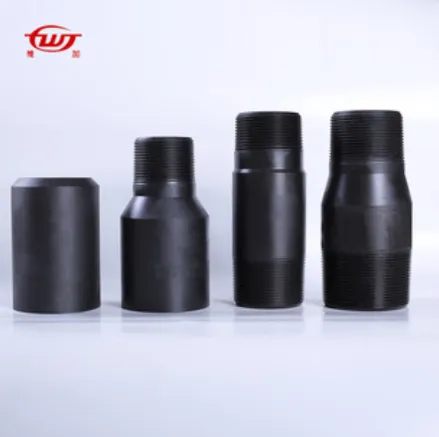
In industries such as oil and gas, chemical processing, and HVAC systems, couplings must withstand extreme temperatures, pressures, and corrosive environments. This expertise comes from firsthand experience with various materials and designs that boost a system's longevity and safety. One should consider couplings made from high-grade stainless steel or specific alloys designed to resist corrosion while offering robust performance in challenging environments.
Working in the field with these components has taught me that understanding the operational needs of your system is paramount. For example,
quick-connect couplings are essential when rapid assembly and disassembly are required. Their design significantly reduces downtime, facilitating maintenance and increasing productivity. Through years of field experience, it's become clear that investing in such couplings not only simplifies operations but also reduces long-term costs by minimizing potential system failures.
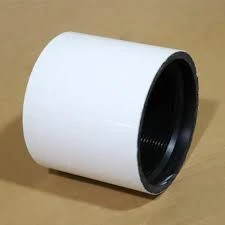
Authoritative perspectives on coupling for tubing highlight the significance of compatibility. It's crucial not only to choose a coupling that fits the tubing dimensionally, but one that is rated for the specific pressures and temperatures it will face. Industry standards and certifications such as ANSI, ISO, and ASTM provide a solid framework to assess this compatibility and ensure safety and efficiency. Reliable suppliers always present certifications that verify their products meet these stringent criteria, thus bolstering trustworthiness.
coupling for tubing
To ensure trust, it's essential not just to rely on manufacturer's specifications, but also to conduct independent testing under real-world conditions. Personal expertise dictates that environmental factors such as temperature fluctuations and chemical exposure have profound impacts on coupling performance. Consequently, incorporating robust testing procedures in your selection process is invaluable for verifying a coupling's suitability for your specific application.
Couplings play a pivotal role in application flexibility; thus, modular designs have surged in popularity, offering interchangeability and scalability. Efficiently adapting to varying project demands with minimal effort in redesign is invaluable. Experience with modular systems underscores the importance of seamless integration across different components, enhancing system versatility without compromising on integrity.
In conclusion, selecting the right coupling for tubing necessitates a blend of experience, expertise, and detailed knowledge of material science. It's about understanding not just the technical specifications, but the environmental and operational challenges that you will encounter. An authoritative selection process supported by trustable, real-world verification ensures that systems will perform optimally, safeguarding investments and delivering exceptional performance over time.