In the intricate world of oil and gas exploration, the significance of well tubing and casing cannot be understated. These components serve as the backbone of any drilling operation, ensuring both the integrity and efficiency of drilling processes. Understanding the nuances of tubing and casing not only exemplifies expertise but also emphasizes the importance of these elements in ensuring successful oil extraction.
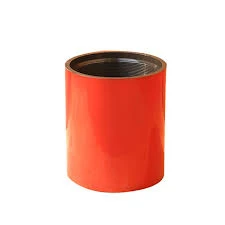
Well tubing and casing play distinct yet interconnected roles in drilling. Casing, the larger tubular structure, is utilized to line the wellbore, preventing its collapse and isolating different pressure zones within the borehole. The casing also safeguards groundwater from contamination by isolating it from drilling fluids and hydrocarbons. Tubing, on the other hand, is inserted into the casing to facilitate the flow of oil and gas from the reservoir to the surface. This distinction is crucial for operators and engineers alike, ensuring that each component is selected and applied correctly based on the geological conditions and operational requirements.
The materials used in constructing casings and tubing are paramount, considering the harsh conditions they endure. Typically made from carbon steel, these tubes are designed to withstand immense pressure and temperature variations. The selection process encompasses factors such as tensile strength, corrosion resistance, and the ability to withstand hydrogen sulfide environments. Expert knowledge in metallurgy and mechanical engineering becomes indispensable, as even slight errors in material selection can lead to catastrophic failures.
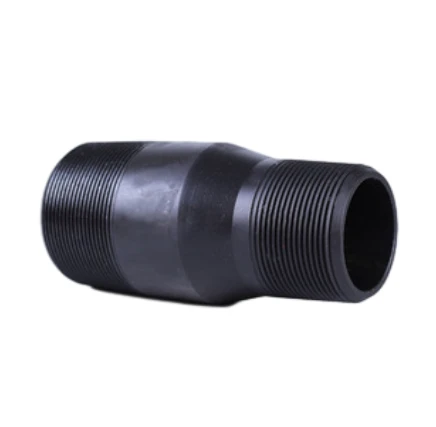
Installation processes demand acute precision and expertise. Ensuring proper cementing of the casing is crucial to provide a robust seal and prevent any unwanted fluid migration. This involves pumping specialized cement into the annular space between the casing and the wellbore, a process that requires careful calculation of volume and pressure. Missteps in this phase can lead to costly remediation efforts and, in severe cases, environmental disasters.
Recent advancements in technology have ushered in more sophisticated methods of well tubing and casing installation. Innovations such as expandable tubular technology allow for the expansion of casing once it is in place, optimizing wellbore diameter and enhancing production capacity. Additionally, the employment of real-time monitoring systems now enables operators to track the integrity and performance of the casing and tubing, allowing for prompt interventions when anomalies are detected.
well tubing and casing
An authoritative grasp of well tubing and casing extends beyond mere installation. Regular maintenance and inspection protocols must be adhered to throughout the lifespan of a well. Non-destructive testing methods, such as ultrasonic testing and magnetic flux leakage, are imperative in identifying potential weak points or failures. Expertise in these inspection techniques is vital, reinforcing the demand for skilled professionals who can interpret data and make informed decisions to avert operational downtimes.
Trust in the quality and reliability of well tubing and casing is bolstered by adhering to industry standards and regulations. Compliance with organizations such as the American Petroleum Institute (API) ensures that products meet stringent safety and performance criteria. Authoritative implementations not only enhance operational efficiency but also bolster confidence among stakeholders.
Endowing the operations with skilled personnel and cutting-edge technologies underscores the importance of embracing a comprehensive approach to well tubing and casing management. With each successful installation and maintenance routine, the industry not only safeguards its financial investments but also protects valuable environmental and human resources.
By synergizing expertise, technology, and robust methodologies, well tubing and casing operations can achieve unparalleled success in the ever-demanding landscape of oil and gas exploration. Prioritizing these elements not only maximizes production but also secures the sustainable future of drilling endeavors.