Pup joints might seem like a simple component at first glance, but their role in the oil and gas industry is crucial, enhancing both operational efficiency and safety. A pup joint is essentially a short length of pipe, used to adjust the length of tubular strings to suit the desired assembly in drilling or production. For those deeply entrenched in the industry, understanding the significance of these components can make a substantial difference in project outcomes.
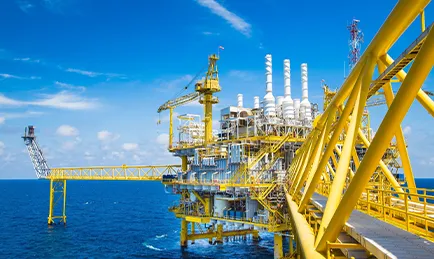
One of the essential experiences shared by professionals working with pup joints is the critical nature of selecting the right material. These joints are available in a variety of grades and materials, each suited for different applications. High-strength materials such as alloy steel are often recommended in more demanding environments. These materials provide durability and ensure reliability under high pressure and temperature conditions, which are common in deep drilling operations.
Industry expertise dictates that recognizing the specifications of pup joints—such as pressure rating, length, material composition, and connection type—is fundamental. This knowledge allows for the selection of the right pup joint that integrates seamlessly with the existing drilling string. In areas where hydrogen sulfide gas is prevalent, for example, a sour service pup joint must be selected for its resistance to sulfide stress cracking. Making informed decisions based on these specifications not only prevents operational downtimes but also minimizes safety risks.
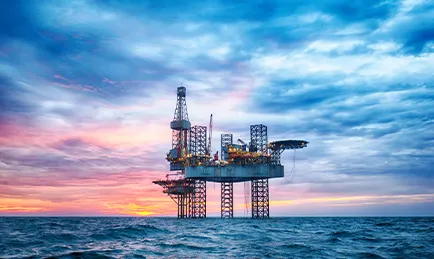
From an authoritative standpoint, major standards governing the manufacturing and use of pup joints are pivotal. In the petroleum sector, standards are not merely guidelines but are prerequisites set by bodies like the American Petroleum Institute (API). Every pup joint must meet rigorous standards, such as API 5CT for casing and tubing, to ensure they serve reliably in oil field operations. Operators and engineers rely heavily on these standards when purchasing and utilizing pup joints, ensuring they are both competent and compliant.
pup joint
Trustworthiness in pup joint products is also heavily reliant on the manufacturing precision and quality assurance processes. Leading manufacturers employ state-of-the-art technology in the forging and finishing of these joints to ensure they meet exacting industry standards. Nondestructive testing techniques such as ultrasonic and magnetic particle testing are often employed to guarantee integrity and reliability. Hence, choosing pup joints from a reputable supplier with a robust quality assurance program is imperative.
Real-world application and case studies further underscore the importance of the appropriate use of pup joints in drilling and production. Companies that invest in training their staff to understand the nuances of these components often report enhanced well productivity and reduced maintenance costs. Workshops and seminars led by seasoned professionals provide invaluable insights into innovative uses of pup joints, such as their role in pressure testing or as temporary flowlines during well operations.
Ultimately, the incorporation of pup joints speaks to a broader theme of strategic resource management in the energy sector. As energy demands continue to rise globally, ensuring the smallest components are optimized for performance can yield significant dividends.
Pup joints, though modest in appearance, embody the ingenuity and precision that define modern industrial operations. As such, their role is indispensable, guiding industry professionals toward smarter, more sustainable, and efficient practices.