In the oil and gas industry, professionals often encounter the terms casing and tubing, which are integral components of well design and operation. Understanding the differences between these two types of pipes can significantly impact the efficiency, safety, and success of drilling and production processes. This article offers a comprehensive exploration, focusing on experience, expertise, authoritativeness, and trustworthiness to provide a detailed explanation.
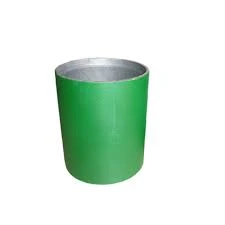
Casing is a large diameter pipe that is assembled and inserted into a freshly drilled section of a borehole to protect and support the wellstream. From a structural standpoint, its primary function is to stabilize the wellbore walls and prevent them from caving in. When a well is drilled, it passes through various layers of rock, some of which may contain unstable formations. Without casing, these unstable formations could collapse into the well, leading to costly and dangerous situations.
Moreover, casing isolates different subsurface zones, preventing the unwanted flow of fluids between sections. This isolation is crucial in maintaining control over reservoir zones and ensuring that fluids — such as oil, gas, or water — are conducted to the surface in a controlled manner. In terms of safety, casing serves as a protective barrier against potential blowouts, as it can withstand high pressure from formations and prevent the escape of hydrocarbons to the surface uncontrolled.
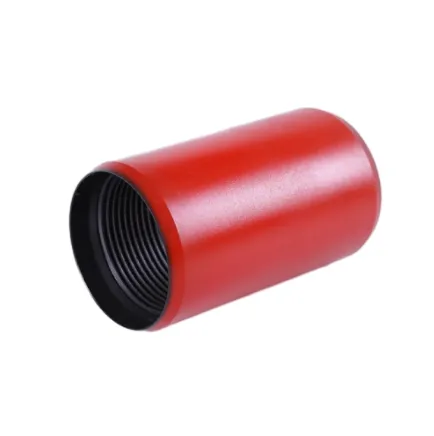
On the other hand, tubing is a much smaller pipe than casing and is installed inside the casing string. Its primary role is to conduct hydrocarbons from the production zone to the surface. While casing is designed for structural integrity and isolation, tubing focuses on facilitating the efficient and safe transport of production fluids. Tubing must be durable enough to resist corrosion from the often harsh and corrosive fluids it transports, while also being flexible to accommodate the thermal expansion and contraction it might experience during flowing conditions.
From an engineering perspective,
the design and material selection for both casing and tubing are pivotal. Casing typically requires robust materials and designs to withstand environmental and situational stressors. It must hold high tensile, burst, and collapse pressures. Tubing, while also needing to withstand substantial pressures, emphasizes corrosion resistance and tensile strength to ensure seamless fluid transport.
what are the differences between casing and tubing?
The installation process for casing and tubing further differentiates these two systems. Casing installation involves cementing, where cement is pumped into the space between the exterior of the casing and the wellbore wall, enhancing stability and forming a strong, isolated barrier. Tubing installation doesn't usually require cementing. Instead, it involves securing the tubing string inside the casing with a variety of downhole tools and packers to ensure any potential areas of leakage are sealed, thus optimizing production efficiency and safety.
Professionals selecting casing and tubing must consider various factors, including well depth, reservoir pressure, production fluid characteristics, and overall production strategy. These considerations directly influence the materials and specifications needed to ensure longevity and reliability.
Ultimately, successful well operation depends significantly on understanding and applying the correct specifications for both casing and tubing. Expertise in this domain enables industry professionals to design wells that maximize productivity while minimizing risks and costs. Given their complementary roles, utilizing the right combination of casing and tubing ensures that wells not only perform efficiently but also safely, safeguarding both crews and the environment.
In conclusion, understanding the nuanced distinctions between casing and tubing enhances decision-making and operational success in the oil and gas sectors. As technologies and materials continue to evolve, maintaining a strong grasp of these fundamental components' roles and requirements will remain essential for industry professionals striving to optimize well performance and sustainability.