A pup joint is an integral component widely used in the oil and gas industry, facilitating efficient and scalable operations in drilling and pipeline maintenance. Derived from its name, a pup joint is a short length of pipe, often measuring between a few feet to several tens of feet, specifically designed to adjust the length of a drill string or casing string. The utility of pup joints extends beyond mere length adjustment; they play a crucial role in enhancing operational precision and reducing wastage, thereby solidifying their indispensable nature in industry applications.
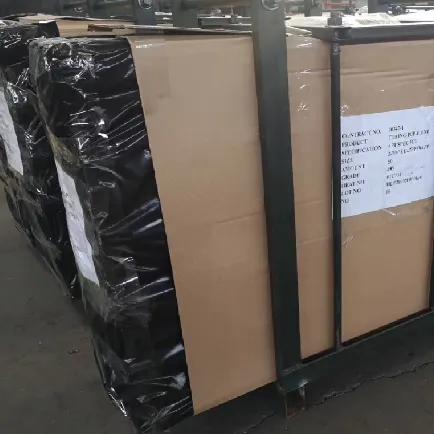
Pup joints are crafted from high-quality materials to ensure durability and resistance to extreme temperatures and pressures characteristic of subterranean environments. Steel, especially alloy steel, is predominantly used, attributing to its strength and resilience, which are critical under high-stress conditions encountered during drilling operations. The meticulous manufacturing process ensures these joints meet stringent industry standards, thereby guaranteeing their safety and performance.
One of the key attributes of pup joints is their versatility. They come in various grades, weights, and thread types to suit different operational needs. For instance, threaded and coupled (T&C) pup joints offer seamless integration within existing pipe systems, reducing the risk of leaks and ensuring a secure fit. This adaptability is crucial in an industry where precision and reliability can directly impact both the efficiency and safety of operations.
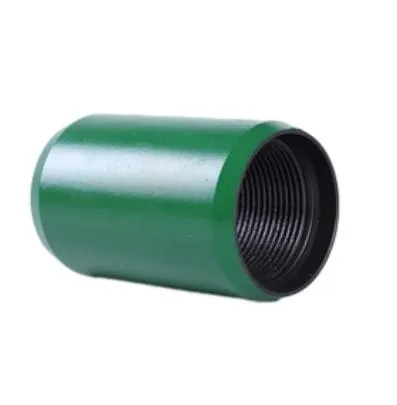
Real-world experience underscores the cost-effectiveness of utilizing pup joints. By facilitating precise customization of drill strings, pup joints minimize the need for cutting longer pipes, which can lead to material wastage and increased operational costs. Additionally, they enable operators to make on-the-fly adjustments to equipment setups, leading to significant savings in terms of both time and resources. This adaptability is particularly beneficial in offshore drilling environments, where logistical challenges amplify the importance of operational flexibility.
Expertly engineered pup joints also contribute to enhancing the safety of drilling operations. Their robust construction ensures they can withstand high tensile loads and torque, thereby minimizing the risk of equipment failure and the consequent downtime or accidents. By maintaining integrity under immense stress, pup joints safeguard personnel and equipment, embodying the industry's commitment to maintaining high safety standards.
what is a pup joint
In terms of authority, the production and use of pup joints are governed by internationally recognized standards such as those set by the American Petroleum Institute (API). These standards dictate the manufacturing specifications, including length, weight, grade, and thread type, ensuring that all pup joints deployed in the field adhere to rigorous quality and safety benchmarks. Companies investing in quality pup joints are likely to favor those compliant with API standards, underscoring the significance of regulatory compliance in maintaining operational fidelity.
The trustworthiness of pup joints is further reinforced through rigorous testing and quality assurance processes. Each joint undergoes extensive testing to simulate operational conditions, examining how they respond to tension, pressure, and temperature variations. This commitment to quality assurance enables companies to trust that their equipment will perform to expectations, enhancing the reliability of their operations.
In the rapidly evolving landscape of the oil and gas industry, the role of pup joints remains fundamental. They embody the industry’s shift towards more efficient, safer, and environmentally conscious practices. By reducing waste, enhancing operational flexibility, and ensuring safety, pup joints are not merely components of a drill string or casing string; they are emblematic of the industry's continuous pursuit of innovation and excellence.
In conclusion, pup joints are more than adjuncts to pipes; they are enablers of operational efficiency and safety. Their design and deployment are crucial for achieving nuanced operational goals, making them indispensable in modern drilling and pipeline maintenance activities. As new technologies and methodologies emerge, the humble yet highly sophisticated pup joint will undoubtedly continue to evolve, rising to meet the challenges and demands of contemporary and future energy exploration and production.