Tubing couplings are pivotal components in the oil and gas industry, acting as the essential connectors between segments of tubing. These couplings ensure the integrity and continuity of a pipeline, which is essential for both the safety and efficiency of extraction processes. As an oilfield engineer with extensive experience in tubing installations, the importance of selecting the right coupling cannot be overstated.
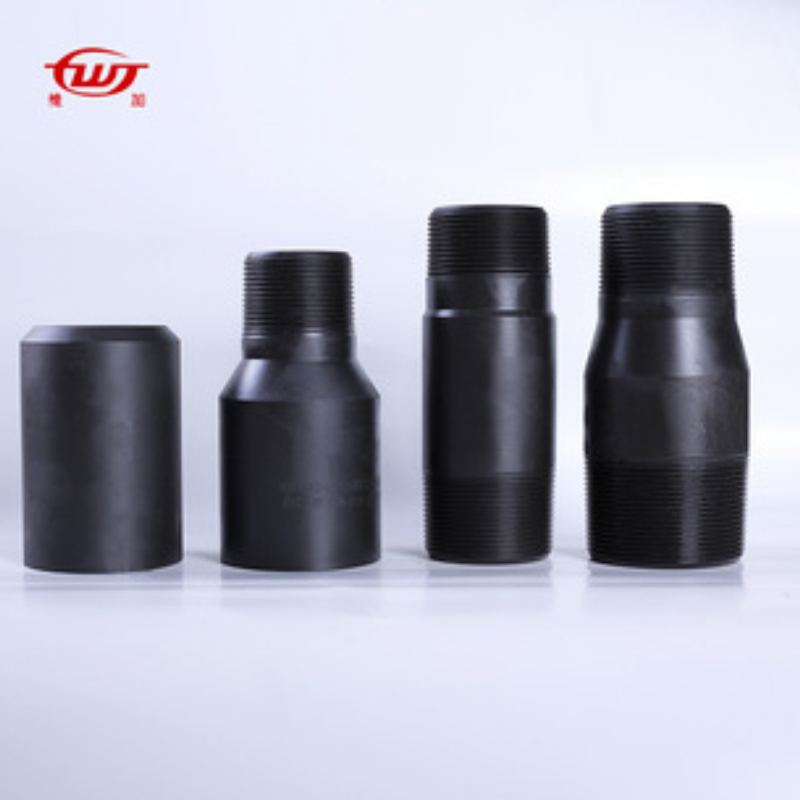
In environments where high pressure and fluctuating temperatures are the norms, the reliability of tubing couplings is crucial. From my own professional journey, dealing firsthand with the intricacies of this component, I have encountered scenarios that underline the value of high-quality couplings. A coupling failure can lead to significant downtime and financial loss, but more critically, it poses serious environmental and safety risks.
Choosing the Right Material
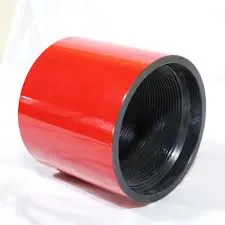
Selecting the appropriate material for a tubing coupling involves understanding the specific demands of the application at hand. Typically made from steel, couplings can be further classified depending on their material grade, such as J55, N80, or P110. These grades refer to the tensile strength of the steel, with higher numbers indicating stronger, more resilient products. For wells with high pressures and corrosive environments, materials like P110 provide the necessary durability. My expertise in handling various grades tells me that while higher grades often come with increased cost, their long-term benefits in terms of safety and maintenance often outweigh the initial expenditure.
Precision Manufacturing and Design
The design and manufacturing process of tubing couplings must adhere to stringent industry standards, such as those outlined by the API (American Petroleum Institute). In the design phase, precision is paramount. From threading dimensions to material treatments, everything is tailored to enhance the coupling's performance under stress. Advanced manufacturing techniques, including CNC machining, ensure consistency and precision. In my experience, a coupling's threads must meet precise tolerances to avoid issues such as galling or connection leakage. Inspections and quality control checks should never be compromised, as even a slight deviation can have significant repercussions down the line.
Industry-specific Expertise
tubing coupling
As an industry authority, it is crucial to remain informed about the latest advancements in tubing coupling technologies. Continuous innovations, such as the development of premium thread types that offer better sealing capabilities and easier make-up, redefine what is achievable. Companies are investing in R&D to engineer couplings that are lighter yet stronger, addressing both performance and cost-efficiency. My commitment to ongoing learning through workshops and industry seminars has been essential in maintaining an authoritative stance on tubing coupling applications.
Building Trust Through Certification and Compliance
The assurance of certification cannot be undervalued. In my professional tenure, I advocate for the procurement of couplings that have undergone rigorous testing and have been certified according to international standards.
Certifications are a testament to a coupling’s quality and reliability. Compliance with API and ISO standards not only facilitates trust but is often a requirement in contractual obligations, particularly with multinational operators.
Case Studies Real-world Insights
Reflecting on real-world applications, a case from the Permian Basin highlights the integral role of tubing couplings. A client faced recurrent failures due to substandard couplings that were not suited for the well’s pressure conditions. Upon applying expertise in product selection and coupling replacement with high-grade alternatives, operations saw a marked decrease in failure rates and an increase in operational uptime. This was a practical demonstration of how expert-driven decisions impact an entire project's success.
In essence, tubing couplings are more than just connectors; they are an investment in the operational efficiency and safety of a drilling operation. Their selection, informed by experience and backed by authority, ensures that pipelines perform at their peak, operators work within safe environments, and resources are extracted responsibly and efficiently.