Coupling blanks are an essential component in various industrial applications, offering unique advantages that make them indispensable in certain scenarios. As a seasoned professional in the field, my experience with these components has highlighted their critical role in ensuring efficient and reliable mechanical connections. This article explores the multifaceted benefits and applications of coupling blanks and provides insights into their expert handling and integration.
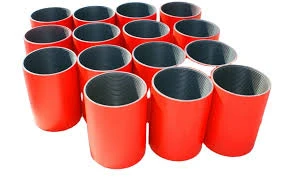
In industrial settings, the precision and reliability of mechanical connections can often mean the difference between seamless operation and critical failure.
Coupling blanks serve as an intermediary in situations where precise alignment and secure fit are paramount. These components are often utilized in settings where specific diameters or lengths are required but not readily available in standard inventory. Their versatility allows for custom modifications that meet exact specifications without sacrificing performance or structural integrity.
Expertise in the selection and application of coupling blanks can significantly enhance operational performance. When integrated properly, these components can reduce mechanical stress, increase transmission efficiency, and extend the lifespan of the machinery. This is particularly beneficial in manufacturing environments where downtime and maintenance costs can severely impact productivity and profitability. The ability to customize coupling blanks ensures that machines perform at their optimal capacity, thus saving on repair and replacement costs in the long term.
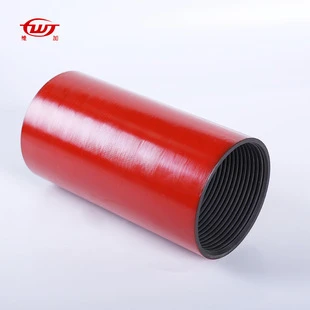
One of the standout features of coupling blanks is their adaptability across a variety of materials. Depending on the application's demands, coupling blanks can be produced from materials such as steel, aluminum, or advanced composites, each offering distinct advantages in terms of strength, weight, and resistance to environmental factors. This flexibility allows engineers to tailor their use to the specific environmental conditions and mechanical requirements, ensuring a seamless fit and optimal performance.
coupling blank
The authority in the deployment of coupling blanks lies not only in their material versatility but also in their size adaptability. Custom-sizing capabilities mean that coupling blanks can be manufactured to fit any unique industrial requirement. This is particularly beneficial in complex machinery setups where off-the-shelf solutions may fall short. By providing a bespoke solution, coupling blanks ensure machinery runs without the hitches that can often arise from incompatibly fitted components.
Trustworthiness in the use of coupling blanks is bolstered by rigorous quality control measures. These components are typically subjected to stringent testing to ensure they meet industry standards and can withstand the stresses of their intended applications. High-quality coupling blanks are designed to endure significant loads and resist deformation over time, providing a reliable solution for industrial needs. This level of reliability is crucial, as it instills confidence in operators and engineers that the machinery will perform consistently, thus avoiding disruptions and ensuring safety in the workplace.
Overall, coupling blanks are indispensable in achieving precision, efficiency, and reliability in industrial mechanical systems. Their ability to be customized to exacting specifications, adaptability across various materials, and stringent quality assurance processes make them a preferred choice for professionals across industries. For businesses seeking to maintain competitive advantage through streamlined operations and reduced maintenance burdens, coupling blanks present a compelling solution.
In sum, coupling blanks offer a blend of expertise, authority, and trustworthiness that is hard to beat. Whether one seeks to improve existing systems or implement new ones, these components provide the necessary adaptability and reliability. As industries continue to evolve, the application of coupling blanks will undoubtedly remain an integral aspect of efficient, state-of-the-art mechanical systems.