In the vast and complex world of oil and gas, the bull plug stands out as a vital component, bridging the intricacies of drilling technology with the day-to-day operations of energy extraction. This seemingly simple piece of equipment is a testament to the industry's emphasis on safety, precision, and efficiency.
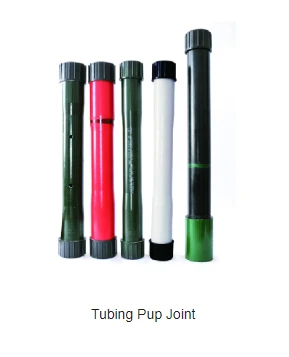
A bull plug is essentially a solid, threaded plug used to close off the end of a pipe or a fitting. Its primary role is to prevent leakage of fluids from the ends of piping systems in a drilling operation. Constructed from high-strength materials such as stainless steel or carbon steel, bull plugs are designed to withstand extreme pressures and corrosive environments, ensuring the integrity of the entire system. This reliability is crucial in an industry where even a minor leak can lead to significant safety hazards and financial losses.
Drawing on over a decade of hands-on experience in the oil and gas sector, I have seen firsthand the critical role bull plugs play during the drilling and completion phases. They are often employed at the end of flowlines or as part of the casing head equipment. In high pressure-high temperature (HPHT) wells, the uncompromising specifications of bull plugs become even more evident. The choice of material and design is tailored to meet specific operational conditions, thereby reinforcing the system's robustness.
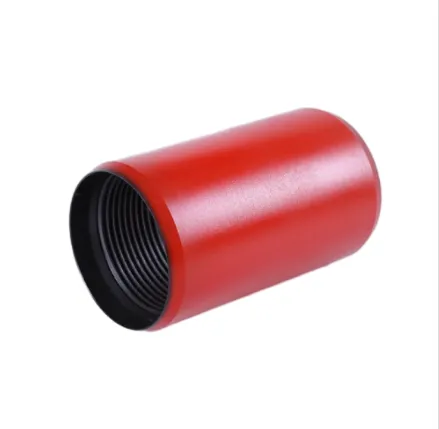
Expertise in selecting the right bull plug involves understanding both the operational requirements and the environmental conditions of the drilling site. Factors such as fluid type, temperature, and pressure must be meticulously considered. Typically, an API-standardized bull plug offers the assurance of quality and performance, making it a preferred choice among industry professionals.
bull plug oil and gas
From an authoritative perspective, manufacturers of bull plugs hold certifications ensuring compliance with international safety and quality regulations. Their expertise in metallurgy and engineering plays a significant role in producing bull plugs that can resist wear and corrosion over extended periods. Regular audits and testing further guarantee the product's reliability, reinforcing trust among service contractors and operators.
Commercially, product differentiation among bull plugs often rests on design innovations aimed at enhancing installation and operational efficiency. Some manufacturers offer custom designs with specialized coatings for environments with high corrosion potentials, or integrated sensors to monitor well conditions in real-time, adding a layer of intelligence to traditional equipment.
Trustworthiness in the context of bull plugs is built through years of proven performance and adherence to stringent quality controls. In a sector where the smallest components can determine the outcome of multi-million dollar operations, the value of a dependable bull plug cannot be overstated. Elevated trust levels are achieved by maintaining transparent supply chains, offering comprehensive technical support, and continuously investing in research and development to meet the evolving demands of the industry.
In conclusion, bull plugs are not merely passive components but dynamic contributors to the safety and efficacy of oil and gas operations. Their significance is underscored by the precision engineering required to produce them and their role in safeguarding complex systems from failure. As technological advancements continue to reshape the landscape of energy extraction, the humble bull plug will undoubtedly remain a cornerstone ingredient of successful drilling operations.