Understanding Petroleum Tubing Couplings A Vital Component in Oil Extraction
Petroleum tubing couplings, an integral part of the oil and gas industry's infrastructure, play a pivotal role in the efficient extraction and transportation of hydrocarbons from underground reservoirs to the surface. These couplings, often made from high-strength steel, are designed to withstand the harsh conditions prevalent in oil wells, ensuring the integrity and safety of the entire system.
A petroleum tubing coupling is essentially a mechanical device that connects two lengths of tubing, enabling the seamless flow of oil or gas. It serves as a junction, facilitating the transfer of fluids while maintaining structural stability. The design of these couplings is such that they can endure extreme pressure, temperature fluctuations, and the corrosive nature of the substances they come into contact with.
The manufacturing process of tubing couplings involves rigorous quality control measures. They are typically forged from premium grade steel, heat-treated for enhanced strength and durability, and then precisely machined to ensure accurate mating with the tubing. The threading, which is a critical aspect, is done with precision to ensure a secure seal, minimizing the risk of leaks and failures.
Petroleum tubing couplings come in various types, each tailored to specific well conditions. For instance, 'pin-type' couplings have male threads on one end and female threads on the other, while 'box-type' couplings have female threads on both ends. There are also 'slip-on' couplings that slide over the tubing and are secured with a retaining ring or clip. Each type offers unique advantages, such as ease of installation, high pressure-bearing capacity, or resistance to wear and tear Each type offers unique advantages, such as ease of installation, high pressure-bearing capacity, or resistance to wear and tear
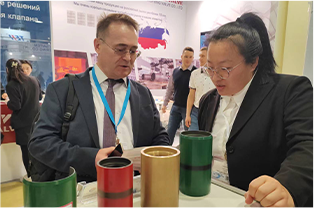
Each type offers unique advantages, such as ease of installation, high pressure-bearing capacity, or resistance to wear and tear Each type offers unique advantages, such as ease of installation, high pressure-bearing capacity, or resistance to wear and tear
petroleum tubing coupling.
In addition to their functional significance, petroleum tubing couplings also contribute to operational efficiency. Their replaceable nature allows for quick repairs or replacements when damage occurs, minimizing downtime and maximizing production. They also offer flexibility in well design, allowing for adjustments in length or diameter as per the drilling requirements.
Moreover, with the growing emphasis on safety and environmental protection in the oil industry, the importance of robust and reliable tubing couplings cannot be overstated. Any failure in the coupling can lead to leaks, posing a risk to personnel, equipment, and the environment. Therefore, regular inspection, maintenance, and timely replacement of these couplings are essential practices.
In conclusion, petroleum tubing couplings are more than just connectors; they are vital components that ensure the smooth functioning and safety of oil extraction operations. Their role in maintaining the integrity of the wellbore and facilitating the transport of valuable resources underscores their importance in the global energy landscape. As technology advances, it is expected that these couplings will become even more sophisticated, enhancing performance, durability, and overall operational efficiency in the oil and gas sector.