Pup joint tubing is an essential component in the oil and gas industry known for its versatility and crucial role in wellbore operations. These tubular segments, shorter than standard tubes, play a significant role in ensuring the optimal functioning of drilling and production wells. Their utilization offers several benefits including precise depth adjustments, flexible connection options, and cost-effective solutions in pipeline engineering.
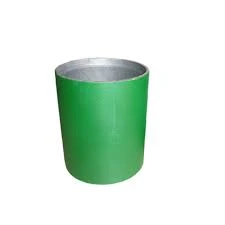
Drawing from firsthand experience and industry expertise, it's evident that pup joint tubings are indispensable in operations requiring precision. These small yet mighty tools ensure seamless connections in pipelines where exact length adjustments are necessary. Due to their ability to provide precise customization in wellbore depths, they eliminate the need for cutting longer pipes, thereby saving time, material, and labor costs.
Professionally speaking, pup joint tubing's variety caters to different wellbore challenges, from compensating for vertical pipe elongation to managing subsurface pressures effectively. They are generally available in different materials such as stainless steel, carbon steel, and various alloys, each serving specific environments and fluid types. This diversity underscores their adaptability, enabling operators to select the most appropriate material composition and length for their specific operational needs.
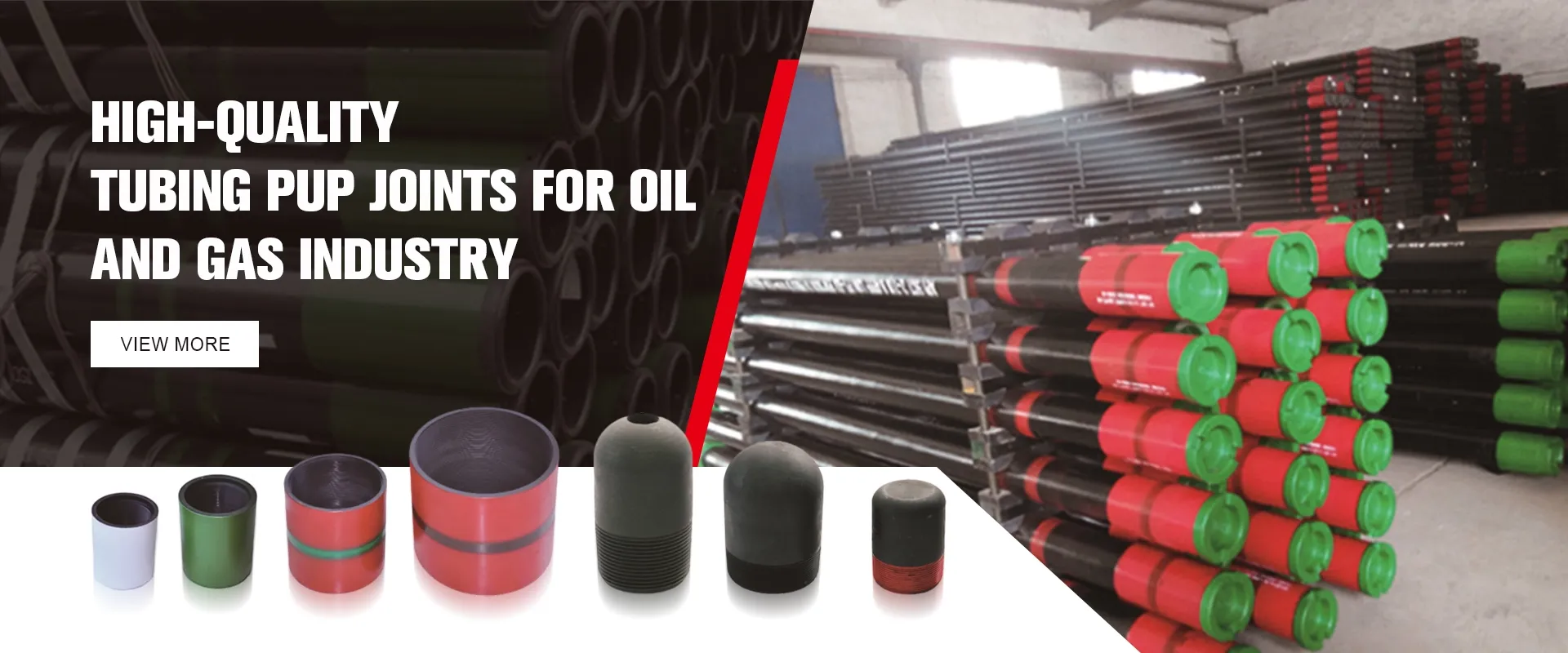
From an authoritative standpoint, pup joints are designed in compliance with industry standards, including API specifications, which enhance their reliability. Their design is meticulously configured to withstand extreme conditions prevalent in oil and gas exploration such as high pressure, temperature variations, and corrosive substances. This compositional integrity translates to a robust performance that operators can trust, ensuring safety and sustainability over extended periods.
pup joint tubing
The trustworthiness of pup joint tubing extends from quality assurance protocols that manufacturers adhere to. Rigorous testing, including hydrostatic tests and material certification, ensure that each piece meets stringent criteria before deployment. This dedication to quality not only protects against operational downtimes due to equipment failure but also safeguards the financial and environmental aspects of drilling ventures.
Moreover, advanced manufacturing technologies have rejuvenated pup joint tubing's applications, introducing enhanced threading techniques and precision engineering that bolster their ease of integration with existing infrastructure. This compatibility further simplifies logistical considerations for operators, providing a seamless installation process which reduces operational disruptions.
In conclusion, the indispensable role of pup joint tubing in oil and gas exploration is underscored by its versatile applications, unrivaled adaptability, and robust integrity. Its consistent performance contributes significantly to operational efficiencies while meeting industry standards, thereby fortifying its position as a trusted asset in the energy sector. With continual advancements in manufacturing and material science, pup joints are poised to maintain their critical status, providing tailored solutions to an ever-evolving industry landscape.