Exploring the Intricacies of Casing Coupling Dimensions for Optimal Performance
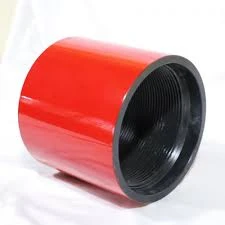
In the dynamic world of oil and gas extraction, understanding the specifications of casing coupling dimensions is critical for ensuring structural integrity and maximizing operational efficiency. Casing couplings play a fundamental role in connecting pipe segments, thereby fortifying the well structure against extreme pressures and corrosion. For professionals in the energy sector, possessing a comprehensive grasp of these dimensions is indispensable.
Casing couplings are pivotal in subterranean drilling applications, where each component must perform flawlessly under harsh environmental conditions. Dimensions of these couplings can influence the overall stability and lifespan of an oil well. The substantial difference between a seamless operation and a costly disruption often comes down to the precise fit and endurance of the casing and its coupling.
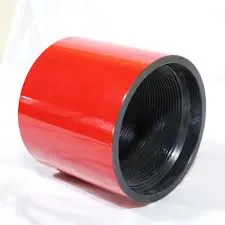
When evaluating casing coupling dimensions, industry experts consider a variety of factors. Diameter, length, and coupling type are primary attributes that dictate how well the casing will perform under load. Standardized measurements generally follow guidelines set by the American Petroleum Institute (API) to maintain uniformity across the industry. These standards ensure that casing pipes and couplings from different manufacturers can seamlessly integrate, providing a highly reliable and interchangeable system.
Diameter is one of the most straightforward yet critical measures. Ranging from 4.5 inches to as large as 20 inches or more, the diameter must match with the specifications required by the well design. Choosing the appropriate diameter involves understanding the well's total depth and pressure conditions, where larger diameters can withstand greater pressures.
Equally important is the length of the casing and its coupling, which should accommodate the required depth while ensuring adequate overlap between pipes. This overlap, or joint strength, is key to withstanding the axial and radial loads during drilling operations. The longer the coupling, often referred to as extended-range couplings, the greater the stability it provides. But a balance must be struck to avoid excessive weight, which can complicate handling and installation.
casing coupling dimensions
Casing coupling types vary depending on their connection profiles, including buttress thread, long round thread, or premium connections. Each of these types serves specific operational needs, with premium connections offering enhanced sealing capabilities for high-pressure wells. The coupling's thread design must be chosen with an eye towards both ease of assembly and its ability to maintain a flawless seal.
The material composition of casing couplings cannot be overlooked. Typically crafted from high-grade steel, couplings are subjected to rigorous testing and heat treatment processes to enhance their resistance to wear and environmental degradation. Material choice is driven by operational demands, where wells with higher corrosive potential might require specialized alloys such as stainless steel or nickel alloys.
Establishing trust in casing products relies heavily on certification and testing. Manufacturers must adhere to API specifications while also encouraging independent testing for verification. Documentation of a casing coupling's performance in different environments provides a robust framework for assessing reliability and durability.
From an engineering perspective, the true value of understanding casing coupling dimensions lies in predictive maintenance. Utilizing advanced modeling and simulation tools, engineers can anticipate wear patterns and potential failure points, ensuring interventions are timely and effective without impeding operations.
In conclusion, the dimensions of casing couplings are not mere numbers on a specification sheet; they are the lifeline that supports the safety and efficiency of oil extraction operations. A keen understanding of these dimensions, supported by rigorous testing and certification, builds the foundation for robust well design. For industry professionals, maintaining expertise in the latest advancements and industry standards ensures that they not only meet but exceed operational demands, establishing a resilient framework in an ever-evolving energy landscape.