A bull plug, an often-overlooked component in the oil and gas industry, plays a crucial role in maintaining the integrity and efficiency of drilling operations. Made typically of high-grade steel to withstand immense pressures and corrosive environments, the bull plug is primarily used to seal the end of the pipe or pipe fitting threads. This seemingly simple tool contributes significantly to the safety and functionality of complex oilfield operations.
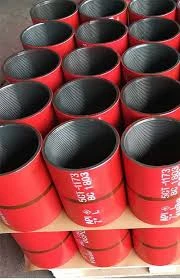
The choice of a bull plug can greatly impact operational efficiency. When chosen correctly, it helps prevent leaks and spills, securing the system against hazardous events. A high-quality bull plug will have a precisely machined surface for mating with pipe threads, ensuring a tight seal that reduces the likelihood of thread galling - a common issue when two metal surfaces wear against each other. This not only preserves the integrity of the piping system but also extends its lifespan, reducing the need for frequent replacements or repairs.
Professionals in the field emphasize the importance of selecting the appropriate material and size for each specific application. For instance, in corrosive environments or those involving high temperatures, materials such as stainless steel or specific alloys are recommended due to their superior resistance to degradation. Oversizing or undersizing the bull plug can lead to ineffective sealing or even structural failure, which could lead to costly downtime or environmental damage.
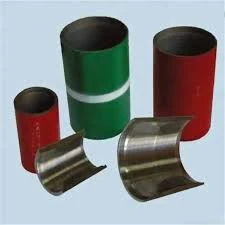
In addition to sealing applications, bull plugs serve as an essential component for pressure testing various sections of piping or vessel systems. By effectively sealing one end, operators can accurately assess the pressure capacity and integrity of a system before beginning normal operations. This precaution helps in identifying potential weaknesses or defects that could lead to catastrophic failures, ensuring the safety of personnel and equipment.
what is a bull plug used for
Field experts often stress the importance of regular maintenance and inspection of bull plugs. Over time, even the most robust bull plugs can wear due to constant exposure to harsh environmental conditions and repeated pressure cycles. Routine inspections for signs of wear, corrosion, or damage are vital to ensure that the bull plug continues to function effectively. Some advanced bull plug designs even incorporate anti-corrosion coatings or surface treatments that further enhance their durability and lifespan.
A common practice among seasoned oilfield professionals is keeping a detailed log of when each bull plug is installed and the conditions it has been exposed to. Such records provide valuable data that can assist in predicting when a bull plug is nearing the end of its useful life, thus allowing for timely replacements and avoiding unpredicted system failures.
In sum, the bull plug, though a small component, holds a pivotal place in the safety and efficiency of oil and gas operations. Its correct application can mean the difference between a smoothly running operation and a costly, potentially hazardous situation. As technologies and materials continue to advance, the functionality and reliability of bull plugs are bound to improve, further reinforcing their critical role in the ever-evolving energy sector. Selecting and maintaining the right bull plug not only upholds operational integrity but also aligns with best practices in safety and environmental stewardship, showcasing expertise and authority in the industry.