Pup joint pipes are integral components used extensively in the oil and gas industry, serving as a crucial element in drilling, production, well testing, and well intervention operations. Their primary utility lies in adjusting the length of the drill string, which makes them indispensable for operations requiring high precision and customization. Pup joints come in various lengths and sizes, which offers unmatched flexibility in the rig setup process. Below, we'll delve deeper into what makes pup joint pipes paramount in oil and gas exploration and production.

Pup joint pipes are designed to withstand the rigorous demands of the oilfield environment. They are manufactured using high-quality steel that possesses exceptional tensile strength, which ensures durability in harsh conditions. The steel used is typically either AISI 4140 or AISI 4130, selected for their excellent mechanical properties and resistance to the corrosive effects of drilling fluids. These materials undergo a heat treatment process that further enhances the metal’s resilience, ensuring it can endure high pressures and temperatures typically found in deep drilling operations.
The precision involved in producing pup joint pipes is paramount. Each pipe undergoes meticulous threading processes, where connections are crafted to meet the American Petroleum Institute (API) standards. These threads are critical as they ensure a leak-proof connection between the various components of the drill string, helping to maintain the integrity of the wellbore under fluctuating pressure conditions. The threads are often coated and protected using industry-standard sealants that prevent galling, a common issue in thread connections that can lead to costly downtimes.
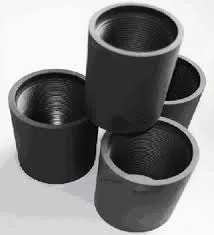
In terms of dimensions, pup joint pipes come in various lengths, usually ranging from 2 feet to 12 feet. This variance allows for precise adjustments to the drill string length without needing additional lengthy pipes, streamlining operations significantly. Since well conditions can vary vastly, having the ability to incrementally adjust the length of the equipment reduces time and costs associated with preparing and maintaining the rig. To complement their customizable nature, pup joints come with different bore sizes catering to specific flow requirements, which aids in optimizing the flow dynamics of the drilling or production operation.
One of the defining features of pup joint pipes is their robustness in extreme environments. Elevated temperatures and pressures significantly challenge materials and connections in deep well drilling. Pup joints, being crafted from specially treated steel alloys, offer enhanced resistance to such conditions, minimizing the risk of failures. Their ability to maintain performance integrity under duress is vital, especially when considering the high costs and potential hazards associated with equipment failure in such circumstances.
pup joint pipe
Furthermore, advancements in technology have introduced enhancements in pup joint pipe designs. Modern pup joints are often coated with specialized anti-corrosive and anti-fouling materials that further extend their operational life. This is crucial in subsea operations where exposure to seawater could shorten the lifespan of less protected equipment. By utilizing state-of-the-art coatings, operators can ensure longer service periods and reduced maintenance costs, contributing significantly to the overall efficiency of their operations.
The role of pup joint pipes in well intervention cannot be overstated. During workovers or maintenance routines, they allow for seamless access to well components that require adjustments or replacements. Their ease of use and installation facilitates rapid interventions, keeping the downtime to a minimum and ensuring that production is resumed swiftly. This aspect is of significant economic importance, as minimizing non-productive time directly correlates to enhanced operational profitability.
Lastly, the trustworthiness of pup joint pipes is underpinned by their compliance with international manufacturing standards and the rigorous testing they undergo. Manufacturers subject these pipes to exhaustive quality checks, including hydrostatic tests, non-destructive testing (NDT), and other industry-specific evaluations. The superiority of pup joints lies in meeting these stringent quality assurances, making them a reliable component in the high-stakes environment of oil and gas operations.
In summary, pup joint pipes are indispensable for their flexibility, durability, and reliability in the oil and gas industry. They facilitate the fine-tuning of drilling and production setups, withstand harsh operational environments, and contribute to the overall safety and efficacy of well operations. As oil and gas extraction methods continue to evolve, the role of high-quality, meticulously engineered components like pup joint pipes becomes even more critical, ensuring that operations are conducted safely, efficiently, and economically.