In the oil and gas industry,
understanding the distinction between casing and tubing is crucial for both engineers and investors. While these terms might seem interchangeable to the uninitiated, they actually refer to two distinct parts of the well completion process, each playing a critical role in the safe and efficient extraction of resources.
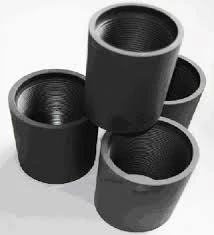
Casing and tubing are integral components of the wellbore, the hole drilled into the earth to reach oil and gas deposits. Both are types of metal pipes used in drilling, but they serve different purposes and are utilized at different stages of the drilling and production process.
Casing, a robust steel pipe, lines the wellbore to stabilize it, prevent the surrounding rock from collapsing, and protect freshwater aquifers from contamination. The use of casing is one of the first steps post-drilling. Its structural integrity is crucial; therefore, it must be strong enough to withstand the various pressures and temperatures encountered deep underground. Casing sizes and specifications vary depending on the depth and type of the well, and it is typically cemented into place to provide a permanent and reliable barrier against the oil, gas, and any undesired fluids in the surrounding formation. The installation involves several layers, starting with a surface casing for freshwater protection and continuing with intermediate and production casings as necessary. This layered approach ensures that each level secures the well integrity against different subsurface conditions.
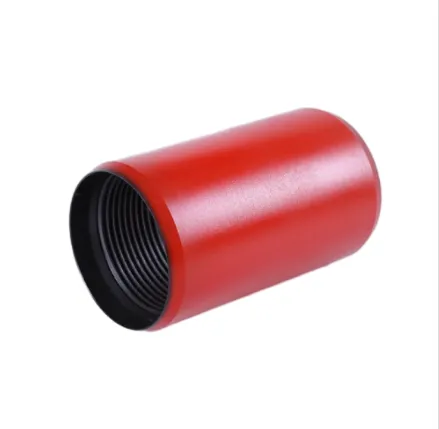
In contrast, tubing is inserted into the casing after the well has been drilled and secured. Its primary function is to act as a conduit for transporting the hydrocarbons from the production zone to the surface. Unlike casing, tubing is not cemented down but is removable and replaceable, making it essential for the continued maintenance and productivity of a well. Tubing allows for control over the flow of resources, optimizing production rates while minimizing the risk of well damage. The use of various tubing sizes can influence production rates and manage pressure conditions effectively. Additionally, different tubing materials and coatings may be employed to combat corrosion and scaling, which are common challenges in hydrocarbon production.
what is the difference between casing and tubing?
The decision to utilize specific casing and tubing setups hinges on several factors, including the depth of the resource, the type of fluid being extracted, and the geological characteristics of the drilling area. The casing forms the backbone of a well’s architecture, and all other components, such as tubing, depend on its integrity. On the other hand, efficiently designed tubing can significantly impact the overall productivity and longevity of a well by reducing the need for frequent interventions and repairs.
In terms of investment, understanding the differences between casing and tubing can aid stakeholders in making informed decisions regarding the viability and longevity of a project. An efficiently cased and tubed well reduces environmental risks and increases operational efficiency, providing more favorable returns.
In conclusion, while casing and tubing may appear similar as they are both pipe structures used within wells, their roles, functions, and timing of deployment within the drilling and production process are distinct. Casing provides the necessary support and protection for the wellbore, while tubing serves as the vital channel for resource extraction. These components, though different, are interdependent and vital to the successful and sustainable operation of oil and gas wells. Understanding their differences and how they complement each other is crucial for ensuring the long-term productivity and safety of drilling operations.