In the complex landscape of oil and gas production, the integration of reliable equipment is pivotal to ensure safety, efficiency, and sustainability. Among the myriad of components essential to this sector, the bull plug emerges as a vital tool, underscoring its importance in both operational integrity and environmental preservation.
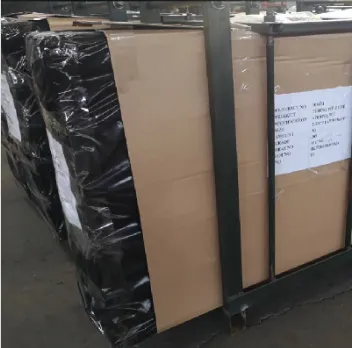
Bull plugs are simple yet crucial devices used primarily to seal off the end of tubular piping or fittings. This relatively unassuming component plays a critical role in maintaining the integrity of oil and gas operations. Typically forged from high-grade stainless steel or similarly durable materials, these devices embody the durability and strength needed for the demanding conditions of drilling and extraction activities.
In terms of experience, workers in the oil and gas sector often emphasize the indispensable role of bull plugs in maintaining system integrity and preventing leaks. Many seasoned professionals recount instances where a reliable bull plug prevented significant material loss, becoming a safeguard against potential environmental hazards. These firsthand testimonies underscore the product’s real-world applicability and significance, reinforcing its place as a non-negotiable element in operational checklists.
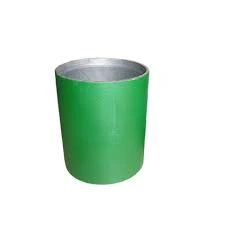
From an expertise standpoint, the design and material composition of bull plugs speak volumes about their intended application. Engineers opt for materials such as 316 stainless steel or carbon steel based on specific requirements—taking into account factors such as pressure resistance, temperature variance, and potential corrosive exposure. Detailed engineering specifications are crucial, as the misalignment of materials under high pressure can lead to catastrophic failures. Expertise in metallurgy and pressure systems is paramount to inform these design choices, ensuring that the bull plug performs effectively under the rigors it faces.
Bull plugs are not simply closed-end caps; they function under the authority of rigorous industry standards. Institutions like the American Petroleum Institute (API) and the American Society of Mechanical Engineers (ASME) set stringent guidelines for manufacturing, ensuring that each unit meets or exceeds safety and performance criteria. Companies producing these components provide guarantee-backed certifications, offering further peace of mind to purchasers that the products are up to the task.
bull plug oil and gas
Trustworthiness of bull plugs is not only derived from compliance with industry standards but also from the legacy of manufacturers. Provenance can play a critical role; reputable manufacturers with a history of reliable outputs are preferred partners in the procurement process. Testament to their reliability, a well-manufactured bull plug can provide service for years without failure, instilling confidence in their deployment across projects varying in scale and complexity.
Furthermore, the selection process for bull plugs integrates comprehensive testing methods. Hydrostatic and pressure tests are standard procedures employed to validate the effectiveness of a bull plug against expected operational conditions. In some scenarios, enhanced testing under simulated conditions can further assure stakeholders of the product's reliability and efficacy.
In a market driven by cost-effectiveness, the debate between initial investment and long-term savings often arises. Bull plugs, despite their upfront cost, offer substantial savings by preventing costly leaks and system failures. Their role in avoiding unplanned shutdowns and minimizing environmental risks underlines a strategic investment in operational continuity.
In summary,
the bull plug is far from just another component in the long list of oil and gas tools. It embodies a confluence of experience, expertise, authority, and trust that underscore its importance in the sector. Selecting the right bull plug is a decision that impacts operational efficiency, financial prudence, and environmental stewardship. As such, understanding the implications of material selection, production standards, and manufacturer reliability is essential to leverage the full potential of this crucial device, ensuring that it is not merely a stop-gap, but a linchpin in robust and sustainable oil and gas operations.