Casing and tubing connections serve as the backbone of the oil and gas industry, ensuring safe and efficient extraction processes. These vital elements hold the drilling environment stable and secure as companies explore deeper wells and more challenging terrains. With increasing demand for energy, the role of robust casing and tubing connections becomes ever more critical.
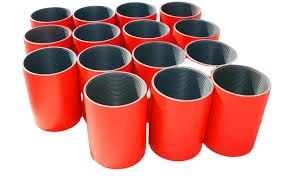
In the field of oil extraction, the choice of casing and tubing connections can significantly affect operational success and safety. Over the years, manufacturers have developed advanced connection technologies to meet diverse operational needs. A seamless design not only prevents leaks but also ensures that the equipment withstands high pressures and temperatures prevalent in deep drilling operations.
The performance of casing and tubing connections largely depends on the mechanical reliability. Strength and durability are paramount, ensuring that connections can endure the complex stresses encountered during drilling and production. Modern designs incorporate threaded connections with ultra-high-tensile strength and superior sealing capabilities. Opting for high-quality threaded connections can drastically reduce the likelihood of operational failures.
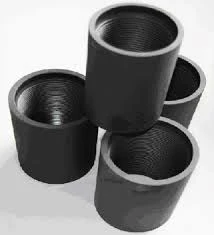
For experts in the field, recognizing the differences between casing and tubing connections can optimize drilling operations. Casing connections typically involve larger diameters, designed to stabilize the borehole and prevent collapse. They act like a protective layer, supporting the surrounding geology and isolating different pressure zones. Tubing connections, on the other hand, are smaller in diameter, facilitating the flow of oil or gas to the surface.
Seamless integration between these connections ensures operational efficiency and safety.
Manufacturers have invested heavily in research and development to produce high-performance connections that can adapt to various environmental challenges. With the rise of unconventional oil extraction methods, such as shale gas and tight oil, the need for more sophisticated connections has become apparent. Hence, the industry is witnessing a paradigm shift toward the adoption of premium connections known for their thread strength, multiple-seal systems, and anti-corrosive properties.
casing and tubing connections
In terms of expert recommendations, choosing connections with certified performance capabilities is a wise approach. Compliance with industry standards, such as those from the American Petroleum Institute (API), ensures that products meet stringent quality requirements. These standards are designed to guarantee that connections can handle the mechanical and hydraulic loads anticipated during their lifecycle.
Another critical factor is the installation process of casing and tubing connections. A proper make-up and the use of specialized tools prevent premature wear and tear. Experienced technicians understand the nuances of torque applications and proper alignment, both crucial to achieving the intended joint integrity and longevity.
Moreover, the aspect of maintenance in extending the life of casing and tubing connections cannot be overstated. Regular inspections, using modern non-destructive testing methods like ultrasound or electromagnetic testing, can detect early signs of wear or potential failure. Addressing these issues promptly can save projects from unplanned downtimes and costly repairs.
From a safety standpoint, casing and tubing connections are integral in establishing an effective blowout prevention system. In high-pressure wells, these connections prevent catastrophic releases of oil and gas, protecting human lives and the environment. Modern anti-galling technologies and torque-turn monitoring further enhance the safety of these connections, making them essential in high-stakes drilling operations.
Investing in high-quality casing and tubing connections represents not just a financial consideration but a strategic decision that impacts the entire lifecycle of well operations. Their significance is underscored by the necessity for ongoing innovations to meet the energy demands of the future. As the industry evolves with new challenges, such expertise and experience ensure reliability and operational excellence in the ever-competitive landscape of oil and gas extraction.