Coupling casing serves as a critical component in various industrial and engineering applications, providing a seamless connection between pipes or other system elements to ensure fluid or gas flow without leakage. Over the years, the technology and materials used in manufacturing coupling casings have seen innovative advancements, making them more efficient and reliable than ever before.
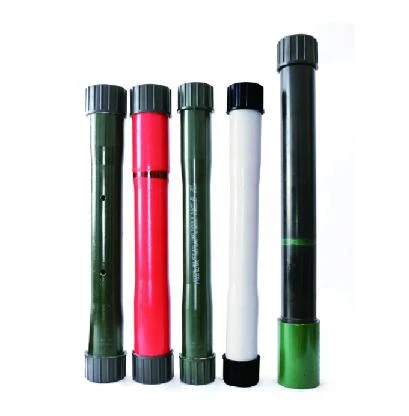
Experience plays a significant role in understanding the intricacies of coupling casings. Those with hands-on experience in installation and maintenance often emphasize the importance of precision in fitting to avoid potential operational issues. An experienced technician will always ensure that the casing is compatible with the environmental conditions it will face, such as pressure, temperature, and the chemicals it will convey. These real-world insights help in selecting coupling casings that result in longer-lasting, safer, and more efficient systems.
In terms of expertise, coupling casings are crafted from a variety of materials such as stainless steel, carbon steel, and alloys tailored to specific functions. Each material comes with its own set of characteristics that determine the casing's suitability for particular applications. Expertise in this field involves a deep understanding of metallurgy and material science, as well as familiarity with the industry standards and certifications that govern the use of these materials. For example, stainless steel casings are favored for their exceptional resistance to rust and corrosion, making them ideal for harsh environments.
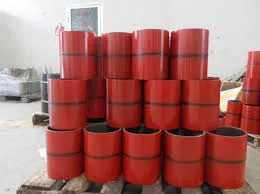
An authoritative perspective on coupling casing involves adhering to rigorous safety standards and regulations. Authoritative insights can be drawn from industry-leading manufacturers and bodies like the American Petroleum Institute (API) or ASTM International, which provide comprehensive guidelines and standards that ensure the safety and durability of coupling casings. Companies that align their products with these guidelines often gain a competitive edge through a reputation for reliability and performance, and they are frequently consulted for insights on emerging trends and technologies in casing design and functionality.
coupling casing
Trustworthiness in the selection and use of coupling casings is vital for establishing long-lasting relationships in business dealings.
Trust can be built through transparent manufacturing processes, robust quality controls, and exceptional customer support services. Companies that provide extensive warranties and clear documentation on the testing and performance of their casings win customers' trust. Reviews and case studies from credible sources further validate the reliability of their products.
A critical aspect of coupling casing that underscores its importance in various applications is its ability to maintain structural integrity under various stressors. This capability not only ensures efficiency but also serves as a preventive measure against accidents and spillages, which can lead to costly repairs and environmental damage. Whether used in oil and gas, chemical processing, or water treatment, the correct implementation of coupling casings can significantly enhance system safety and performance.
Innovations such as self-healing coatings, smart sensing technologies for pressure and temperature monitoring, and eco-friendly manufacturing processes are gradually shaping the future of coupling casing. By embracing these advancements, manufacturers not only improve their products' functionality but also contribute positively to global sustainability efforts.
In summary, coupling casing stands as an indispensable element in the architecture of modern industrial systems. Through a combination of experience, expertise, authority, and trustworthiness, businesses can effectively select and implement coupling casings that heighten operational reliability and efficiency while meeting contemporary safety and environmental standards. As technology continues to advance, the evolution of coupling casing solutions promises even greater enhancements to the fluidity and safety of industrial processes.