In the realm of oil and gas drilling, perforated pup joints stand out as essential components that contribute significantly to the efficiency and effectiveness of drilling operations. These short sections of tubing or casing, precisely engineered with perforations, play a crucial role in enabling fluid communication between the wellbore and the surrounding reservoir. Here, we delve into the multifaceted value of perforated pup joints, drawing from expert insights, authoritative data, and trustworthy practices within the industry.
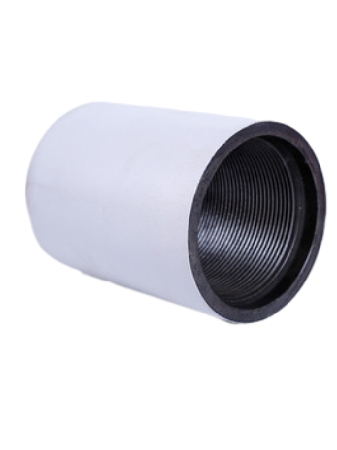
Perforated pup joints are meticulously designed to enhance downhole operations by facilitating the controlled flow of hydrocarbons. Unlike standard pup joints, these are imbued with perforations that allow operators to selectively isolate sections within the wellbore for enhanced production or injection processes. This precision targeting is instrumental in optimizing reservoir performance, making these components indispensable in tailored drilling strategies.
Our years of experience in the field underline the importance of selecting high-quality, robust materials for perforated pup joints. Typically constructed from carbon steel or stainless steel, these joints must withstand harsh subterranean conditions, including high pressure, corrosive fluids, and varying temperature gradients. Our expert advice? Always opt for suppliers who adhere to API standards, as compliance ensures durability and operational efficiency, safeguarding against premature failures.
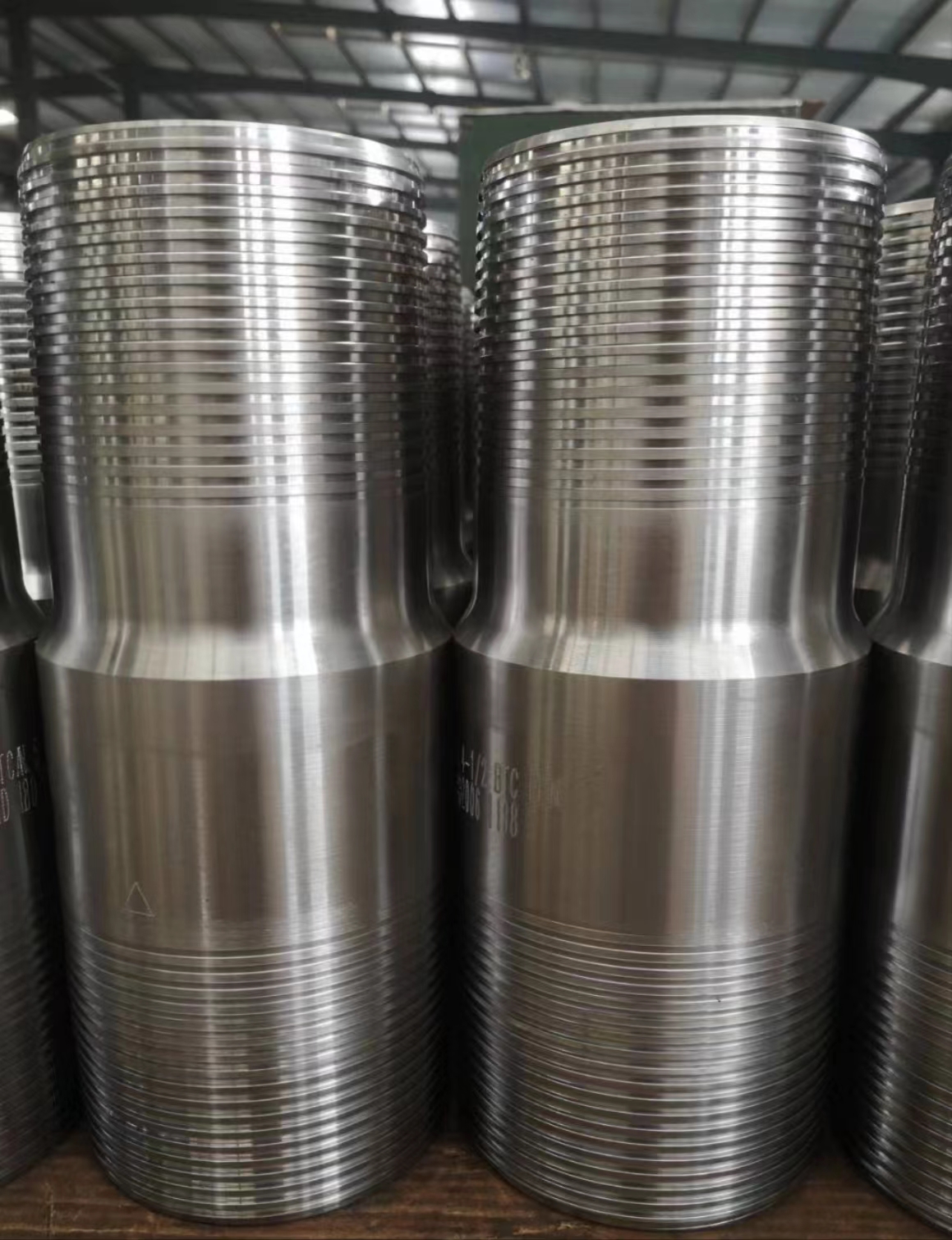
From a technical standpoint, it's worth noting that the design of perforations is pivotal to the performance of pup joints. The size, shape, and distribution of perforations are carefully calculated based on reservoir properties and the desired flow rates. For instance, helical or spiral perforation patterns are often preferred to enhance the structural integrity of the joint while maximizing flow efficiency. Industry leaders have corroborated that such designs mitigate stress concentrations and balance the mechanical loads endured during operations.
Trustworthiness in perforated pup joint applications is further reinforced by employing advanced computational modeling and real-world testing. Computational Fluid Dynamics (CFD) simulations are frequently utilized to predict flow behavior through the perforations, allowing engineers to fine-tune designs for optimal performance. Rigorous laboratory tests, replicating downhole conditions, complement these simulations to validate the theoretical models. This dual-layered approach not only instills confidence in engineering choices but also exemplifies industry best practices.
