In the realm of oil and gas industry, the term bull plug isn't just a technical jargon; it holds paramount significance. This crucial component embodies the intersection of advanced engineering, practical adaptability, and critical safety measures.
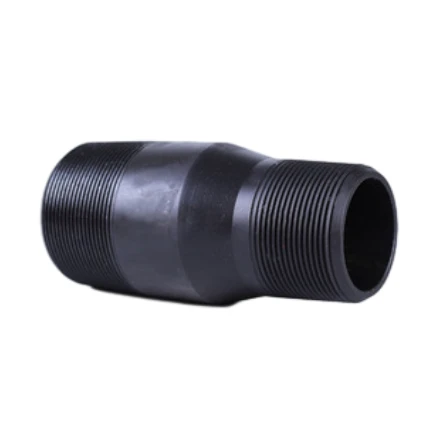
Bull plugs are essential components within a wellbore, primarily used to seal the end of the drill pipe or tubing. Their principal function is to provide a secure closure and prevent any fluid or gas from escaping. Choosing the right bull plug isn't merely about fitting protocols or dimensions; it involves understanding the pressures, temperatures, and the chemical profile of the substances they will encounter.
Crafted from high-grade steel or corrosion-resistant alloys, bull plugs must adhere to stringent safety and quality standards to withstand harsh subterranean environments. In my experience working on oil fields that stretch across challenging terrains, the effectiveness of a bull plug is often a balancing act of material science and engineering precision. Selecting a subpar plug can lead to catastrophic failures, risking safety, environmental damage, and significant financial losses.
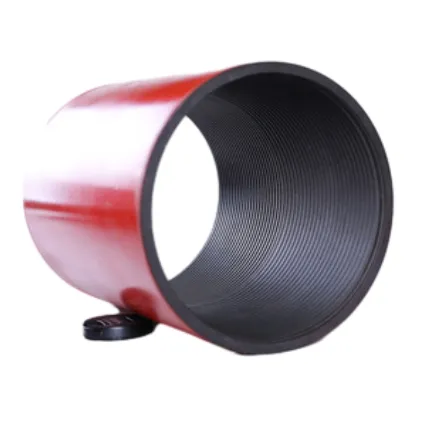
Understanding the different types of bull plugs available is critical. Threaded bull plugs are common, valued for their ease of installation and reliability. They are designed to be compatible with a wide array of casing and tubing threads, making them adaptable for various operational needs. If your operational environment entails high-pressure conditions, threaded bull plugs made from stainless steel are recommended due to their excellent pressure tolerance and corrosion resistance.
bull plug
On projects involving corrosive gases, such as hydrogen sulfide, opt for bull plugs manufactured from duplex stainless steel or those with special coating treatments. These provide an extra layer of protection, ensuring longevity and integrity of the seal. In scenarios where temporary sealing is required, plastic bull plugs present a viable option, offering flexibility and cost-effectiveness without compromising on performance.
Bull plugs' reliability is also enhanced by adhering to strict manufacturing standards. API 5CT and NACE MR0175/ISO 15156 are among the key standards that dictate the design, materials, and quality of bull plugs in oil and gas operations. Consult manufacturers who not only comply with these standards but also have certifications and a proven track record in delivering durable and dependable components. In my professional trajectory, selecting a manufacturer with robust quality assurance processes has been critical in ensuring the safety and efficiency of drilling operations.
Innovation continues to shape the development of bull plugs. Advances in materials technology and manufacturing processes have led to the introduction of bull plugs that promise even greater resilience and adaptability. From enhanced surface treatments to new alloy formulations, the future of bull plugs is one that promises improved performance in even the most demanding conditions.
In conclusion, the selection and use of bull plugs are more than a mere technical decision; they are a pivotal element in ensuring the safety, efficiency, and success of oil and gas undertakings. By leveraging comprehensive expertise and adhering to high standards, professionals in the industry can make informed decisions that reinforce the integrity of their operations. Emphasizing experience, expertise, and trustworthiness in your choice of bull plugs can prevent future disruptions and enhance overall operational efficacy.