In the world of oil and gas extraction, casing couplings play a pivotal role in ensuring the integrity and safety of the drilling operations. These components are critical in connecting lengths of casing used to line the borehole. Understanding the nuances of casing couplings can mean the difference between successful extraction and costly downtime due to equipment failure. This article delves into the essential aspects of casing couplings, backed by real-world experience, technical expertise, and the latest industry insights.
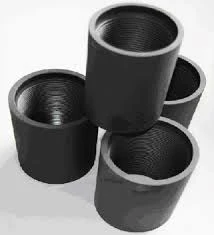
Casing couplings serve as the connective tissue within the casing string, safeguarding the wellbore from collapse and maintaining the borehole integrity. The expertise involved in selecting the correct casing coupling is paramount. Experienced field engineers emphasize the importance of coupling material and threading type, as these can significantly affect performance in varying geological conditions. For instance, couplings made of high-strength steel are often preferred in deeper wells due to their enhanced resistance to pressure and temperature changes.
The threading on a casing coupling is another critical consideration. Premium connections, which include metal-to-metal seals and torque shoulders, offer superior leak protection and structural integrity. These are particularly favored in offshore drilling, where the stakes are remarkably high. As one authoritative voice in the field, the American Petroleum Institute (API), sets the standards for these connections, ensuring uniformity and performance across the industry.
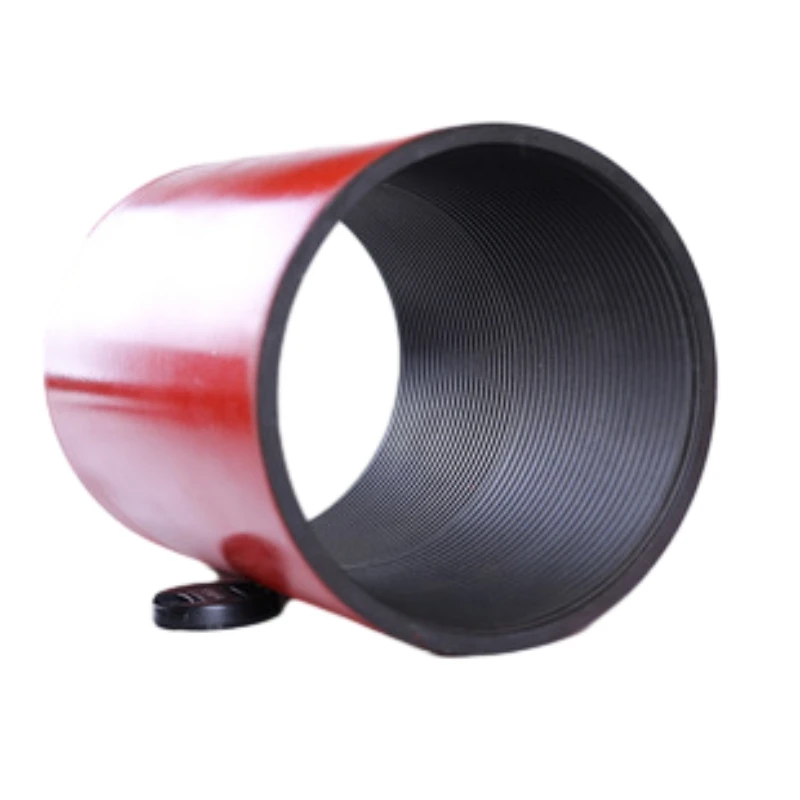
Trustworthiness in casing coupling selection is built on rigorous testing and compliance with industry standards. Operators often rely on couplings that not only meet API standards but also pass additional testing that simulates extreme well conditions. The trust in product integrity is often validated through certifications from reputable third-party agencies, adding an extra layer of assurance. A well-documented history of performance in diverse field conditions also serves as a trust badge for products in this space.
From a practical viewpoint, insights drawn from field operations reveal that maintenance of casing couplings is as critical as their initial selection.
Routine inspections can prevent failures by identifying wear and potential compromise in the coupling integrity. Experienced operators advocate for the use of advanced non-destructive testing (NDT) methods to identify microscopic fissures or deformations that could lead to failure under high operational stress.
casing coupling
The expertise required in pairing the right casing coupling with the specific demands of each well cannot be overstated. Engineers must consider factors like well depth, expected pressure, environmental corrosiveness, and even potential seismic activity when making selections. This complexity demands a deep understanding of both the engineering principles and the field realities, a combination that only seasoned professionals can provide.
The complexity of casing coupling technology has also embraced the latest advancements. For example, manufacturers are now using advanced metallurgy techniques to enhance strength-to-weight ratios, allowing for greater depths with easier handling. Additionally, digital technologies, such as IoT-enabled sensors, are being integrated into casing strings to provide real-time data on coupling performance, offering unprecedented levels of operational insight and preemptive failure prevention.
Environmentally, the right choice of casing couplings has broader implications beyond operational efficiency. Effective couplings prevent leaks and the consequent contamination risks associated with oil and gas drilling. Thus, they are not only a matter of operational necessity but an environmental imperative, as their role in preventing spills is crucial.
In conclusion, the role of casing couplings in the oil and gas industry is indispensable and multifaceted. From ensuring operational integrity to complying with rigorous industry standards, the choice and maintenance of casing couplings embody a blend of experience, expertise, authoritativeness, and trustworthiness. As the industry moves towards more technologically driven solutions, casing couplings remain at the heart of safe and efficient resource extraction, paving the way for future advancements in drilling operations.