Casing threads and couplings play a critical role in the oil and gas industry, providing structural integrity and leak-proof connections essential for the efficient and safe transport of fluids. Understanding the nuances of casing threads and couplings can significantly impact operational efficiency and safety.
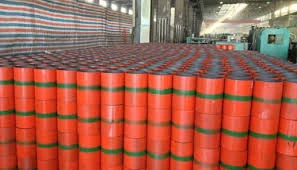
Historically, the development of casing threads has seen significant advancement. Gone are the days when simple threaded connections sufficed. Modern casing threads have evolved into sophisticated designs engineered for extreme environments and high-pressure applications. One of the most critical aspects of these threads is their ability to maintain a seal under fluctuating temperatures and pressures. An expertly crafted casing thread will reduce the risk of leaks and ensure the longevity of the piping system.
The most commonly used casing threads include API round thread, API buttress thread, and premium thread connections.
Each has its unique features and applications. API round threads, recognized for their versatility and ease of assembly, are typically used in low-pressure environments. On the other hand, API buttress threads offer a greater tensile strength suitable for deeper wells where higher pressures are prevalent. Premium threads have an increased focus on gas tightness, using advanced thread geometries to ensure durability and reliable sealing capacity. The selection between these is not arbitrary; it requires an in-depth understanding of the well environment and the specific operational demands.
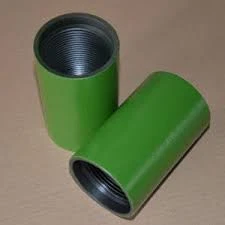
Couplings are equally essential in the context of casing systems, as they connect individual pipe segments, creating a continuous pipeline. The integration of couplings is vital for maintaining the alignment and sealing integrity of the pipeline. Modern couplings are crafted to resist corrosion, temperature variations, and mechanical stress. Choices for couplings range from standard seamless couplings to specialized types with anti-galling properties or built-in protectors.
Experience shows that the choice of materials for threads and couplings can significantly influence performance outcomes. The industry’s shift toward high-grade alloy steel and the incorporation of protective coatings have been game-changers, extending the lifespan of these components. These materials demonstrate superior resistance to the adverse effects common in demanding operational environments, like corrosion induced by harsh chemical exposure or mechanical fatigue from constant vibration.
casing threads and couplings
The expertise involved in the installation and maintenance of casing threads and couplings cannot be understated. Employing skilled professionals who understand the intricacies of thread geometry and coupling dynamics ensures the reliability of the entire system. Proper training and adherence to installation guidelines are critical in preventing mishaps that could lead to costly well interventions or environmental damage.
Furthermore, the importance of choosing a reputable manufacturer cannot be overstressed. Authoritative manufacturers provide quality assurance processes that include stringent testing for both threads and couplings. This ensures that each product not only meets but exceeds industry standards. Reliable manufacturers also offer certification and documentation providing traceability and assurance of the product's performance characteristics.
Trustworthiness is established through consistent performance and demonstrable safety records. In this context, the integration of casing threads and couplings with advanced diagnostic technologies for integrity monitoring can preempt failures. Periodic inspections and the use of technologies such as ultrasound or electromagnetic scanning aid in early detection of wear and tear, preventing catastrophic failures.
In conclusion, the strategic selection and maintenance of casing threads and couplings is paramount for the efficiency and safety of well operations. An in-depth understanding of the technical specifications, combined with cutting-edge materials and expert installation, forms the foundation of a reliable casing system. Trustworthy manufacturers and comprehensive monitoring systems further enhance operational security, ensuring that the complexities of the oil and gas industry are met with precision and reliability.