Pump seating nipples are crucial components in artificial lift systems used primarily in the oil and gas industry. These devices play a pivotal role in ensuring efficient and reliable oil extraction, aligning with modern needs for optimized energy resource management. Drawing upon decades of experience and a profound understanding of well operations, we delve into the intricacies of pump seating nipples, emphasizing their role, material considerations, design advancements, and installation best practices.
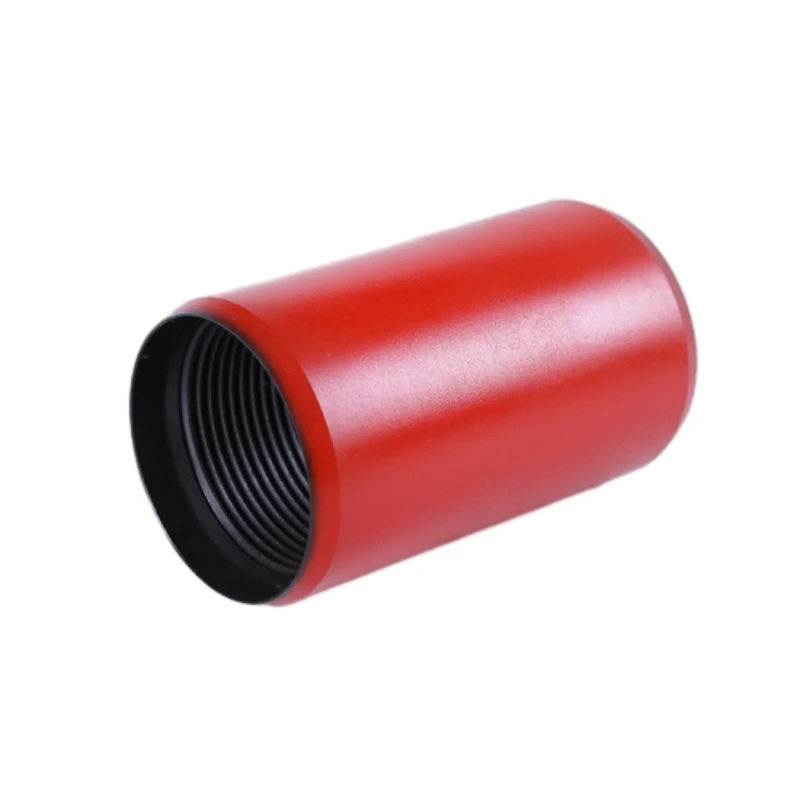
Pump seating nipples serve as the anchor point for downhole pumps, ensuring they are securely positioned in the wellbore. The integrity and functionality of these components directly impact the performance of the entire well system. Through extensive field experience, it has been observed that the choice of material is imperative for their longevity and resistance to harsh environments. Historically, high-strength steel alloys have been preferred due to their durability and resistance to corrosion. However, with advancements in metallurgy, more resilient and lightweight composite materials are being explored, offering a promising future for enhanced performance and reduced operational costs.
In discussing expertise, it's important to consider the advancements in the design of pump seating nipples. Traditional designs have been significantly improved to accommodate higher pressures and temperatures encountered in deeper wells. These improvements are often the result of meticulous research and development by skilled engineers. The introduction of precision machining and advanced coating technologies has further optimized these components, ensuring smooth operations and reduced downtime. Moreover, manufacturers are increasingly customizing designs to meet specific operational requirements, further underscoring the need for expertise in the manufacturing process.
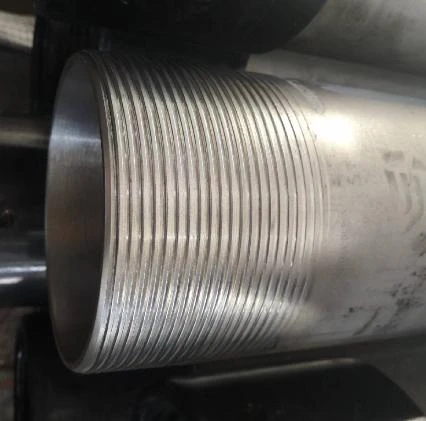
Authoritativeness in this domain is demonstrated by continual collaboration with industry leaders and adherence to international standards. Regulatory bodies and expert panels regularly update guidelines to ensure safety and efficiency in oil extraction processes. Reliability and consistency are non-negotiable, given the financial and environmental stakes. Companies that produce pump seating nipples typically hold certifications reflecting their compliance with these stringent standards, reinforcing their credibility and commitment to quality assurance.
pump seating nipple
Trustworthiness is built through a track record of successful deployments and case studies demonstrating tangible results. Numerous oil fields worldwide have reported marked improvements in production efficiency and equipment lifespan following the integration of advanced pump seating nipple designs. These success stories are not merely anecdotal; they are backed by statistical data and rigorous analysis, offering a compelling testament to the trustworthiness of current innovations in this field.
Installation of pump seating nipples requires a comprehensive understanding of the well's specifications and the operating conditions. Experienced technicians are crucial as they bring a wealth of practical knowledge to the table, ensuring every installation accounts for individual well parameters. Proper installation is vital to prevent issues such as misalignment, which can lead to inefficient pumping and premature equipment wear. Training programs are commonly provided by manufacturers to ensure that field personnel are equipped with the necessary skills and knowledge.
In conclusion, pump seating nipples are a lynchpin in the productivity of oil extraction operations. Their evolution reflects a remarkable interplay of experience, expertise, authoritativeness, and trustworthiness. The oil and gas industry continues to rely heavily on meticulous design, material science innovations, and precise installation methods to optimize these elements. As the world pivots towards more sustainable energy solutions, ongoing innovations in pump seating nipple technology ensure that current resources are being extracted in the most efficient and environmentally conscious manner possible. Companies prioritizing these components will find themselves at the forefront of a competitive industry, fortified by robust operational systems.