In the dynamic realm of oil and gas exploration, precise and reliable casing coupling dimensions are paramount for operational efficiency and safety. Casing couplings play a critical role in connecting casing pipes, ensuring the structural integrity and pressure boundaries in drilling operations. Herein lies an exploration of their dimensions, tailored for those seeking expertise and trustworthiness in this essential aspect of the petroleum industry.
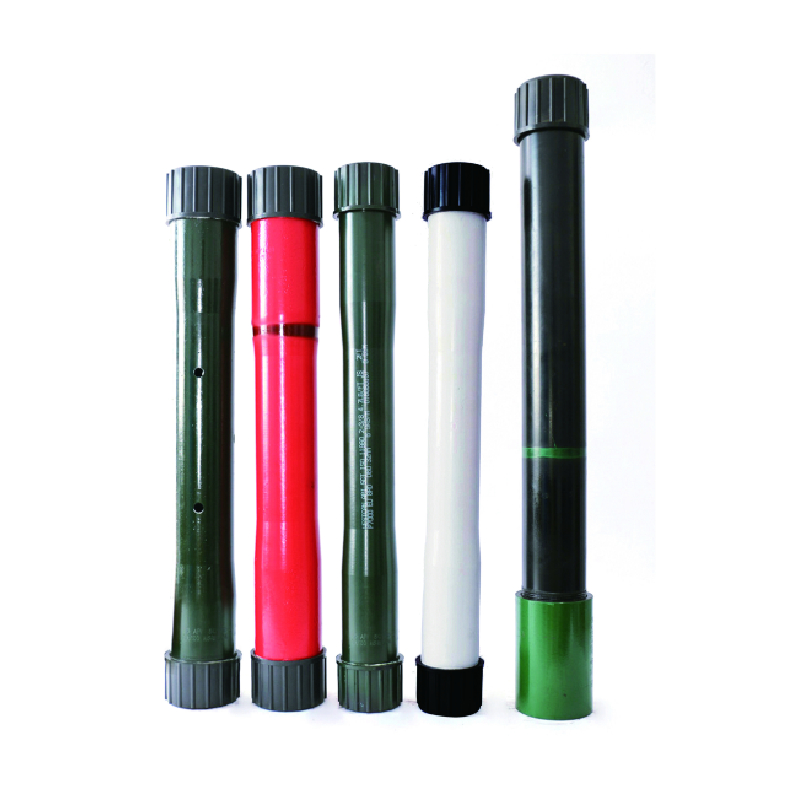
Understanding the intricacies of casing coupling dimensions begins with delving into the API (American Petroleum Institute) standards. The API 5CT specification is pivotal as it delineates the requirements for casing and tubing couplings. Recognizing the importance of these standards ensures that products not only meet industry expectations but also perform robustly under the demanding conditions of oil wells.
Dimensions of casing couplings are specified by various factors including outer diameter (OD), inner diameter (ID), length, grade, and connection type. These elements must be precisely measured and adhered to in order to maintain functionality and safety. Typically, casing couplings conform to standardized sizes such as those defined under API 5B, encompassing diameters from 1.05 to 20 or above, depending on the well design and operational requirements.
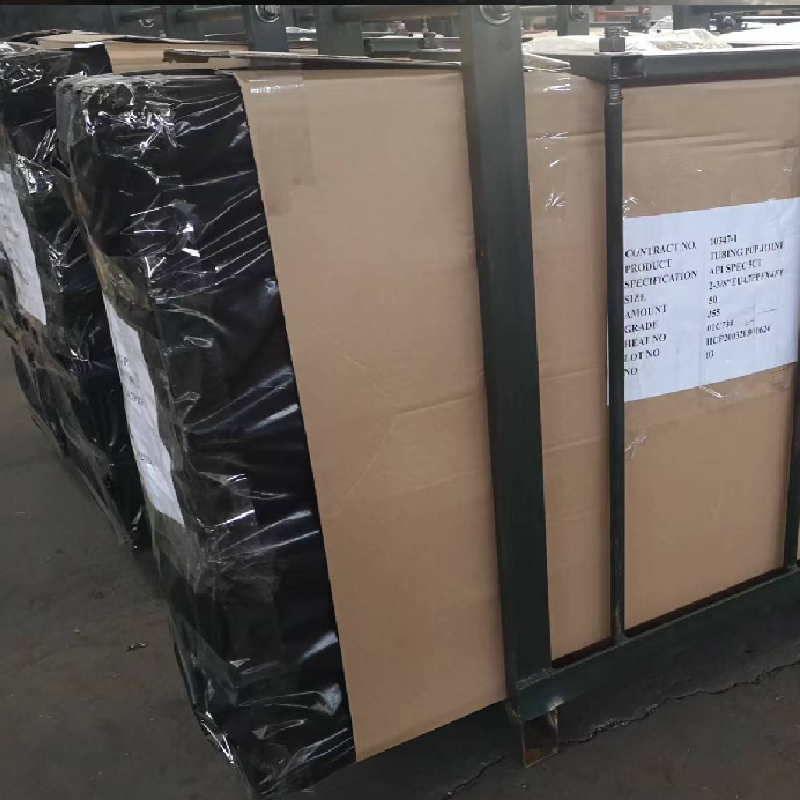
One common challenge encountered in this field is the selection of an appropriate coupling size to match the casing pipes. It is imperative to ensure that the inner diameter of the coupling accommodates the outer diameter of the casing pipe, while also considering thread type and specifications. For instance, buttress thread (BTC) and long thread (LTC) coupling types require different dimensional considerations; mismatches can lead to catastrophic operational failures.
Real-world application frequently brings to light the necessity of tailoring casing couplings to specific well conditions. Engineers and field experts often customize these components to withstand unique pressures, temperatures, and chemical exposures encountered within individual wells. Material selection, thus, becomes a critical consideration; options range from carbon steel to high alloy materials, each offering distinct advantages depending on environmental demands.
casing coupling dimensions
One illustrative case involved a deepwater drilling project where standard material couplings failed due to unexpected corrosive conditions. By analyzing the specific chemicals present and consulting with metallurgical experts, the team redesigned the couplings with a nickel-chromium alloy, resulting in enhanced durability and a reduction in maintenance frequency. This expert adaptation underscores the importance of not only following standards but also exercising engineering judgment and field-specific expertise.
In assessing the casing coupling market, seeking partnerships with manufacturers who are transparent about their adherence to API standards can greatly enhance the operational success rate. Additionally, reputable manufacturers often offer additional testing services, such as non-destructive examinations (NDE) and pressure testing, to verify the integrity of the coupling dimensions and performance before deployment.
Trustworthiness in this domain is further amplified through comprehensive quality control protocols and industry certifications. Manufacturers who consistently undergo external audits and adhere to ISO 9001 standards or equivalent quality management systems demonstrate a heightened level of commitment to reliability and excellence.
To maintain an authoritative position in the discussion of casing coupling dimensions, continual education and professional development are vital. Engaging with professional societies such as the Society of Petroleum Engineers (SPE) can provide updates on the latest research, technological advancements, and innovative practices that can shape future casing coupling designs.
In conclusion, casing coupling dimensions are an integral factor in the oil and gas sector, demanding careful attention to detail, adherence to standards, and situational expertise. By prioritizing these elements, professionals in the industry can ensure the safe and efficient operation of their drilling activities, safeguarding both their investments and the environment.