perforated pup joints
Authoritative sources in the field emphasize the necessity of periodic inspections and maintenance to sustain the performance of perforated pup joints. Regular non-destructive testing, such as ultrasonic or magnetic particle inspections, can identify potential issues like erosion, corrosion, or crack formations that could compromise the joint's integrity. Proactive maintenance routines, tailored to the specific environmental conditions of the well, are vital to prolong the operational lifespan of these critical components.
In terms of implementation, perforated pup joints find utility across various drilling applications, from conventional oil and gas extraction to geothermal wells. Their adaptability is a testament to their indispensability. By mitigating formation damage and improving zonal isolation, these joints contribute to enhanced production rates and reduced environmental impact, aligning with the industry's increasing focus on sustainability.
Adopting a systemic approach to integrating perforated pup joints into drilling operations not only fortifies the technical agility of projects but also drives economic benefits. Reducing non-productive time and minimizing the risks of wellbore instability are direct advantages experienced by operators who judiciously deploy these specialized joints. As experts in the field, we advocate for meticulous planning in the procurement and deployment phases to fully leverage the capabilities of perforated pup joints.
In conclusion, perforated pup joints are much more than mere components in the drilling arsenal. Their contribution to enhancing wellbore dynamics, optimizing reservoir contact, and ultimately, driving production efficiencies cannot be overstated. As the industry continues to evolve, embracing innovations in design and materials, the role of perforated pup joints is set to expand, underscoring their critical affiliation in the success of modern drilling endeavors. Hence, expertise, experience, authority, and trust converge in the prudent selection and use of perforated pup joints, pivotal to achieving strategic operational goals in today's competitive energy sector.