The significance of Casing Coupling in Oil and Gas Industry
In the dynamic landscape of the oil and gas industry, casing coupling plays an integral role in ensuring the safety and efficiency of drilling operations. This critical component is the backbone of the well construction process, connecting individual sections of steel casing to form a continuous barrier that protects the wellbore and supports the drilling process.
Casing, essentially, is a large-diameter pipe that is lowered into a well to provide structural integrity and prevent the collapse of the wellbore walls. Coupling, on the other hand, is the juncture that unites these casings, forming a seamless connection. The coupling mechanism ensures a strong, leak-proof seal, thereby preventing the ingress of fluids and maintaining well control.
The design of casing couplings varies depending on the specific application and the conditions encountered downhole. They can be thread-type or non-threaded, with each type offering its own advantages. Threaded couplings, for instance, allow for easy assembly and disassembly, while welding or swaging methods provide a more permanent connection.
The quality and durability of casing couplings are paramount. High-stress environments, extreme temperatures, and exposure to corrosive substances demand robust materials and precision engineering. Any failure in the coupling can lead to catastrophic consequences, including blowouts, environmental contamination, and loss of equipment.
Moreover, casing coupling is not just about physical joining; it also involves sophisticated calculations and engineering considerations
Moreover, casing coupling is not just about physical joining; it also involves sophisticated calculations and engineering considerations
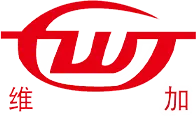
Moreover, casing coupling is not just about physical joining; it also involves sophisticated calculations and engineering considerations
Moreover, casing coupling is not just about physical joining; it also involves sophisticated calculations and engineering considerations
casing coupling. Factors such as tensile strength, torque capacity, and pressure ratings must be meticulously assessed to ensure the coupling can withstand the anticipated loads and pressures during drilling and production phases.
The coupling process itself is a meticulous operation, often requiring specialized tools and skilled technicians. Regular inspection and maintenance are necessary to ensure the integrity of the connections, further emphasizing the importance of proper casing coupling.
In recent years, advancements in technology have led to the development of more efficient and safer casing coupling systems. For instance, new materials like corrosion-resistant alloys and advanced coating technologies have improved the lifespan and performance of couplings. Additionally, digital solutions, such as real-time monitoring systems, have enhanced our ability to predict and prevent potential issues.
In conclusion, casing coupling is a vital aspect of the oil and gas industry, playing a crucial part in the complex dance of drilling and production. It is a testament to human ingenuity and the constant quest for safety and efficiency in an industry that pushes the boundaries of engineering. As we continue to explore deeper and more challenging reservoirs, the importance of effective casing coupling will only grow, underlining its indispensable role in the global energy sector.