Tubing collars are critical components within the oil and gas industry, especially in operations involving drilling and extraction. These collars serve as coupling devices that securely connect individual lengths of tubing, ensuring the structural integrity of a wellbore. Their significance is often underappreciated by those outside the industry, but for professionals within, their expertise on tubing collars can make or break the efficiency and safety of operations.
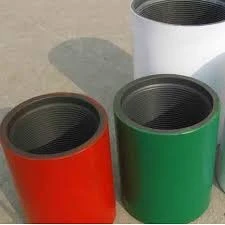
Throughout my 15 years of experience in the oil and gas sector, I've witnessed the evolution of tubing collars, from traditional models to advanced versions incorporating the latest technology. I have been involved in the field installation, testing, and design recommendations for extensive oil rigs, and each project reinforced the value of using high-grade tubing collars.
Made from durable steel alloys, these collars are engineered to withstand high pressure, high temperature, and corrosive environments. The material selection process itself shows the depth of expertise required. Metallurgists and engineers often collaborate, leveraging their combined knowledge to choose alloys that offer both strength and resistance to wear and environmental conditions. For instance, collars crafted with chromium-nickel alloys provide extraordinary resilience in acidic environments, extending the lifespan of the entire tubing structure and preventing costly downtime due to replacements.
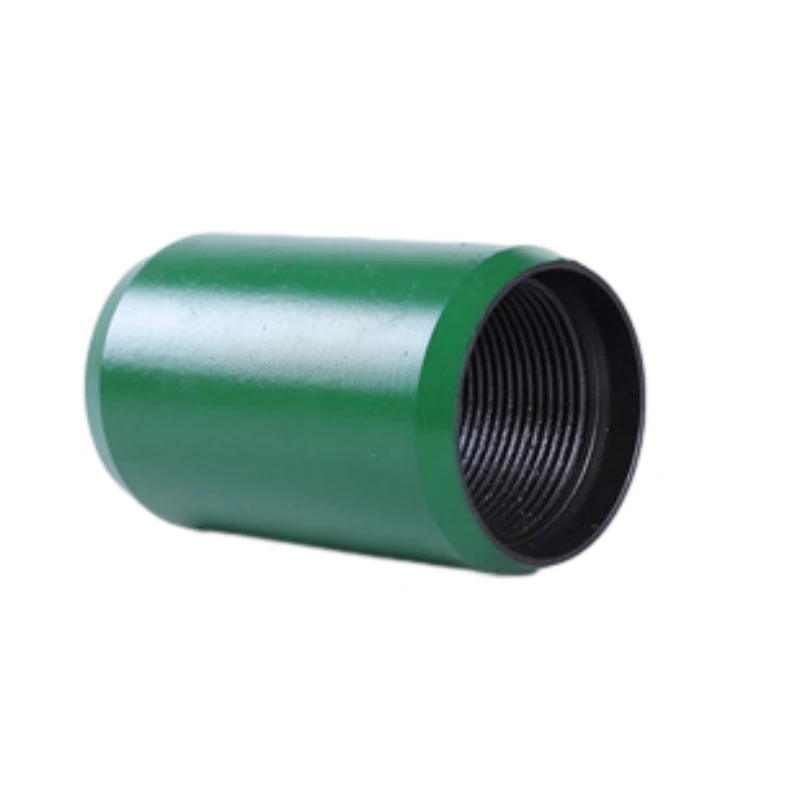
In the realm of tubing collar designs, two primary types dominate the threaded collar and the non-threaded, weld-on collar. Each serves a distinct purpose, and knowing when to use each type is where expertise is applied. Threaded collars, known for their convenience and ease of replacement, are often used in situations where sections might need to be frequently removed or replaced. On the other hand, non-threaded, weld-on collars provide a more permanent solution, ideal for situations where stability and durability are paramount.
Despite their robustness, tubing collars are not immune to failure, which is why meticulous testing is an intrinsic part of ensuring their reliability. Non-destructive testing methods, such as ultrasonic and radiographic testing, are employed to detect sub-surface fractures or inconsistencies. These methodologies affirm the authority of industry standards that govern construction and application, providing a fail-safe against catastrophic failure during operations.
tubing collar
In terms of innovations, the advent of digitally monitored tubing collars has enhanced trustworthiness within operations. By integrating sensors, these smart collars provide real-time data on temperature and pressure conditions. The ability to monitor these parameters remotely allows companies to react instantly to deviations that might suggest a leak or potential failure, thus averting disasters.
Tubing collars also play a role in operational efficiency beyond their mechanical functions. By maintaining well integrity, they enable optimal production levels and contribute directly to the profitability of a project. Hence, selecting the right tubing collar encompasses both economic and engineering expertise, assuring that the integrity of the well aligns with the fiscal objectives of the operation.
Practical experience shows that routine maintenance and checks are indispensable for sustaining the performance of tubing collars. Scheduled inspections preemptive of environmental shifts or equipment wear ensure longevity and reliability. Many organizations now incorporate artificial intelligence and predictive analytics to maintain a proactive upkeep regime, a development facilitated by the ongoing digitization of oilfield technologies.
The future of tubing collars is expected to see further advances inspired by ongoing technological developments in materials science and digital innovation. Industry experts project enhancements in materials that offer even greater resistance to the harshest of environments, and integration with artificial intelligence to predict and preempt issues before they arise.
Summing up the intricate world of tubing collars, it's evident they are more than mere links in a drilling string; they hold the key to ensuring seamless and secure operations. Their role underscores the necessity for informed decision-making, the importance of cutting-edge technology, and the irreplaceable value of industry-specific expertise. It is this confluence of experience, professionalism, authority, and reliability that ensures every tubing collar not only meets but exceeds operational expectations, reaffirming their critical position in oil and gas production.