In the world of oil and gas drilling, understanding the components of well construction is essential to ensure proper functionality, efficiency, and safety. Among these components, the pup joint plays a crucial role. A pup joint, essentially a length of tubing or casing, is specifically designed to adjust the length of the string to its desired specification. With varying applications across industries, the pup joint's significance is multifaceted.
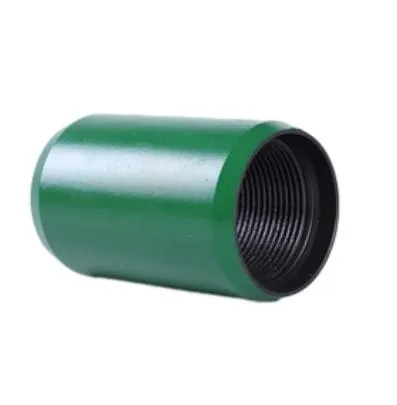
The primary function of a pup joint is to provide flexibility and precision in the drilling string assembly. In operations where precise depth measurements are crucial, pup joints ensure that the drilling operation remains on target. Fabricated from high-quality materials, they are tailored to withstand the high pressures and stresses encountered in subsurface environments, safeguarding against potential failures that can lead to costly downtime or damage.
Expertise in the oil and gas industry highlights the value of pup joints in enabling a tailored fit for assemblies. They come in varying lengths, usually between 2 and 12 feet, allowing for swift adjustments and ensuring that the overall string matches the specific length requirements of the project. This ability to make precise adjustments is invaluable for operators aiming to optimize their configurations quickly and efficiently.
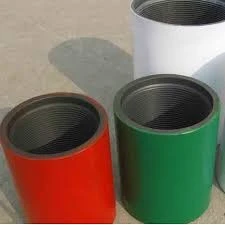
The authoritative value of pup joints is underscored by industry standards and manufacturing processes that ensure durability and compliance with safety regulations. Manufactured to meet the stringent standards of organizations such as the American Petroleum Institute (API), pup joints are a testament to engineering excellence. These regulatory frameworks ensure that every pup joint withstands operational stresses and performs reliably under challenging conditions.
what is a pup joint
Trusting a reliable supplier for pup joints is critical. Industry leaders provide not only the product but also technical support and consultation to ensure correct application and maximum operational efficiency. Making informed choices about the type of material, be it carbon steel, stainless steel, or a corrosion-resistant alloy, is pivotal. Each material offers specific advantages depending on the operational environment, whether it be standard, high-pressure, or corrosive.
Considering practical aspects of handling and maintenance enhances the experience with pup joints. Regular inspection routines, including checking for signs of wear and ensuring all threads are in excellent condition, contribute to prolonged service life. Storage procedures are equally important; ensuring joints are kept clean, dry, and free of contaminants will minimize the risk of damage when not in use.
For drilling operators seeking continuous improvements, advancements in pup joint technology provide opportunities to enhance efficiency. Innovations such as precision threading and anti-corrosion coatings extend the life of these components and reduce the likelihood of operational hindrances. These developments demonstrate a commitment to enhancing the practical application and reliability of pup joints, reinforcing their indispensable role in drilling operations.
In conclusion, the pup joint is a fundamental yet sophisticated component essential for the success of drilling operations in the oil and gas sector. A blend of engineered precision, robust construction, and adherence to industry standards ensures its reliability and efficiency in field applications. By promoting a deep understanding and careful management of this component, industry professionals can achieve remarkable operational results, boosting both productivity and safety. Thus, investing in high-quality pup joints from reputable suppliers not only supports immediate operational goals but also integrates into long-term strategic planning in the field development lifecycle.