Bull plug pressure rating is an often overlooked yet crucial aspect in industries utilizing high-pressure systems. Understanding its intricacies can significantly enhance system safety and operational efficiency.
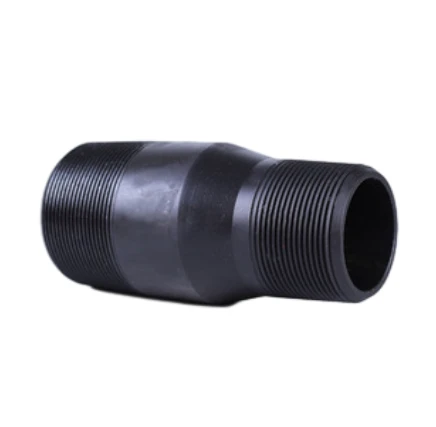
Bull plugs, essential components used to seal the end of a pipe or tubing, bear the brunt of system pressure, making their pressure ratings a critical performance parameter. Incorrect pressure ratings not only compromise safety but can also lead to fatal system failures, emphasizing the need for accurate knowledge and expertise in selecting the right bull plug for each application.
Experience in managing high-pressure scenarios reveals that choosing a bull plug with an adequate pressure rating involves more than just identifying a maximum pressure threshold. The operational environment, including temperature fluctuations, fluid type, and potential corrosive conditions, demands an experienced eye. For instance, when dealing with chemically aggressive environments, selecting a bull plug with corrosion-resistant properties alongside a robust pressure rating becomes imperative. Real-world experience consistently shows that overlooking these factors leads to premature wear or catastrophic failures, thereby necessitating costly repairs and downtime.
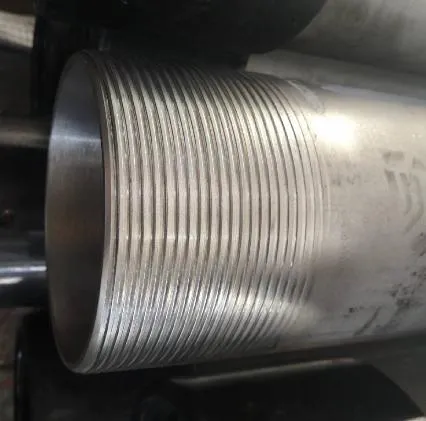
Expertise in material science further aids in understanding the pressure rating of bull plugs. Different materials, such as stainless steel or alloy, offer varying pressure endurance and resilience to environmental exposure. For example, stainless steel bull plugs may provide superior resistance against rust and corrosion, crucial in offshore drilling applications. By leveraging expertise in choosing the correct material, one can ensure that the bull plug not only withstands the required pressure but also delivers extended service life with minimal maintenance.
bull plug pressure rating
Authoritativeness comes into play as regulations and standards govern the manufacturing and application of bull plugs in high-pressure systems. Industry standards such as the American Petroleum Institute (API) specifications and the ASME Boiler and Pressure Vessel Code serve as benchmarks for pressure ratings and safety. Familiarity with these authoritative guidelines ensures compliance and imbues confidence that the selected bull plug meets the rigorous demands of modern industrial applications.
Trustworthiness in the selection process is underscored by sourcing bull plugs from reputable manufacturers, ensuring adherence to quality control measures and rigorous testing protocols. A trustworthy vendor provides detailed pressure rating certifications and testing documentation, offering peace of mind that each component has undergone stringent checks. This reliability is paramount in sectors such as oil and gas, where equipment failure can have substantial environmental and financial repercussions.
A hypothetical case study underscores the merit of comprehensively understanding bull plug pressure ratings. Consider a natural gas facility operating at 15,000 psi pressure environments; the engineering team opts for bull plugs rated marginally above their operational pressure. However, with expert insight, the team identifies recurring temperature spikes due to seasonal changes, necessitating a review and subsequently opting for plugs with a higher pressure rating and temperature tolerance. This adjustment not only averted potential system failures but also streamlined operations and enhanced safety protocols.
In conclusion, a detailed understanding of bull plug pressure ratings necessitates a harmony of experience, expertise, authority, and trustworthiness. By combining these elements, industries can optimize their high-pressure systems, ensuring resilience, safety, and longevity without compromising on effectiveness or exposing themselves to unwarranted risks.