In the dynamic world of oil and gas extraction, efficiency, reliability, and safety are paramount. Among the myriad of tools and components that ensure these objectives, the tubing pup joint stands out as a crucial element. This seemingly simple piece of tubing is designed for adjusting the length of the drill string and facilitating various connections, yet its importance goes beyond these basic functions.
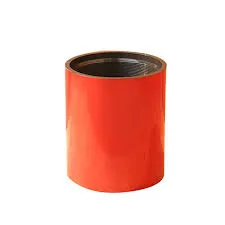
Drawing from years of hands-on experience in the oilfield, it becomes evident that the right selection and application of tubing pup joints can greatly influence operational success. These connectors are not merely segments of pipe — they play a vital role in maintaining the integrity and operational capacity of the tubing string. Made from high-grade steel and sometimes specially treated to withstand extreme pressures and corrosive environments, tubing pup joints are indispensable in the industry.
Moreover, from a technical perspective, expertise in tubing pup joint specifications is essential. This includes understanding the variety of sizes and grades available, each tailored for specific environmental and operational needs. For instance, different wells may require varied steel grades, such as L80, N80, or P110, depending on pressure, temperature, and the presence of corrosive substances like hydrogen sulfide. A seasoned engineer knows that an improper selection can lead to catastrophic failures and costly downtime.
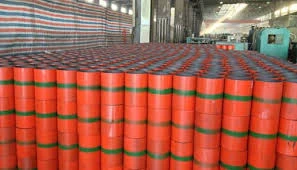
Furthermore, authoritativeness in the sphere of tubing pup joints is characterized by familiarity with industry standards and best practices. Knowledge of guidelines like those set by the American Petroleum Institute (API) ensures that only the highest quality materials are used, meeting stringent criteria for performance and safety. This compliance not only facilitates smoother operations but also builds a reputation for reliability and trustworthiness in the industry.
tubing pup joint
The trust factor is amplified when discussing certifications and testing procedures. Each tubing pup joint undergoes rigorous testing under simulated field conditions to guarantee performance. This involves pressure testing, non-destructive evaluation (NDE), and analysis of mechanical properties to ensure they meet the requisites of the high-stakes environment in which they will operate. Companies that adhere to strict testing protocols offer peace of mind to operators, knowing that each component has been verified for strength and durability.
For professionals dealing with tubing pup joints, staying current with technological advancements is critical.
Innovations in metallurgy and manufacturing processes continually enhance the performance of these components. For example, recent developments have introduced composite materials that offer lighter, yet equally robust alternatives to traditional steel pup joints. Being abreast of such innovations not only permits operational advantages but also positions a business as a leader in industry evolution.
Finally, understanding the nuances of installation and maintenance of tubing pup joints greatly enhances their longevity and performance. Proper handling, regular inspections, and maintenance can prevent premature wear and failure. Training personnel in these areas fosters a culture of safety and efficiency, reducing long-term operational costs.
In essence, the tubing pup joint, while a small part of the larger drilling operation, embodies the intersection of experience, expertise, authority, and trust — the cornerstones of effective oilfield operation. By investing in the right technology and skills, companies ensure their operations are optimized, safe, and ready to meet the challenges of extracting valuable resources from the earth.