Tubing couplings are integral components in the oil and gas industry, serving a critical function in the well construction process. These small but pivotal components are designed to connect different sections of tubing, ensuring the seamless and safe transmission of oil and gas from the reservoir to the surface. Beyond their fundamental role in connectivity, tubing couplings are engineered to withstand the harshest environmental conditions, providing a reliable solution in complex drilling operations.
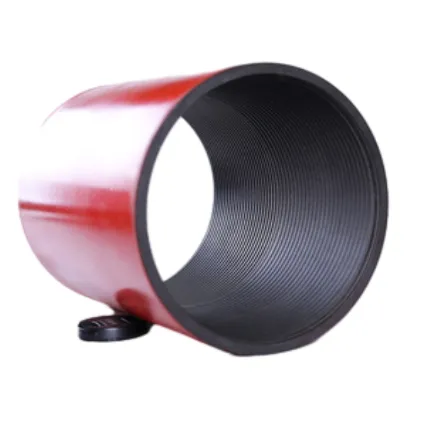
Understanding the intricacies of tubing coupling starts with their construction material. Typically made from steel, these components are built to resist not only the extreme pressures encountered deep underground but also the corrosive effects of saline water and hydrocarbon mixtures. Through precise metallurgical processes, tubing couplings are manufactured to meet stringent API (American Petroleum Institute) standards, ensuring compatibility and interchangeability in varying drilling scenarios.
The Evolution of Tubing Couplings
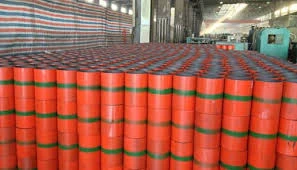
Advancements in technology have not left tubing couplings behind. Innovations in metallurgy and design have led to the development of couplings that possess enhanced sealability and torque resistance. Modern tubing couplings often incorporate proprietary thread designs that minimize the risk of leakage and unfastening. These improvements not only augment the reliability of couplings but also prolong their service life, reducing the frequency of interventions and associated costs.
In recent years, the focus on environmentally sustainable drilling practices has further influenced the evolution of tubing coupling technology. Developers are increasingly exploring eco-friendly coatings and materials that minimize environmental impact without compromising on strength or durability. This shift is crucial as the industry faces mounting pressures to mitigate environmental footprints while maintaining operational efficiency.
Expert Insights on Selecting the Right Tubing Couplings
Choosing the correct tubing coupling involves a deep understanding of well requirements and operational conditions. Experts emphasize the importance of considering factors such as the well depth, pressure, temperature, and fluid composition. For instance, high-pressure high-temperature (HPHT) wells necessitate couplings that can endure elevated stress levels without deformation or failure.
Moreover, the role of threading in tubing couplings cannot be understated. Thread types vary significantly, with some designed for easy assembly and disassembly in frequent operational changes, while others offer high resistance against loosening in high-vibration environments. It is critical for practitioners to consult with manufacturers and leverage their expertise to select the optimal thread configuration and material type for specific applications.
tubing coupling
Building Trust with Quality Assurance
Quality assurance is a cornerstone of trustworthiness in tubing coupling products. Manufacturers adhere to rigorous quality control processes, conducting comprehensive inspections and testing at every production stage. Non-destructive testing methods such as ultrasonic and radiographic examinations are employed to detect any anomalies that might compromise the integrity of the couplings.
Furthermore, the traceability of materials and manufacturing processes is meticulously documented. This transparency not only enhances accountability but also enables drilling operators to trace any issues back to their source, facilitating swift resolutions and continuous improvements in product design and quality.
The Future of Tubing Couplings in the Global Energy Landscape
Looking forward, the demand for robust and efficient tubing couplings is set to grow in tandem with the escalating global energy requirements. The increasing exploration of unconventional reservoirs, such as shale and deepwater reserves, is likely to propel innovation in tubing coupling technology. Future developments may focus on smart couplings equipped with sensors that provide real-time data on operational conditions, further optimizing drilling operations and preempting potential failures.
Moreover, as the industry pivots towards sustainable energy solutions, tubing couplings must evolve to meet the demands of renewable energy sectors, such as geothermal energy extraction, where similar challenges of pressure and temperature are encountered.
In conclusion, tubing couplings are much more than mere connectors; they are pivotal engineering components that uphold the operational integrity of the oil and gas industry. Through continuous innovation, adherence to quality, and alignment with sustainable practices, they continue to serve as the backbone of efficient and effective energy extraction operations worldwide.