In the world of industrial components, the battle between bull plugs and round head plugs is a testament to the complexity and specificity within the field. These two seemingly similar yet distinctly different components hold significant roles in various sectors, particularly in oil and gas industries, where they serve as essential tools for sealing and capping pipelines. Understanding the subtle but impactful differences between bull plugs and round head plugs can significantly enhance operational efficiency and safety, a vital tenet for those in the industry.
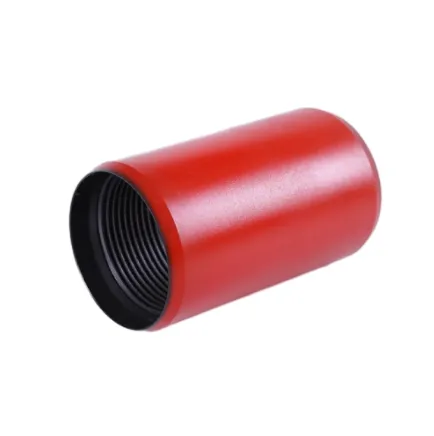
Bull plugs and round head plugs may appear interchangeable to the untrained eye, yet they are designed with unique specifications tailored to specific tasks. Starting with bull plugs, these conical-shaped fittings are specifically engineered to seal off the end of a pipeline. Manufactured with a thicker, broader base, bull plugs provide a robust seal and are ideal for high-pressure environments, which is why they are predominantly utilized in the oil and gas industries. The design focus is on durability and resistance to extreme conditions, characteristics that make bull plugs highly effective in withstanding the immense pressures of subsurface pipelines.
Round head plugs, in contrast, feature a flat, often circular head that allows for even distribution of sealing pressure across its surface. This design is particularly advantageous in applications where the plug must be flush with the termination point of the pipeline. Round head plugs are commonly used in applications where aesthetic appearance is important or where space is limited because their design allows for easier integration with surrounding surfaces or machinery.
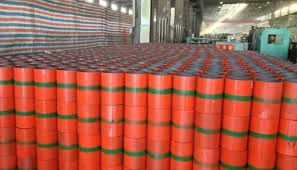
Technical specifics further distinguish these two types of plugs. Bull plugs are often crafted from high-strength steel or alloys, designed to endure harsh environments and potential exposure to corrosive materials. They provide a tighter and more reliable seal through their tapered design, which is often critical for preventing leaks in volatile environments. Conversely, round head plugs, while still robust, are frequently used in less demanding settings but are valued for their versatility and ease of installation and removal. The flat top allows for simple tooling and makes it easier to manipulate with conventional tools, thus requiring less specialized equipment.
bull plug vs round head plug
When evaluating which plug is most appropriate for a specific task, professionals in the field must consider several factors—pressure ratings, environmental conditions, and the nature of the fluid or gas within the pipeline. Bull plugs, with their robust design, are the go-to for sectors where maintaining a reliable seal is critical under high-pressure conditions. Round head plugs serve well in settings requiring frequent access or where the pressure demands are not as intense, making them a versatile option for countless applications.
In terms of installation and maintenance, both plugs require precise handling to ensure maximum efficacy and safety. Bull plugs, due to their size and the environments they are used in, often necessitate specialized tools or equipment for installation, a factor that underscores their suitability for heavy-duty industrial use. Round head plugs, however, offer a more straightforward installation process, lending themselves to projects where time and ease of access are paramount considerations.
A seasoned industry expert will note the importance of selecting the right plug based on the conditions and demands of the task at hand. This decision can directly impact the longevity of the equipment and facilitate smoother operations. Moreover, industry professionals emphasize the need for regular maintenance checks and replacements as part of routine safety procedures.
In conclusion,
understanding the differences between bull plugs and round head plugs is crucial for achieving peak operational efficiency and safety. By matching the plug type to the specific requirements of the environment and task, professionals can enhance the performance, safety, and lifespan of their industrial systems. Whether dealing with high-pressure scenarios or more general applications, the correct choice of plug contributes significantly to overall operational success, proving that even the smallest components can have the largest impacts.