Coupling for tubing is an essential component in various industries, whether you're dealing with oil and gas pipelines, chemical processing plants, or even plumbing systems in residential settings.
The importance of selecting the right coupling cannot be overstated. In a world where efficiency, safety, and reliability are paramount, understanding the nuances of tubing couplings becomes crucial.
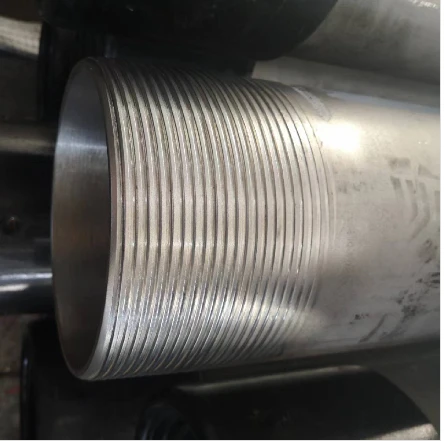
Couplings in the oil and gas industry, for example, play a vital role in connecting tubular segments, facilitating the seamless transport of resources from wellbore to processing facilities. The expertise required to choose the right coupling involves considering factors such as pressure ratings, environmental conditions, and the type of fluid being transported. A seasoned engineer will emphasize the necessity of matching coupling material with the tubing material to prevent galvanic corrosion, which can be critical in offshore applications where saline water can accelerate corrosion rates.
In chemical processing, the expertise extends to understanding the chemical compatibility of the coupling material. When dealing with corrosive chemicals, it's vital to use couplings made from materials like stainless steel or specialized alloys that can withstand harsh conditions without degrading over time. Failure to do so not only compromises the integrity of the tubing system but also poses significant safety hazards. Consulting with coupling manufacturers who have a proven track record in producing high-grade components for chemical plants can offer valuable insights and enhance the trustworthiness of the system design.
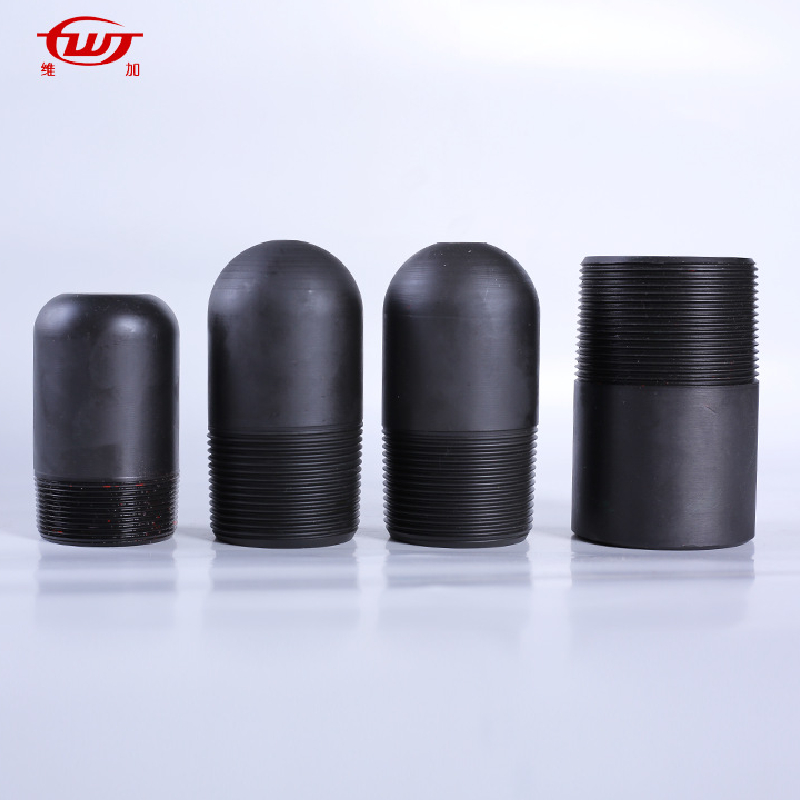
Authoritativeness in selecting couplings also derives from an understanding of the latest industry standards and regulations. ISO and ASTM standards provide comprehensive guidelines on the manufacturing, testing, and quality assurance of tubing couplings. Companies that adhere to these standards demonstrate their commitment to quality and reliability, instilling confidence in their clientele.
coupling for tubing
From a practical experience standpoint, installers and maintenance personnel often share valuable insights that shape coupling selection and maintenance strategies. Real-world scenarios reveal that regular inspections and maintenance of couplings can prevent environmental spills and costly downtimes. Experience has shown that investing in high-quality couplings with robust locking mechanisms can significantly reduce the risk of disconnections in high-vibration environments.
Furthermore, advancements in engineering have introduced smart coupling technologies that integrate sensors to monitor pressure and temperature changes in real-time. This innovation allows for proactive maintenance and detection of potential issues before they escalate into critical failures. Trustworthiness in this context is enhanced by data-driven insights, enabling operators to make informed decisions based on real-time metrics.
In residential plumbing systems, the significance of using the right coupling is no less important. Homeowners rely on the trustworthiness and expertise of plumbers to ensure their water and gas supply systems are leak-free and operate efficiently. Plumbers with extensive experience will often recommend specific brands known for their durability and ease of installation, which can save time and reduce the need for frequent repairs.
In conclusion, coupling for tubing is not just a minor component but a crucial element that demands careful consideration of experience, expertise, authoritativeness, and trustworthiness. Whether in industrial or residential applications, selecting the right coupling is key to ensuring system longevity, safety, and efficiency. As industries continue to evolve, staying informed about the latest developments in coupling technology and maintaining strong relationships with reputable manufacturers will remain indispensable for achieving operational excellence.