Casing threads and couplings are integral components in the oil and gas industry, fundamentally designed to ensure the integrity and functionality of drilling operations. These elements work together to support the structural strength and longevity of casings used in oil wells. Understanding the intricacies of casing threads and couplings can significantly contribute to optimizing their selection and application, ultimately enhancing well efficiency and safety.
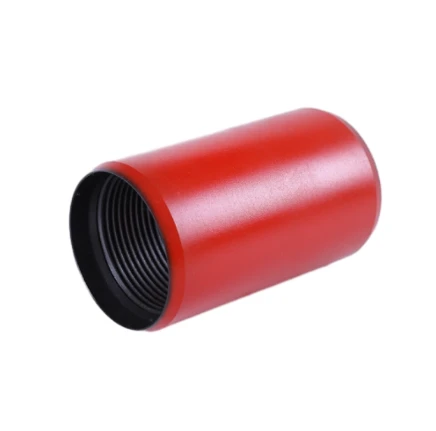
In the realm of casing threads, there are various types, each tailored for specific applications and load considerations. The most prevalent threading types are buttress and round threads. Buttress threads, with their square-shouldered design, are widely preferred in scenarios that demand high tensile strength. Their robust construction allows them to handle the immense pressures encountered during deep drilling operations, minimizing the risk of thread failure under extreme conditions. Round threads, on the other hand, provide an advantageous balance of strength and flexibility, making them suitable for diverse wellbore environments. The unique geometry of round threads facilitates easier stabbing during assembly and disassembly processes, which can be critical in time-sensitive drilling projects.
Couplings play a complementary role in the casing installation process. Acting as connectors, couplings link individual joints of casing pipe into a continuous string, maintaining a tight seal across threaded connections. Premium couplings, engineered with advanced metallurgy and precise machining, exhibit enhanced corrosion resistance and mechanical durability. These qualities are crucial in hostile subterranean environments where exposure to corrosive gases and fluids can severely compromise lesser materials. The ability to maintain joint integrity under harsh conditions is a testament to the coupling's critical role in well performance and longevity.
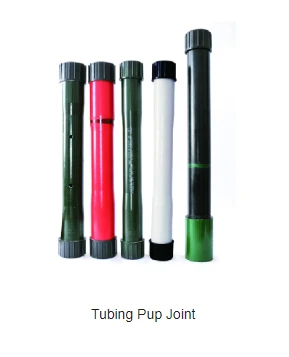
For oilfield operators, selecting the appropriate combination of casing threads and couplings requires a comprehensive understanding of geological conditions, anticipated well pressures, and operational objectives. Engaging with manufacturers who demonstrate expertise and a proven track record in supplying high-performance threading solutions is imperative. Manufacturers with certifications from leading industry standards, such as API (American Petroleum Institute), provide an added layer of trustworthiness, assuring operators that their threading solutions meet rigorous quality and safety standards.
casing threads and couplings
The real-world experience shared by seasoned drilling engineers highlights the tangible benefits achieved through the judicious selection of casing threads and couplings. Studies indicate that optimizing thread types to match specific drilling environments can lead to a significant reduction in the frequency of downhole failures. This not only improves operational efficiency but also translates to cost savings by minimizing non-productive time. Additionally, investing in premium couplings is often cited as a prudent long-term strategy to safeguard against unforeseen downhole challenges, thus preserving the integrity of critical drilling assets.
Advancements in material science have spurred innovation in threading and coupling technology, opening avenues for increased collaboration between engineers and material scientists. Emerging technologies, such as thread compounds engineered to reduce friction and wear, are gaining traction as they further enhance the performance lifespan of casing connections. These compounds play a crucial role in providing a protective barrier against galling and seizing during make-up and break-out operations, especially in scenarios involving repeated connections in multi-stage fracturing.
Trust in the durability and reliability of casing threads and couplings can significantly influence drilling success. Building this trust involves a commitment to thorough testing and quality assurance protocols before products reach the wellsite. Manufacturers often employ standardized testing procedures such as tensile load testing, fatigue testing, and full-scale joint make-up and break-out tests to validate the performance of their coupling and threading systems. Sharing test results and case studies transparently not only fosters trust among stakeholders but also reinforces the manufacturer's authority and credibility in producing high-quality products.
In conclusion, choosing the right casing threads and couplings is a strategic decision that impacts the efficiency, safety, and cost-effectiveness of oil well operations. By leveraging the expertise of industry leaders and integrating the latest technological advancements, oilfield operators can optimize casing performance to meet the demands of increasingly challenging drilling environments. Prioritizing quality and reliability in these critical components establishes a foundation for successful, safe, and economically viable drilling projects.