When delving into the intricate world of oil and gas well completion, the term seating nipple might seem technical, yet it plays a crucial role in well integrity and production efficiency. This specialized component, originating from the craftsmanship of seasoned engineers, serves as a vital element in the subsurface safety systems employed in wells.
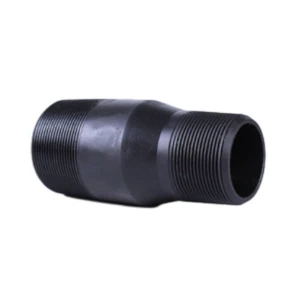
Seating nipples, often used in conjunction with other completion tools like plugs and checks, provide an ingenious solution designed to handle high-pressure environments. For professionals navigating the complex terrains of petroleum engineering, understanding the merits and functions of seating nipples is fundamental.
The key to the effectiveness of seating nipples lies in their robust design and material selection. Usually crafted from high-grade steel or corrosion-resistant alloys, these components are engineered to endure extreme downhole conditions. Their durability ensures long-lasting performance, preventing costly maintenance and interventions, which is a significant consideration in the challenging economic landscape of oil and gas operations.
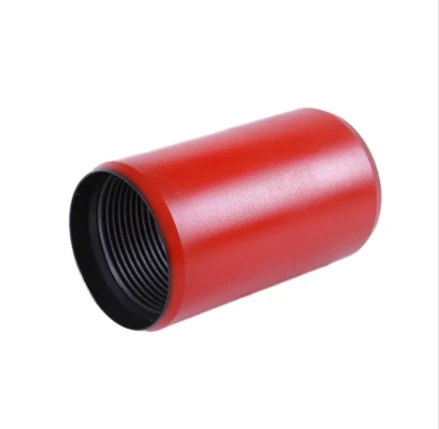
Functionality is another facet where seating nipples shine.
They are instrumental in controlling fluid flow within the tubing strings. Through their precise engineering specifications, seating nipples allow for the secure placement of various types of plugs. These plugs can be selectively inserted or removed, enabling operators to isolate sections of the well. This functionality is essential, especially when dealing with zonal isolation during production or when executing specific well interventions.
In terms of installation expertise, seating nipples demand meticulous attention. Experienced wellsite engineers emphasize the importance of correct seating nipple placement within the tubing string. The precise location ensures optimal accessibility and operational efficiency, which are critical for maintaining the integrity of the wellbore and enhancing production rates. Training and experience play a significant role here, as improper installation can lead to tools becoming stuck or operational failures.
seating nipple
Professionals well-acquainted with seating nipples appreciate the flexibility they bring to well operations. Whether it is for permanent installations or temporary interventions, seating nipples offer adaptable solutions to varied wellbore challenges. Their ability to accommodate different plug types — such as flow control devices, blank plugs, or chokes — underscores their versatility and indispensable nature in completion design.
The authoritative voice in well completion does not only stem from the technical robustness of seating nipples but also from the empirical data gathered from numerous successful installations worldwide. The trustworthiness of this component is established through case studies demonstrating their efficacy in enhancing well productivity while reducing operational risks.
Industry experts often highlight the advancements in seating nipple technologies, where the integration of smart sensors provides real-time data monitoring. This innovative approach marries traditional engineering principles with modern data analytics, offering operators insights into downhole conditions. Such information is invaluable, especially in predictive maintenance and optimizing production strategies.
The experience garnered from field applications underscores a vital lesson working closely with manufacturers to tailor seating nipples to specific operational needs is crucial. This collaboration ensures that the units meet the unique demands of each well environment, thereby maximizing their performance and extending operational lifetimes.
As operators seek to push the boundaries of efficiency and effectiveness, seating nipples remain prominent in discussions around well completion innovations. Their continued relevance and evolving functionality underscore their position as a cornerstone component in the ever-advancing domain of oil and gas extraction.