In the realm of mechanical engineering and industrial applications, the term special clearance coupling denotes a significant advancement in rotational equipment design.
Special clearance couplings, though specialized, have profound implications for industries relying on dynamic machinery systems. These couplings offer enhanced efficiency, reliability, and operational precision, making them a cornerstone in advanced mechanical solutions.
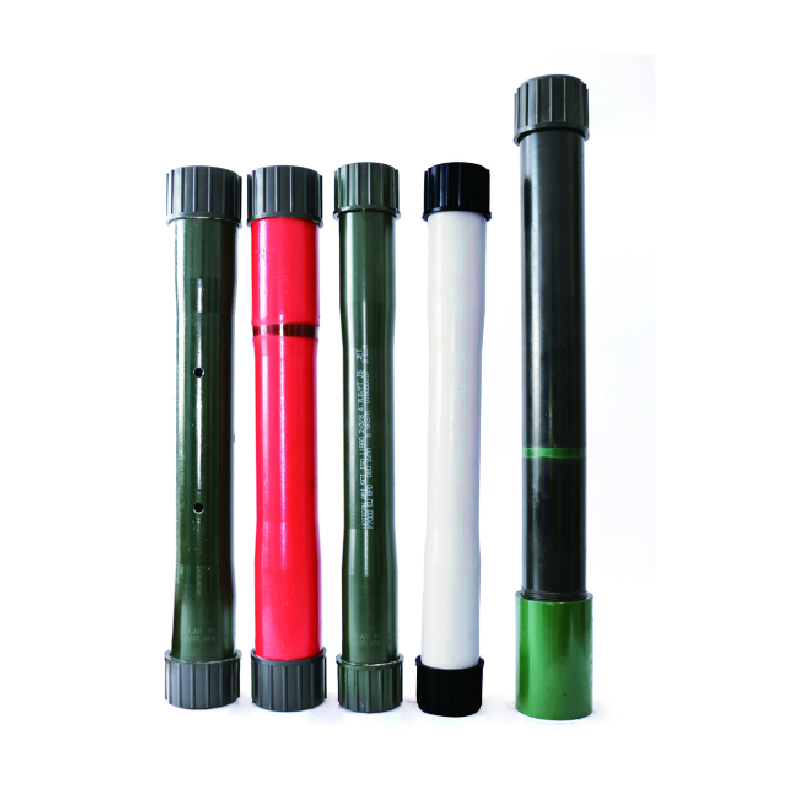
The concept of special clearance coupling is pivotal when optimizing machinery for high-performance applications. These couplings are engineered with deliberate clearances, tailored to accommodate specific operational conditions, thus ensuring maximum mechanical efficiency and minimal wear and tear. This customization is not arbitrary; it’s the result of meticulous analysis and understanding of the particular requirements of various machinery systems.
To appreciate the complexities and advantages of special clearance couplings, it is essential to delve into the expertise that shapes their design. Professionally, these couplings are crafted using state-of-the-art materials and manufacturing processes. High-grade alloys and composite materials are commonly employed to withstand extreme conditions, including high torque and misalignment. Precision engineering allows these couplings to handle these challenges without compromising performance.
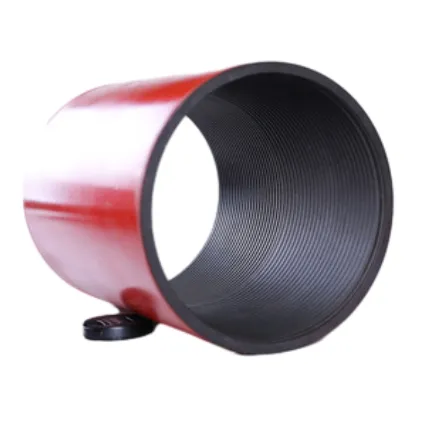
From an expertise perspective, the design and implementation of special clearance couplings are driven by detailed analytical modeling and simulation technologies. With the advent of advanced computing, engineers can simulate the exact conditions under which the coupling will operate, predicting potential points of failure and friction. The use of finite element analysis (FEA) and computational fluid dynamics (CFD) facilitates the identification of optimal clearance settings, ensuring the coupling's resilience and durability.
special clearance coupling
The authority behind special clearance couplings comes from their widespread adoption in critical sectors, where reliability is non-negotiable. Industries such as aerospace, automotive, and renewable energy heavily rely on these couplings to maintain operational continuity. In aerospace, for example, the delicate balance between weight and strength necessitates the use of custom clearances to manage the stress distribution across the coupling during flight. Similarly, in wind turbines, these couplings ensure the blades can rotate effectively in variable wind conditions without causing undue stress on the rotor system.
Trustworthiness in the application of special clearance couplings is reinforced by rigorous testing protocols. Before these couplings make their way into the field, they undergo comprehensive performance assessments. These tests, which include thermal cycling, load testing, and lifecycle analysis, ensure that each coupling meets stringent industry standards and safety regulations. The commitment to quality assurance underscores the dependability of these components in high-stakes environments.
Real-world experiences further validate the efficacy of special clearance couplings. Examples abound of companies witnessing significant improvements in machinery uptime and efficiency after adopting these specialized solutions. Maintenance teams report reduced downtimes and extended service intervals, attributing these improvements to the precision design of the couplings. These practical testimonials reaffirm the role of special clearance couplings as vital components in modern industrial setups.
In conclusion, special clearance couplings represent a synthesis of engineering prowess and practical application. Their development is borne out of a deep understanding of mechanical principles and an unwavering commitment to industrial advancement. By addressing specific operational challenges through tailored design, these couplings embody the pinnacle of mechanical reliability and performance. As industries continue to push the boundaries of technology and efficiency, the importance of such specialized components will only grow, solidifying their status as essential elements in the machinery landscape.