Casing coupling dimensions play a pivotal role in the oil and gas industry, especially in well construction and integrity. Understanding these dimensions is essential for professionals seeking reliability and efficiency in their drilling operations. This article explores the nuanced dimensions of casing couplings, providing in-depth insights into their significance in maintaining wellbore stability and ensuring successful drilling campaigns.
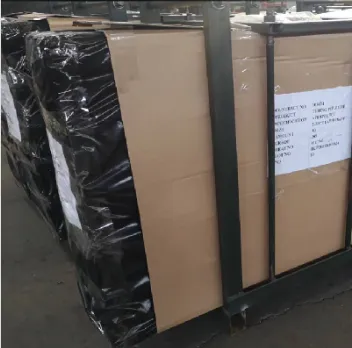
Casing couplings are integral components used to connect two joints of casing or liners downhole. Their dimensions, which are standardized, affect not only the mechanical integrity but also the operational success of drilling projects. A precise understanding of casing coupling dimensions—such as outside diameter, internal diameter, length, and thread specifications—ensures that operations adhere to both safety and regulatory standards across the globe.
The outside diameter (OD) of a casing coupling is crucial for compatibility with casing pipes, allowing for a seamless connection. Typically, casing couplings are manufactured in accordance with API specifications, such as 5CT, which standardizes dimensions to suit varied depths and pressures. Adequate OD selection prevents stress concentration points along the casing strings, thus reducing potential failures and ensuring the pipelines can withstand external pressures exerted by geological formations.
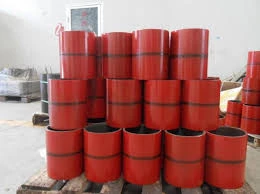
Equally important is the internal diameter (ID) of the coupling, as it dictates the flow capacity within the casing string. A coupling with a smaller ID can restrict mud circulation or even impede the passage of necessary downhole tools during operations. Engineers must balance the ID to optimize flow without compromising the structural integrity of the coupling. Proper ID sizing enhances wellbore cleaning and minimization of surge pressures during tripping, facilitating a smoother drilling process.
Length is another critical dimension of casing couplings. While standard couplings have fixed lengths, options for longer versions are available to provide additional joint strength where needed. An optimal coupling length supports uniform load distribution and promotes better thread engagement, reducing the risk of joint failure under axial loads or torque during well operations.
casing coupling dimensions
Threading specifications, another dimension, are vital for ensuring secure coupling connections. Threads must align with international standards like API or proprietary designs that guarantee leak-proof seals. The thread design impacts the assembly torque required and the ease of makeup, which is vital for maintaining operational efficiency and safety.
Beyond these fundamental dimensions, technological advancements have paved the way for innovations in coupling materials and coatings, enhancing corrosion resistance and extending the service life of well casings. Composite materials or advanced steel alloys offer increased durability, making them ideal for harsh environments such as deep-water wells or high-temperature reservoirs. These innovations address common challenges faced in the field, like corrosion, fatigue, and wear, helping to sustain the longevity of drill strings.
Industry experts emphasize the importance of regular inspections and maintenance to ensure that couplings remain within operational tolerances and dimension specifications. Non-destructive testing methods (NDT) such as ultrasonic or magnetic particle testing are employed to detect any anomalies or degradation that could compromise the coupling's integrity.
In conclusion, understanding the dimensions of casing couplings is not merely a logistical necessity but a critical factor in the successful execution of drilling operations. By adhering to industry standards and embracing technological advancements, professionals in the oil and gas sector can ensure the reliability and safety of their drilling activities, mitigating risks associated with wellbore instability and equipment failure.
Investing in quality casing couplings and maintaining a comprehensive grasp of their dimensions propels efficiency and maintains the trust of stakeholders, affirming the company’s commitment to excellence and operational safety in every project.