The oil and gas industry is an intricate field where precision and accuracy significantly impact the outcomes. Among the critical components in this industry are casing and tubing—vital in the drilling, completion, and production stages of a well. Although they appear similar, casing and tubing serve fundamentally different purposes and entail unique characteristics that industry professionals must clearly understand.
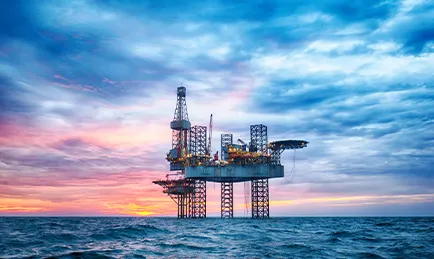
Casing serves as a structural retainer for the wellbore, and it is crucial in maintaining the well's integrity. Essentially, casing is a series of steel pipes placed in the well after drilling to prevent collapse of the borehole. There's a specific need to distinguish casing as it undergoes various roles providing support to the walls, preventing contamination from surrounding formations, and serving as a conduit for production tubing. Casing is installed in sections, which can include surface casing, intermediate casing, and production casing. Each layer offers unique applications and protects environmental integrity by locking in different geological subsurface areas.
On the other hand, tubing is geared towards transporting the oil and gas from the reservoir to the surface after the well has been completed. Unlike casing, tubing's diameter is considerably smaller as it needs to fit within the casing. The tubing must be replaceable and allows for the flow of hydrocarbons during the production phase. Tubing may also be subject to higher temperature and pressure conditions than casing since it directly handles the extracted substances.
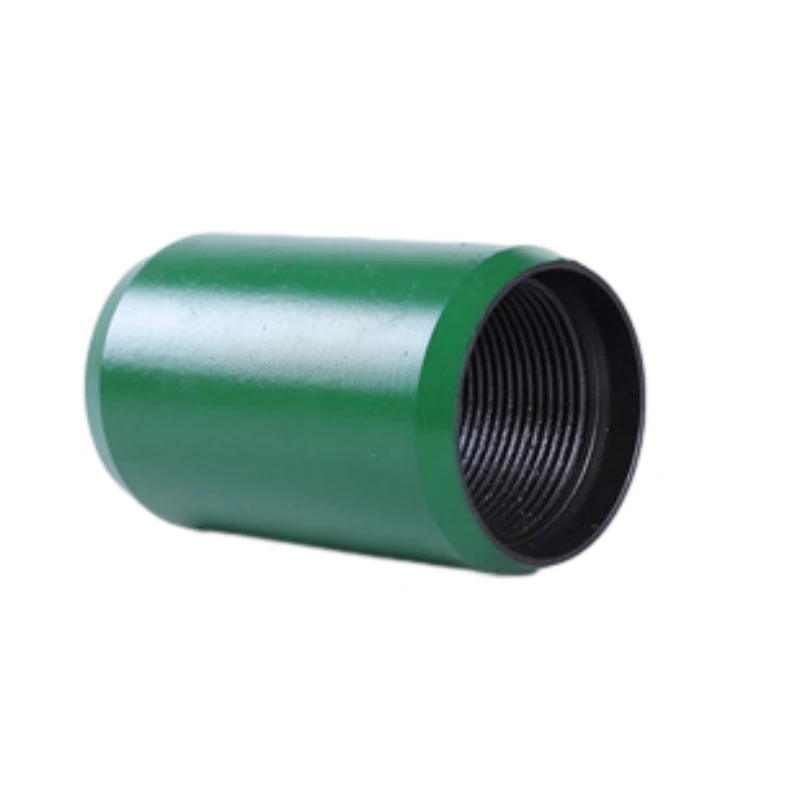
The fundamentally distinct functions necessitate different material properties and installation techniques. Casing is required to fulfill a supporting role, thus requiring a focus on thickness and strength. To combat the collapsing pressure from external forces, casing typically features thicker walls and a larger diameter. This necessity also means casing undergoes stringent engineering processes to ensure it can withstand substantial geological pressures and corrosive elements.
what are the differences between casing and tubing?
Tubing, conversely, has a more dynamic function. Here, the emphasis is placed on flexibility and allowing efficient flow dynamics, as fluids often have to be moved long distances vertically. The design of tubing is optimized for replacing and adjusting to production rates, which demands a refined material selection to ensure the long-term economic feasibility of well operations. The joint integrity and connection structure are critical in tubing, providing a secure seal without hampering fluid movement.
Professional understanding and application of these differences are essential for efficient and safe oil extraction processes. The implications of selecting incorrect materials or misapplying casing versus tubing can lead to disastrous results. For example, improperly installed casing can lead to well collapse or uncontrolled release of hydrocarbons. Similarly, ill-sized tubing can cause significant flow restrictions or erosion, thus impacting productivity and safety.
Moreover,
technological advancements continue to enhance the utility and efficiency of both casing and tubing. Innovations like enhanced alloys, corrosion-resistant coatings, and novel installation techniques further blur the traditional limitations and differences. However, these advancements demand continuous learning and adaptation from industry professionals to ensure the effectiveness of their applications is maximized.
In summary, casing and tubing are not merely interchangeable terms but represent specialized equipment with distinct roles in the oil and gas industry. Their differences are defined by functions—casing providing structural support and zonal isolation, while tubing focuses on efficient transportation of production fluids. Factoring these disparities into engineering and operational decisions is a fundamental component of well management, guaranteeing both technical success and economic sustainability in hydrocarbon recovery. Understanding these nuances and leveraging the latest advancements allows industry professionals to maintain their authoritative and trustworthy positions, securing optimal results in an ever-evolving field.