Tubing couplings play a crucial role in the oil and gas industry, serving as vital connectors between different sections of tubing. These components ensure the smooth flow of hydrocarbons from reservoirs to the surface. Understanding the intricacies of tubing couplings can significantly impact the efficiency and safety of drilling operations.
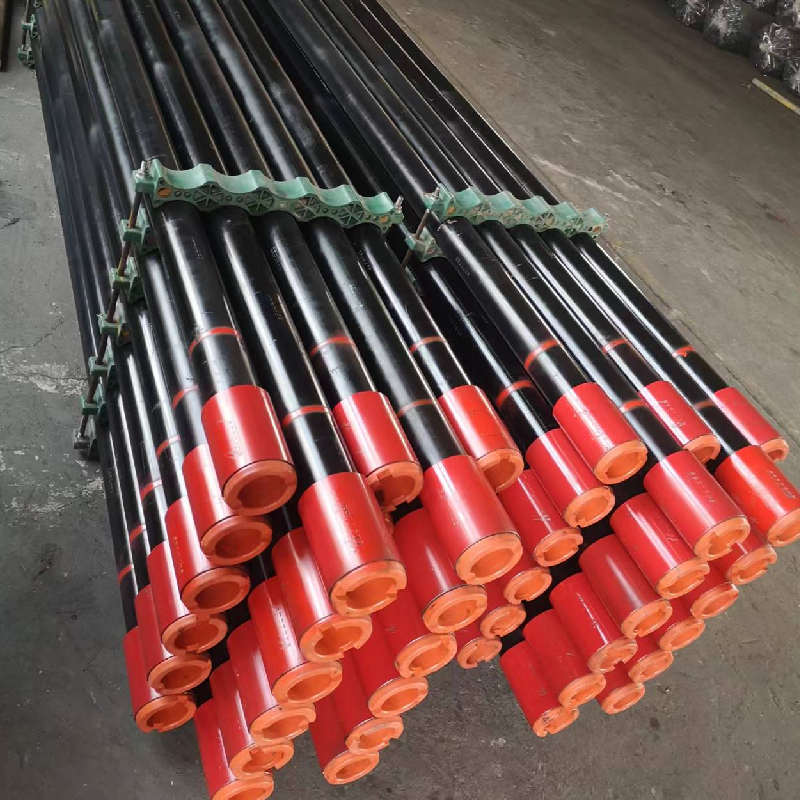
Tubing couplings are precision-engineered to withstand the extreme conditions encountered during drilling and extraction processes. This includes high pressures and temperatures, which underscores the importance of selecting the right type of coupling for specific applications. Each coupling must be designed to match the specific dimensions and requirements of the tubing it connects.
In practice, there are different types of tubing couplings, including standard API (American Petroleum Institute) couplings and premium couplings.
API couplings are standardized and are widely used for general applications. They are robust, reliable, and offer good performance under normal field conditions. However, in more challenging environments where increased resistance to corrosion, high pressure, and temperature are required, premium couplings are preferred. These are made from higher-grade materials and undergo rigorous testing to ensure their durability.
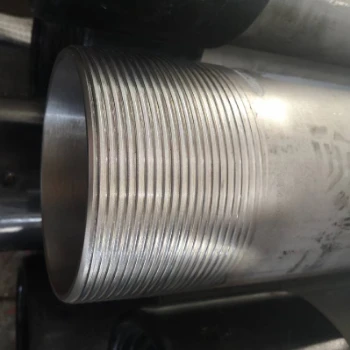
One of the critical considerations when selecting tubing couplings is the material. The most commonly used materials are carbon steel, stainless steel, and alloy steel. Carbon steel is cost-effective but may not offer the same corrosion resistance as stainless steel, making it less suitable for sour gas applications. Conversely, stainless steel and alloy steel provide excellent corrosion resistance and mechanical properties, making them ideal for extreme conditions.
Real-world experiences highlight the importance of regular inspection and maintenance of tubing couplings. Even the most robust couplings can suffer from wear and tear over time due to the harsh conditions under which they operate. Operators should implement regular inspection regimes using non-destructive testing methods such as ultrasonic testing or magnetic particle inspection. These ensure that any potential issues are identified and rectified before they lead to operational failures.
tubing coupling
Furthermore, the expertise of personnel handling the installation and maintenance of tubing couplings is paramount. Trained professionals who understand the technical specifications and operational nuances can ensure that couplings are installed correctly and maintained properly throughout their lifecycle. This reduces the risk of failures, which can lead to costly downtime and potential safety hazards.
Authoritative bodies like the American Petroleum Institute and the International Organization for Standardization provide guidelines and standards that oversee the manufacturing and testing of tubing couplings. Adhering to these standards enhances the quality and reliability of the couplings, fostering trust among end-users regarding their safety and efficiency.
Moreover, the coupling design continues to evolve, with advancements aimed at improving performance and extending the service life of the components. Innovations such as the use of advanced materials, enhanced thread designs, and coatings have all contributed to increased coupling reliability.
Establishing trust in tubing couplings also involves transparency from manufacturers about their testing and quality assurance processes. End-users should be informed about the specific tests that couplings undergo, such as pressure tests and fatigue tests, which are vital in determining their suitability for various applications. Ensuring transparency and accountability from suppliers builds confidence in the users who rely on these components for the safe and efficient operation of their drilling operations.
In conclusion, the strategic selection, expert installation, and diligent maintenance of tubing couplings are vital components of successful oil and gas operations. Their reliability ensures continuous production, reduces the risk of environmental incidents, and increases operational safety. As the industry advances, the continued development and understanding of tubing couplings will remain a focal point for professionals aiming to enhance efficiency and sustainability in resource extraction.