The world of oil and gas production is expansive and filled with a complex network of equipment that operates seamlessly to maintain efficient and safe extraction processes. A crucial component in this system is the tubing coupling, a product often underestimated but significant in its role. Based on years of field experience and professional expertise in the energy sector, this guide offers an authoritative insight into the intricacies of tubing couplings, emphasizing their importance, functionality, and best practices for ensuring reliability and performance.
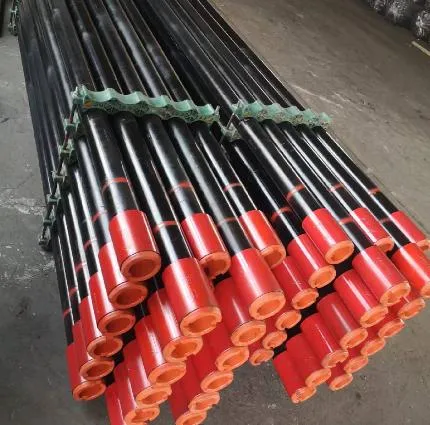
Tubing couplings serve as the connectors that join lengths of tubing in an oil well. These small yet mighty devices are built to withstand the unforgiving and high-pressure environments typical in subterranean oil extraction. Their primary function is to ensure a tight, leak-proof connection between tubing segments, which prevents valuable product loss and mitigates potential hazards such as blowouts. For professionals in the field, understanding the nuances of tubing couplings can significantly impact operational efficiency and safety compliance.
Over the years, hands-on experience has taught us that the choice of coupling material is critical. Carbon steel, stainless steel, and various alloys are commonly used materials, each selected for their specific properties such as tensile strength, corrosion resistance, and cost-effectiveness. The right material choice not only extends the lifespan of the coupling but also enhances its ability to withstand the specific environmental conditions of the well.
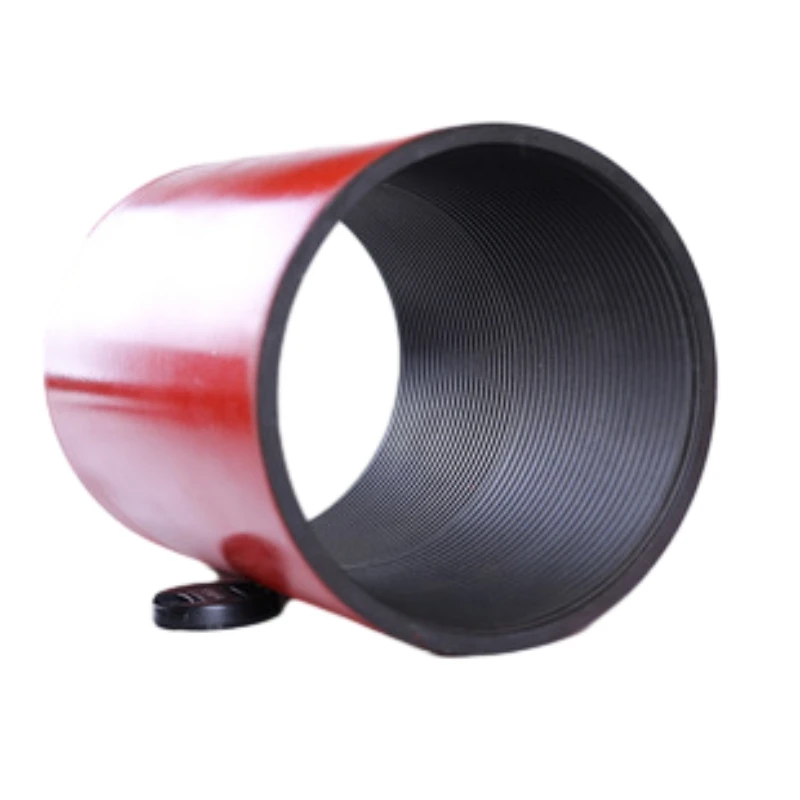
Another aspect to consider is the coupling design.
The two main types are threaded and torqued couplings. Threaded couplings are prevalent in standard operations due to their ease of use and versatility. However, torqued couplings, which require precise equipment to ensure proper torque levels, are preferred in high-pressure scenarios due to their superior sealing capability. Achieving the correct torque is vital; too little could result in leaks, while too much may cause the coupling to fail.
tubing coupling
Quality control and standard compliance are non-negotiable for tubing couplings. API (American Petroleum Institute) standards are the benchmark for all coupling products, ensuring they meet the rigorous requirements for industrial safety and performance. Each coupling should undergo comprehensive testing, including pressure testing, material hardness checks, and dimensional accuracy inspections, to certify their integrity before deployment.
Real-world expertise underscores the significance of routine maintenance and inspection. Oil field veterans emphasize that even the most robust couplings can succumb to wear over time, exacerbated by extreme temperatures and chemical exposure. Implementing regular inspection schedules can detect signs of wear such as cracks, corrosion, or thread deformation early, preventing costly downtimes or catastrophic failures.
For professionals seeking to invest in high-quality tubing couplings, building trust with suppliers is crucial. Work with suppliers whose reputation is backed by consistent product quality and adherence to industry standards. Look for manufacturers that provide comprehensive documentation of their quality control processes and are transparent about their raw material sourcing.
In conclusion, tubing couplings are indispensable to the smooth operation of oil extraction processes. Their selection, installation, and maintenance demand careful consideration, guided by expert knowledge and proven industry practices. By prioritizing quality materials, adhering to design specifications, and conducting diligent maintenance, operators can trust in the reliability and safety of their coupling systems. Such adherence to industry best practices not only affirms the trustworthiness of the equipment used but solidifies an operator’s reputation for safety and efficiency in the competitive oil and gas sector.