Tubing crossovers may not be the most glamorous component in the oil and gas industry, but their role is absolutely crucial. These specialized connectors allow for the seamless integration of different tubing strings in wells, enhancing operational flexibility and efficiency. In industries where precision and reliability are paramount, understanding the nuanced functions and benefits of tubing crossovers is vital.
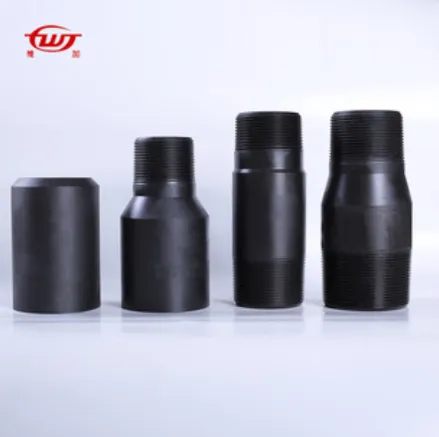
To begin with, tubing crossovers facilitate a crucial transition between different sections or diameters of tubing used within a well. Their precise engineering ensures that despite transitioning between potentially different sizes or specifications, the seal and structural integrity of the tubing string is maintained. This is particularly important given the extreme pressures and conditions often found in subterranean environments.
Product expertise and experience count hugely in the selection and application of tubing crossovers.
Expertise in metallurgy and engineering plays a significant role in designing these components. Crossovers are constructed from high-strength materials such as stainless steel, Inconel, or other specialized alloys that withstand corrosion and high pressure. These metals are chosen based on the specific chemical composition of the well fluids and gases they're exposed to, ensuring prolonged service life and reliability.
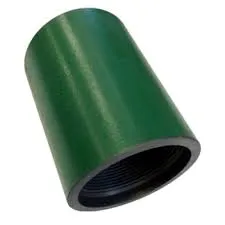
Professionals in the field with years of hands-on experience frequently emphasize the importance of precision in the machining of these crossovers. The threads that connect crossovers to tubing sections must meet stringent API or other industry standards to ensure a secure connection. Even a minor imperfection in the threading can result in catastrophic failures, incurring significant financial and environmental costs.
tubing crossover
In addition to function and material consideration, the installation of tubing crossovers also requires authoritative oversight. Trained technicians, often guided by strict procedural standards and quality checks, handle their installation. Proper torque application during the makeup process is critical to prevent over-tightening, which can lead to thread galling, or under-tightening, which may cause leaks. The use of digital torque gauges is now standard practice in the industry to ensure precision.
From a reliability perspective, non-destructive testing (NDT) is often employed both in the manufacturing phase and prior to installation. Techniques such as ultrasonic testing or magnetic particle inspection help verify the integrity of the crossovers, ensuring there are no material flaws or cracks that could propagate under stress.
Trustworthiness and industry regulation compliance serve as the foundation for any authoritative product discussion. All quality tubing crossover manufacturers adhere to relevant international standards such as those set by the American Petroleum Institute (API). These standards provide guidelines not only for design and material but also for performance expectations under specified conditions. Adherence to these standards is non-negotiable in industries where safety and reliability are directly linked to environmental and operational outcomes.
In summary, tubing crossovers, while often overlooked, play a critical role in wellbore operations. An understanding of their technical underpinnings—rooted in precise engineering, material science, meticulous installation, and stringent quality control—ensures their effective application. By prioritizing expertise and reliability, this small but mighty component aids in optimizing oil and gas recovery in challenging environments. Their proper selection and deployment underscore the broader industry's commitment to efficiency, safety, and operational excellence.