Bull plugs, essential components in the drilling industry, are integral for maintaining the efficiency and safety of oil and gas extraction processes. These components, often underestimated in their importance, play a crucial role in the success of drilling operations. Drawing from years of experience in the industry, this article explores the intricacies of bull plugs, highlighting their application, significance, and the factors influencing their selection.
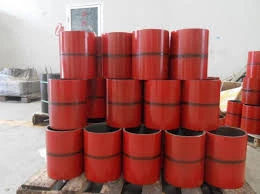
Bull plugs, typically fashioned from high-grade steel, are used to seal or terminate the end of a casing string in the drilling process. Their robust construction ensures that the integrity of the casing is maintained, even under extreme pressure conditions. This is particularly important in environments such as deep-sea drilling or high-pressure high-temperature (HPHT) wells, where the conditions can test the limits of even the most durable materials.
From an expert’s perspective, the choice of a bull plug must be guided by a thorough understanding of the well's conditions. For instance, the material of the bull plug must be chosen based on the chemical composition of the fluids it is expected to encounter. Corrosive environments require the use of bull plugs made from highly resistant alloys to prevent deterioration that could compromise well integrity.
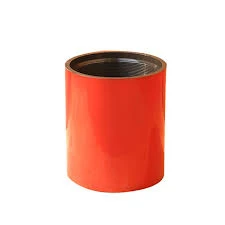
The structural engineering of bull plugs also showcases a blend of precision and innovation. Recent advancements have led to the development of bull plugs with enhanced threading designs, allowing for a more secure fit and reducing the risk of leaks. The advent of computer-aided design (CAD) has further refined the production process, ensuring that each bull plug meets the exact specifications necessary for optimal performance.
Using bull plugs effectively requires not only technical expertise but also a foundational knowledge of geology and well architecture. A drill operator must have the acumen to anticipate the stress impacts and thermal variances that might affect the bull plug’s performance. This involves a series of calculations and judgments, often under time-sensitive conditions, to ensure that every component, including the bull plug, aligns with the operational goals of the drilling project.
bull plugs
Trustworthiness in the manufacturing of bull plugs is another critical component. Reputable suppliers adhere to standards set by organizations such as the American Petroleum Institute (API) to assure consistency and reliability. Trustworthy manufacturers also provide certifications and documentation, reinforcing the authenticity and quality of their products.
Thus, selecting a bull plug from a seasoned manufacturer is as crucial as its application in the field.
Over the years, real-world failures and successes have shaped the development and improvement of bull plugs. Cases where inadequate bull plugs have led to well failures reiterate the importance of meticulous selection and testing. Conversely, stories of triumph, where well-chosen bull plugs have ensured the completion of drilling projects despite challenging scenarios, underline their value.
Looking towards the future, the role of bull plugs may evolve with technological advancements. Innovations in materials science propose the use of composite bull plugs, which promise enhanced resistance to environmental stresses while maintaining structural integrity. Moreover, the integration of IoT technology could allow for real-time monitoring of bull plugs, enabling operators to assess and respond to potential issues instantaneously.
In summation, bull plugs, while often a behind-the-scenes component, are pivotal in the orchestration of a successful drilling operation. Expertise in their selection and application, backed by reliable manufacturing processes, ensures not only operational efficiency but also the safety of all associated tasks. As the industry progresses, the evolution and adaptation of bull plug technologies will undoubtedly continue to mirror the advancing frontiers of oil and gas exploration.