Stainless steel couplings have long been hailed as a cornerstone in the realm of industrial applications due to their exceptional properties and versatility. Distinguished by their robust durability and resistance to corrosion, these components play a pivotal role in various mechanical systems. But beyond their functional importance, choosing the right stainless steel coupling can significantly enhance operational efficiency and safety in diverse sectors.
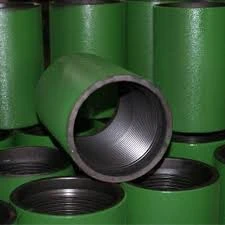
Industries ranging from automotive to aerospace rely heavily on stainless steel couplings for their seamless integration and performance under pressure. In high-pressure environments, a quality coupling ensures the secure transfer of energy without leakage or damage. This capability is crucial in maintaining the integrity of pipelines and machinery, preventing costly downtimes and repairs.
Stainless steel, renowned for its resilience, offers unmatched resistance to both chemical reactions and extreme temperatures, making it ideal for industrial use. Unlike other materials, stainless steel does not degrade quickly when exposed to harsh conditions, ensuring longevity and reduced maintenance costs. Couplings made from this material are particularly valuable in chemical processing plants where exposure to corrosive substances is a constant concern.
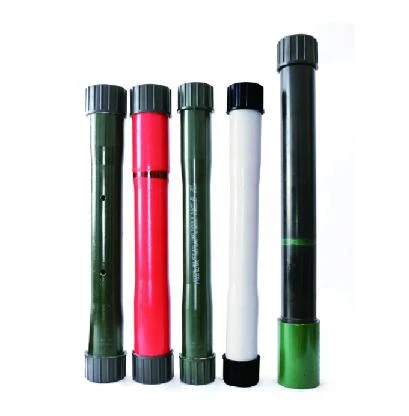
From a technical perspective, stainless steel couplings are engineered to accommodate various forms of mechanical loading. Their design allows for flexibility in alignment, effectively compensating for shifts and movements within mechanical systems. This adaptability reduces stress on connected components, prolonging their service life and maintaining optimal performance.
Expertise in the selection and application of stainless steel couplings is crucial. Engineers and purchasing managers need to consider factors such as the type of stainless steel alloy, size requirements, and environmental conditions.
Different grades of stainless steel, like 304 and 316, offer varied levels of resistance and mechanical properties. For instance, 316 stainless steel, with its added molybdenum, is superior in resisting chloride corrosion, making it preferable in marine or saline environments.
stainless steel coupling
Furthermore, the manufacturing process of stainless steel couplings adheres to stringent quality standards, ensuring their reliability across applications. Manufacturers leverage precision forging and CNC machining to achieve precise dimensions and tight tolerances. This precision ensures that each coupling meets the technical specifications required for its intended application, thereby enhancing reliability and safety.
Logistically, the deployment of stainless steel couplings across an operation can streamline processes. Their uniformity and compatibility with a variety of systems allow for easy interchangeability and scalability. This versatility ensures that businesses can adapt quickly to changes in demand or operational scale without significant overhauls to their existing setups.
The expertise of suppliers and manufacturers also plays a crucial role in guiding industries towards the optimal usage of stainless steel couplings. By providing tailored recommendations and customized solutions, reputable suppliers can significantly impact the efficiency of a company's mechanical operations.
In conclusion, stainless steel couplings are indispensable for industries demanding high performance, durability, and reliability. Their exceptional qualities not only improve the lifespan and safety of mechanical systems but also offer economic advantages through reduced maintenance needs and operational disruptions. With expert knowledge and careful selection, businesses can harness the full potential of stainless steel couplings to achieve superior operational results.