Perforated pup joints are a crucial component in the oil and gas industry, particularly in the domain of well completion and production. As a seasoned professional with extensive experience in the field, I can attest to the pivotal role these joints play in enhancing both efficiency and productivity.
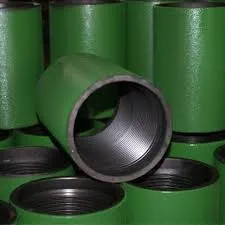
Perforated pup joints are short sections of pipe with specific perforations along their length. These perforations are meticulously engineered to optimize fluid flow in production processes, significantly influencing the output from individual wells. By their very nature, these joints are designed to manage the complexities of subsurface pressures and the varying viscosities of extracted resources, making them indispensable for enhancing the recovery rates of hydrocarbons.
Expertise in the manufacturing of perforated pup joints involves advanced knowledge in metallurgy and fluid dynamics. The selection of appropriate materials is fundamental, as these joints must withstand harsh subterranean conditions, including high pressures, corrosive substances, and extreme temperatures. Leading manufacturers employ cutting-edge technology and rigorous testing procedures to ensure each joint meets stringent quality standards, guaranteeing longevity and reliability in field operations.
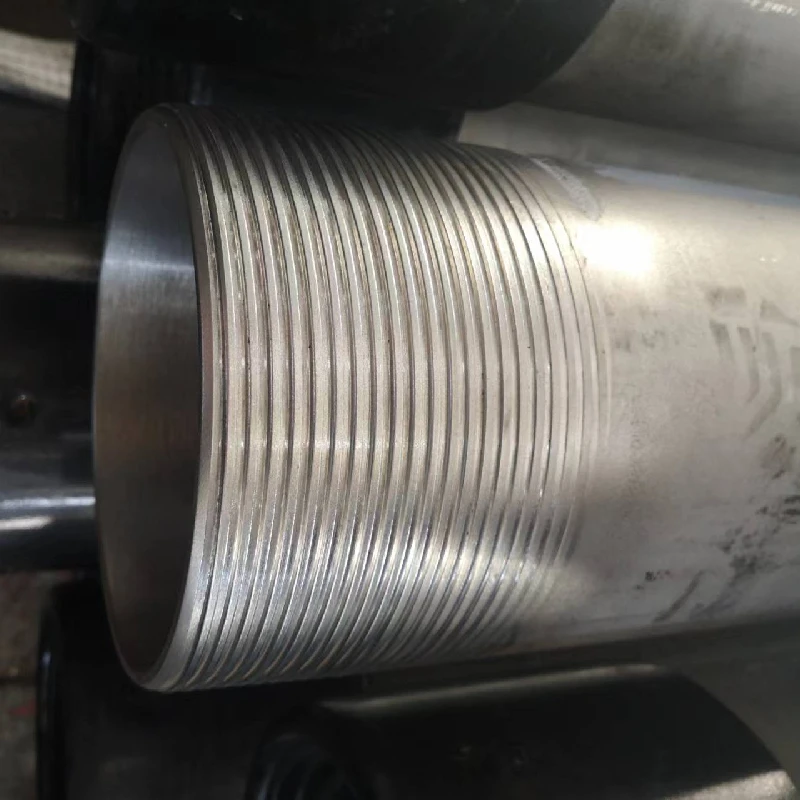
The authority of using perforated pup joints stems from their proven effectiveness in real-world applications. Companies across the globe have documented significant improvements in well performance metrics when implementing these joints in their completion strategies. Data-driven analyses have consistently shown enhanced well integrity and increased flow efficiency, resulting in a boost in overall production levels.
perforated pup joints
Trust in the use of perforated pup joints is bolstered by the extensive research and continual innovation within the field. Collaboration with academic institutions and industry experts ensures that the latest advancements in design and application are incorporated, keeping the technology at the forefront of modern extraction techniques. Additionally, adherence to international standards and certifications provides assurance to operators on the reliability and safety of these components.
From a practical perspective, the installation of perforated pup joints requires precision and expertise. Operators must be adept at determining the optimal placement and orientation of these joints within the wellbore to fully leverage their benefits. This often involves detailed subsurface imaging and simulation to map out the most effective configuration, underscoring the need for skilled personnel and sophisticated equipment.
In summary, perforated pup joints represent a confluence of expert engineering, authoritative performance, and credible research. Their implementation is critical to maximizing the efficiency of modern oil and gas extraction processes. Companies committed to utilizing cutting-edge technology and adherence to international best practices can expect substantial returns in productivity and operational integrity through the effective use of perforated pup joints.