In the evolving landscape of oil and gas exploration, the components used in drilling operations play an integral role in determining the efficacy and safety of the process. One quintessential component is the finished casing coupling, a tool that stands as both a protector and a facilitator in the drilling systems. Here, we delve deep into the world of finished casing couplings, exploring their significance, features, and the expertise required in their fabrication and application.
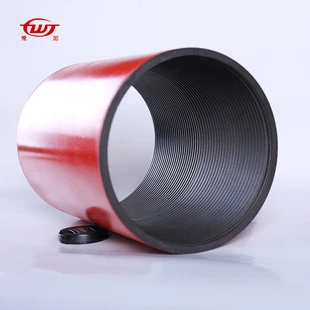
Finished casing couplings are pivotal in the construction of oil wells. They serve as the connectors between casing pipes, ensuring that the pipeline infrastructure is structurally sound and capable of withstanding the pressures of subterranean environments. To create a coupling that meets industry standards, manufacturers must exercise meticulous precision and extensive knowledge, drawing on years of experience to deliver a product that guarantees durability and reliability.
The expertise involved in designing finished casing couplings is not to be underestimated. These devices are engineered to endure extreme conditions, including high pressures, corrosive materials, and wide temperature variations. The choice of materials is critical; typically, high-grade steel alloys are used to offer the necessary toughness and resistance to corrosion. Manufacturers often apply various surface treatments or coatings to enhance these properties further, ensuring the longevity and performance of the coupling in demanding environments.
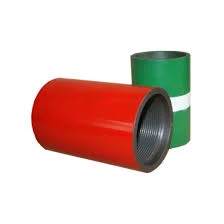
The manufacturing process involves stringent quality controls and state-of-the-art technology. Advanced CNC machinery is commonly utilized to achieve the precise threads and dimensions that are crucial for the seamless connection of casing pipes. Furthermore, couplings must conform to the industry's strict standards such as those set by the American Petroleum Institute (API) to ensure they can maintain the integrity of the well over its lifetime.
In terms of authoritativeness and trustworthiness, the producers of finished casing couplings often work closely with engineers and specialists in drilling technology. Through this collaboration, they continually refine designs and processes, contributing to the broader body of industry knowledge and setting new benchmarks for safety and efficiency. Review and testing, often conducted in collaboration with third-party certification bodies, validate the performance claims of these couplings, with rigorous assessments designed to simulate actual field conditions.
finished casing coupling
Field experience further underscores the value of high-quality finished casing couplings. In the oil fields, every component must perform flawlessly; failures can lead to catastrophic outcomes such as blowouts or environmental disasters. Operators with extensive experience know the importance of using reliable components, and the role finished casing couplings play in avoiding unnecessary downtime and ensuring consistent production.
Moreover, innovations in coupling design reflect a deeper understanding of downhole dynamics and the challenges faced by drilling engineers. Recent advancements include the development of premium threading profiles that reduce the risk of galling (seizing and tearing) and enhance sealing capabilities, thus providing additional security against leaks and other malfunctions. Such innovations not only improve operational safety but also optimize the economic efficiency of drilling activities by reducing maintenance needs and prolonging equipment lifespans.
Trust in finished casing couplings is ultimately built through consistent performance, adherence to industry standards, and verifiable testing and certification. Producers who prioritize transparency in their manufacturing processes and maintain stringent internal and external quality checks establish a foundation of trust with their clients. This trust is crucial as it allows oil and gas companies to operate with confidence, knowing that their infrastructure is supported by components designed to meet the highest standards.
In conclusion, finished casing couplings are much more than mere connectors; they are vital components engineered with precision, expertise, and a deep understanding of their critical role in well integrity. The commitment to quality from manufacturers, combined with continuous innovation and adherence to industry standards, solidifies their standing as trustworthy components in the complex machinery of oil extraction. Such a focus on experience, authority, and reliability transforms these couplings into indispensable elements that underpin the success of drilling operations worldwide.