When considering various components and equipment used in the oil and gas industry, the bull plug stands out due to its functional relevance and widespread usage. Engineered for high-pressure environments, a bull plug is a type of pipe fitting used to terminate the end of a piping system or pressure vessel. Its primary function is to block off a section of pipe, providing both safety and efficiency in industrial applications.
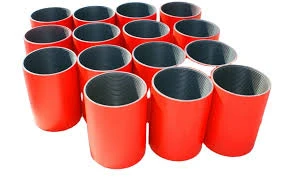
Bull plugs are typically solid fittings, rounded on one end, and threaded on the other, making them ideal for tasks where a secure seal is paramount. Precision in manufacturing ensures they withstand extreme pressures, reducing risks associated with leaks or bursts, which could lead to catastrophic equipment failure or environmental damage.
The experience of using bull plugs across different settings emphasizes their importance in sectors such as drilling, production, and chemical processing. Operators have reported significant operational efficiency when employing bull plugs in shutting down pipeline routes for maintenance or during pressure testing. Their ease of installation and removal allows for quick adaptation to changing operational needs without significant downtime.
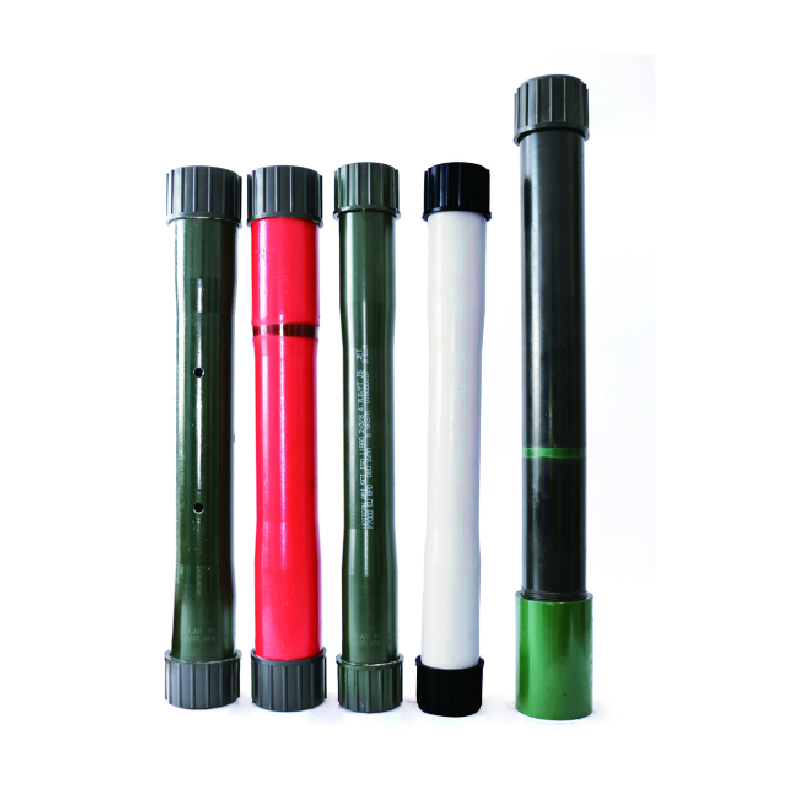
From an expertise standpoint,
the manufacturing of bull plugs demands advanced metallurgy and engineering principles. The materials used are typically carbon steel, stainless steel, or alloys designed to endure corrosive environments. For example, stainless steel bull plugs are often employed in offshore drilling, where saltwater corrosion might otherwise be detrimental. The selection of material impacts the plug’s longevity, and choice often depends on specific environmental conditions and pressure requirements.
Moreover, proper sizing and threading are critical for ensuring a tight fit, preventing any potential for leaks. The precision in these fittings exemplifies the careful engineering and manufacturing processes that prioritize both function and safety. The threading generally adheres to ANSI or API standards, ensuring compatibility and safety across systems worldwide.
what is bull plug
Bull plugs also play a critical role in the broader system integration within the industry. They frequently work in conjunction with other fittings such as flanges, elbows, and reducers, making them versatile components within the pipeline infrastructure. Their integration helps in managing flow paths, redirecting pressure, and isolating sections for maintenance without disrupting operations.
Trustworthiness of bull plugs is non-negotiable; hence, rigorous testing and quality control measures are integral to their production. Manufacturers often subject these plugs to pressure tests, material defect examinations, and dimensional measurements to ensure compliance with industry standards. Users must regularly inspect and maintain bull plugs as part of routine pipeline checks to detect early signs of wear or damage, ensuring continual operational integrity.
Apart from oil and gas, bull plugs find their utility in various industrial applications, including water treatment plants and chemical facilities. Their role in maintaining system safety by providing a reliable seal makes them indispensable across industries requiring precise pressure management and pipeline integrity.
To achieve an authoritative level of understanding regarding bull plugs, professionals must consider both theory and applied experience. Training programs and certifications for pipeline engineering often include detailed modules on fittings like bull plugs, emphasizing their critical function in system design and maintenance. Learning from seasoned engineers who have firsthand experience with these components can provide invaluable insights into best practices and problem-solving strategies when using bull plugs.
In conclusion, bull plugs are essential components in maintaining the integrity and safety of pipelines in various industries. Their importance cannot be overstated, given their role in preventing leaks, safeguarding against pressure-related accidents, and enabling efficient industrial operation. The combination of expert manufacturing, rigorous testing, and proper installation and maintenance practices solidifies their status as a reliable and necessary element in high-stakes industrial applications. Understanding their functionality and proper use not only enhances operational efficiency but also contributes significantly to overall safety and system endurance.