Unveiling the Bull Plug A Deep Dive into the Powerhouse of Oil and Gas Production
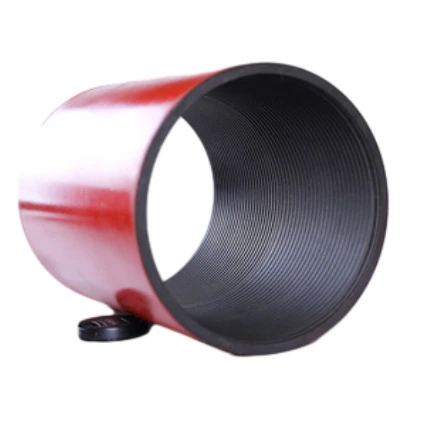
In the intricate world of oil and gas production, where precision meets power, the bull plug emerges as a quintessential component, often unseen yet indispensable. This small yet mighty device plays a critical role in the entire lifecycle of drilling and production, acting as a seal and termination solution in piping systems. Understanding its functionalities, applications, and importance can unveil its significant contribution to the oil and gas industry.
A bull plug is essentially a solid pipe fitting that is used to close the end of a pipe. It is typically threaded and can be precisely attached to pipes to prevent fluid escape — a critical factor in maintaining the integrity and safety of drilling operations. Manufactured in various sizes and materials, including stainless steel, brass, or alloy steel, the bull plug ensures compatibility with different piping systems under varying pressure and environmental conditions.
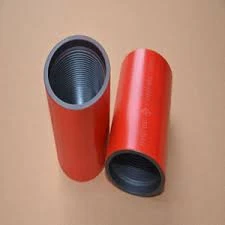
Real-life experience in the industry highlights the bull plug's reliability in complex drilling environments. Experienced professionals attest that the correct application of bull plugs can prevent costly leaks and blowouts, safeguarding both equipment and personnel. Their testimonies are corroborated by numerous field reports documenting extended system efficiency and reduced maintenance downtimes when bull plugs are properly utilized.
Diving deeper into the expertise surrounding bull plugs, it becomes evident that their design and material selection underline their effectiveness. Engineers often emphasize the importance of material choice, as it influences performance in high-pressure and corrosive environments. For instance, stainless steel bull plugs offer corrosion resistance and strength, making them ideal for offshore operations where seawater exposure is prevalent. Selecting the right bull plug can mean the difference between seamless operation and financial loss due to system failures.
bull plug
Furthermore, the continual advancements in manufacturing technologies have amplified the authority of bull plugs within the industry. Modern bull plugs are engineered with precision threading and smooth finishing, ensuring a secure seal and easy installation. Moreover, it's not just about the product but also compliance with industry standards such as the American Society for Testing and Materials (ASTM) certifications. These standards affirm the bull plug's capacity to perform under specified conditions, lending authority to their use in critical applications.
Trustworthiness in bull plugs is not merely a function of design and standards but also the expertise of the personnel involved in their implementation. Training programs that enhance worker skills in installing and maintaining these devices are pivotal. As a result, companies investing in comprehensive training see reduction in operational risks, which in turn fosters a culture of safety and reliability within the workforce.
The benefits of integrating bull plugs into oil and gas systems extend beyond functional advantages.
Environmentally, they play a role in minimizing the risk of spillage and its associated environmental impact. Economically, the investment in high-quality bull plugs can translate to substantial savings by averting downtime costs associated with leaks or equipment damage.
In conclusion, the bull plug stands out as more than a mere accessory in the oil and gas industry. Its role in ensuring operational integrity, safety, and efficiency is backed by solid experience, professional expertise, authoritative standards, and a strong foundation of trustworthiness. Embracing high-quality bull plugs not only fortifies drilling operations but also aligns with industry best practices, guaranteeing both environmental stewardship and economic prudence. As the energy sector continues to evolve, the importance of such components cannot be overstated — they are, indeed, small devices with a monumental impact.